[ad_1]
I’m again at this time to indicate you the remainder of the method for making lined, pinch-pleated curtains, and I’ll present you each element of the way to end the curtains and dangle them. I need to say up entrance that this submit incorporates an absurd quantity of pictures (74 to be actual), however please don’t let that intimidate you! This course of isn’t troublesome in any respect, however I needed to incorporate a number of pictures in order that you could possibly simply perceive each little step of the method. However once more, including pleats and ending up a material panel shouldn’t be troublesome. Simply take it one small step at a time, and also you’ll get it!
NOTE: That is Half 2 of a two-post tutorial. Click on under to see Half 1 of this tutorial for lined, pinch-pleated curtains.

Yesterday, I left off with the physique of the material panel completed for probably the most half, and unfold out on my work desk like this. The hems had been completed, the face material and the liner had been sewn collectively, and I used to be virtually able to sort out the pleated header.
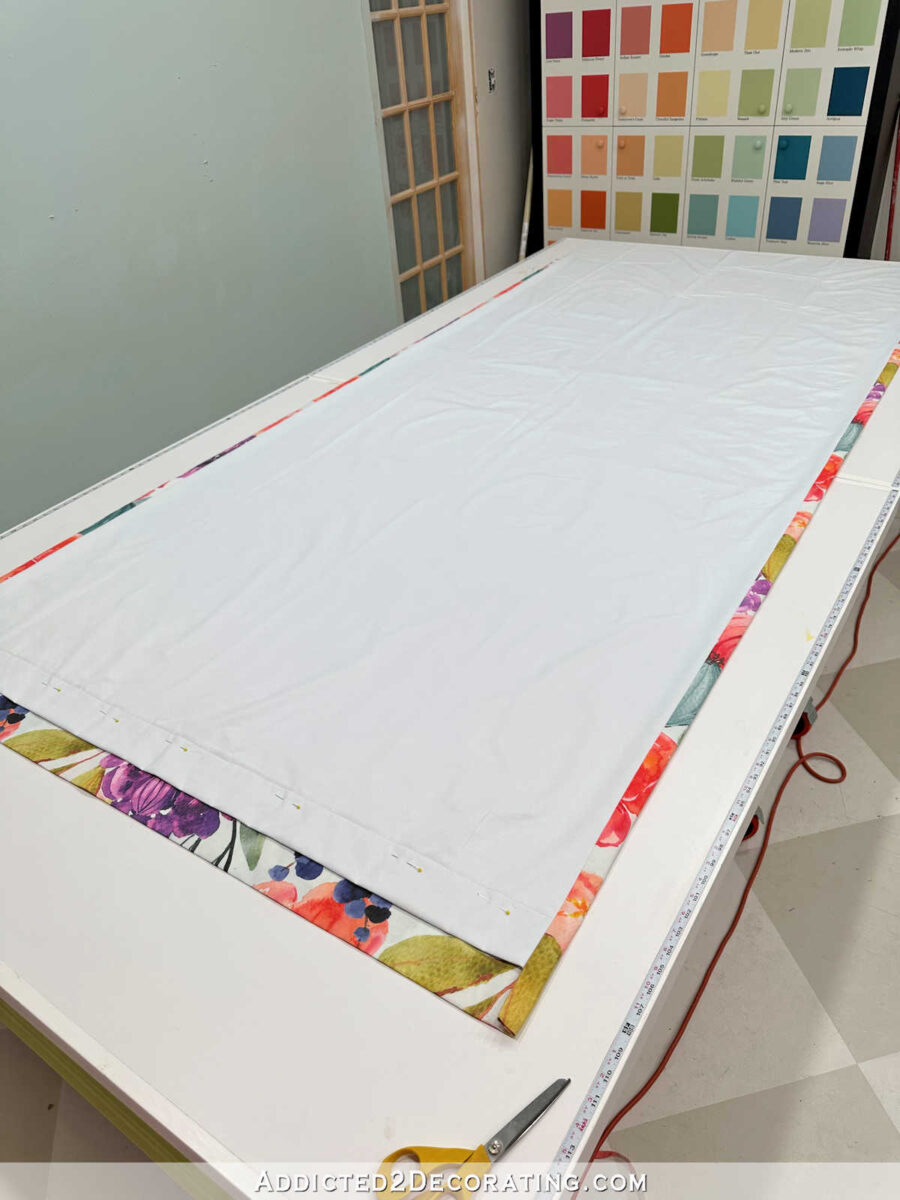
The one factor I nonetheless wanted to do earlier than engaged on the pleated header was to iron within the facet seams to get that actually sharp crease on the facet edges of the panel. I actually took my time with this and didn’t rush this step as a result of these sides need to be proper to ensure that the material panel to hold correctly. And once more, that lining wants to increase all the best way to that outdoors ironed-in crease alongside the very edge. The entire folds are within the material, not on the liner.
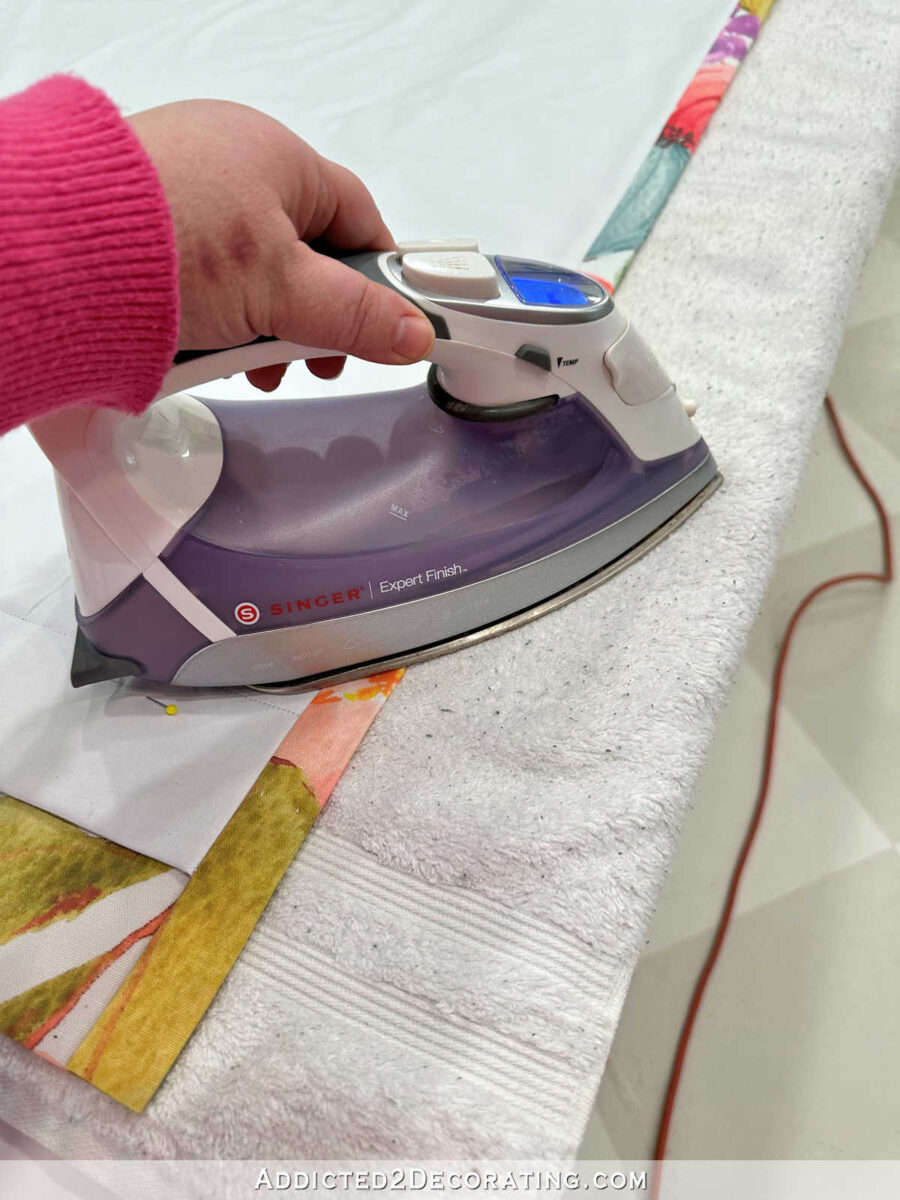
With these sides ironed and the panel mendacity flat, face material down and lining up, I measured and marked my completed material size. When you’ll keep in mind, I had taken this measurement proper on the very starting. You possibly can refer again to Half 1 for those who don’t keep in mind.
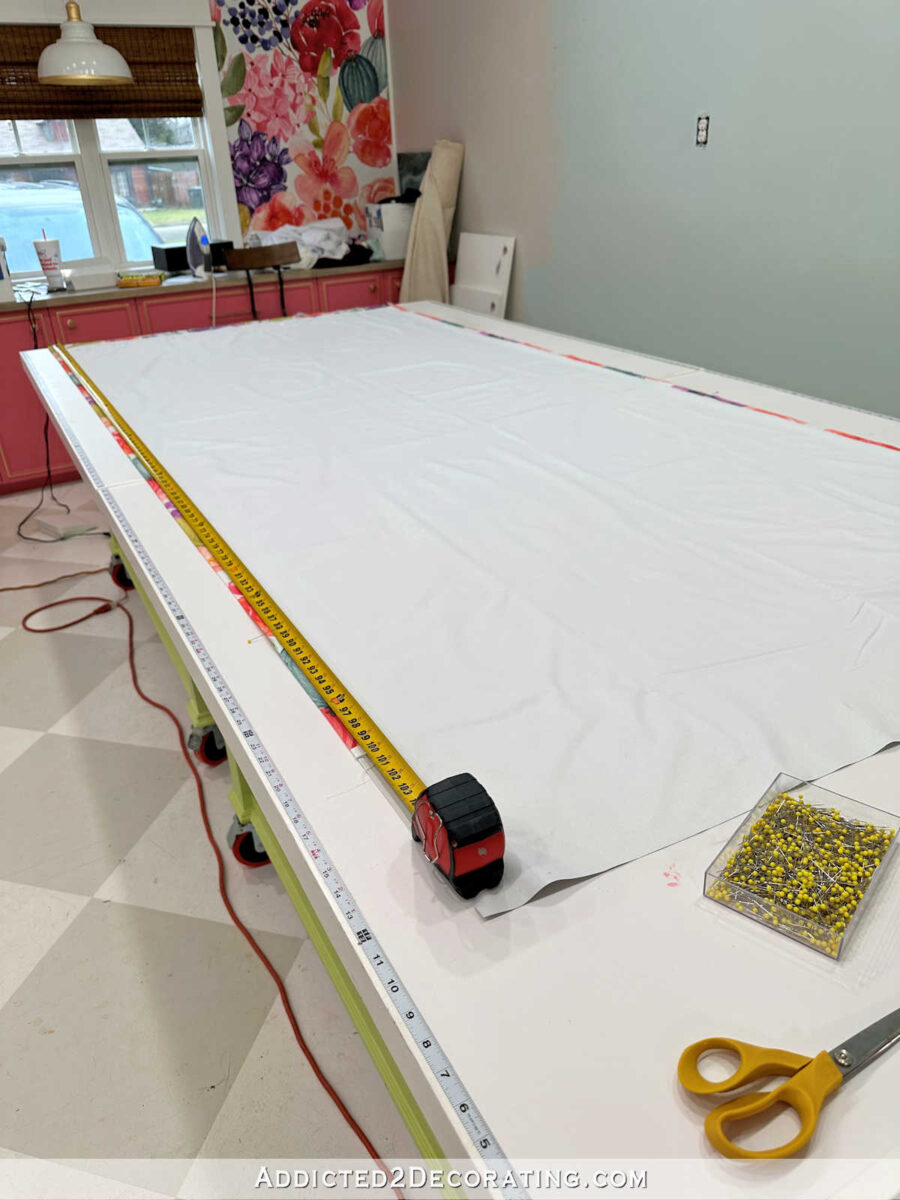
My completed material panel size was 88 5/8 inches, so I measured and marked all sides of the panel with a pin at that measurement.
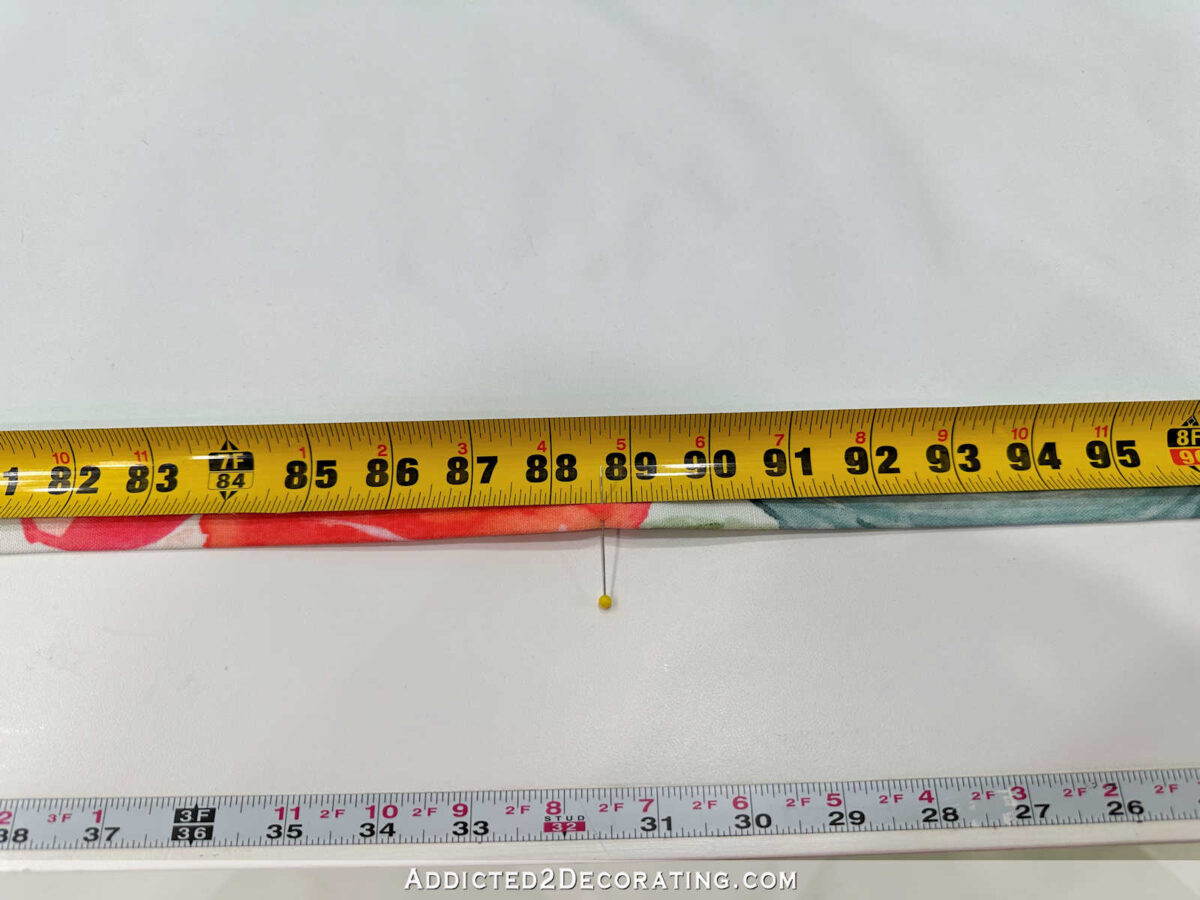
For now, I simply did one measurement and one pin on all sides of the panel.
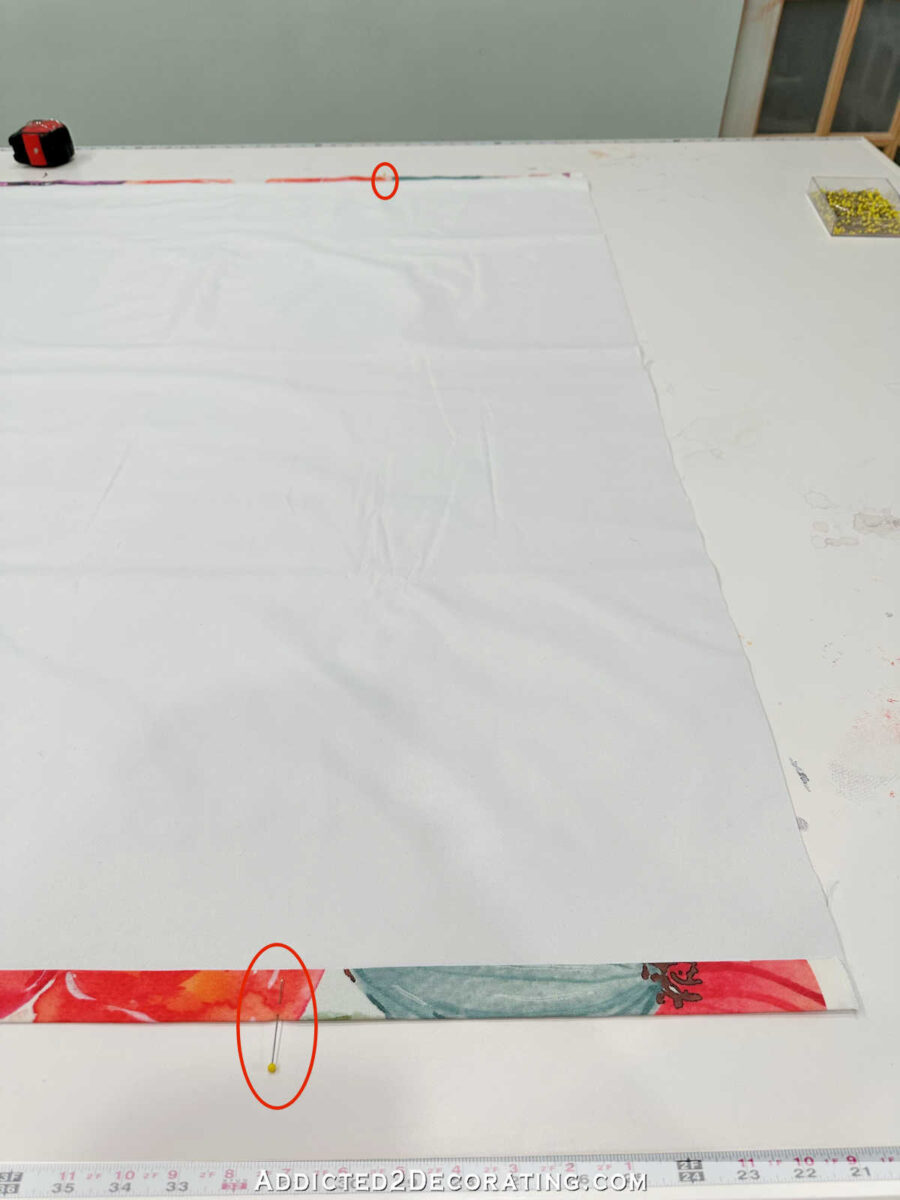
Subsequent, I folded the material over proper at these pins and repinned all sides into place via all layers of the material.

After which I measured and pinned the completed top on the remainder of the panel.
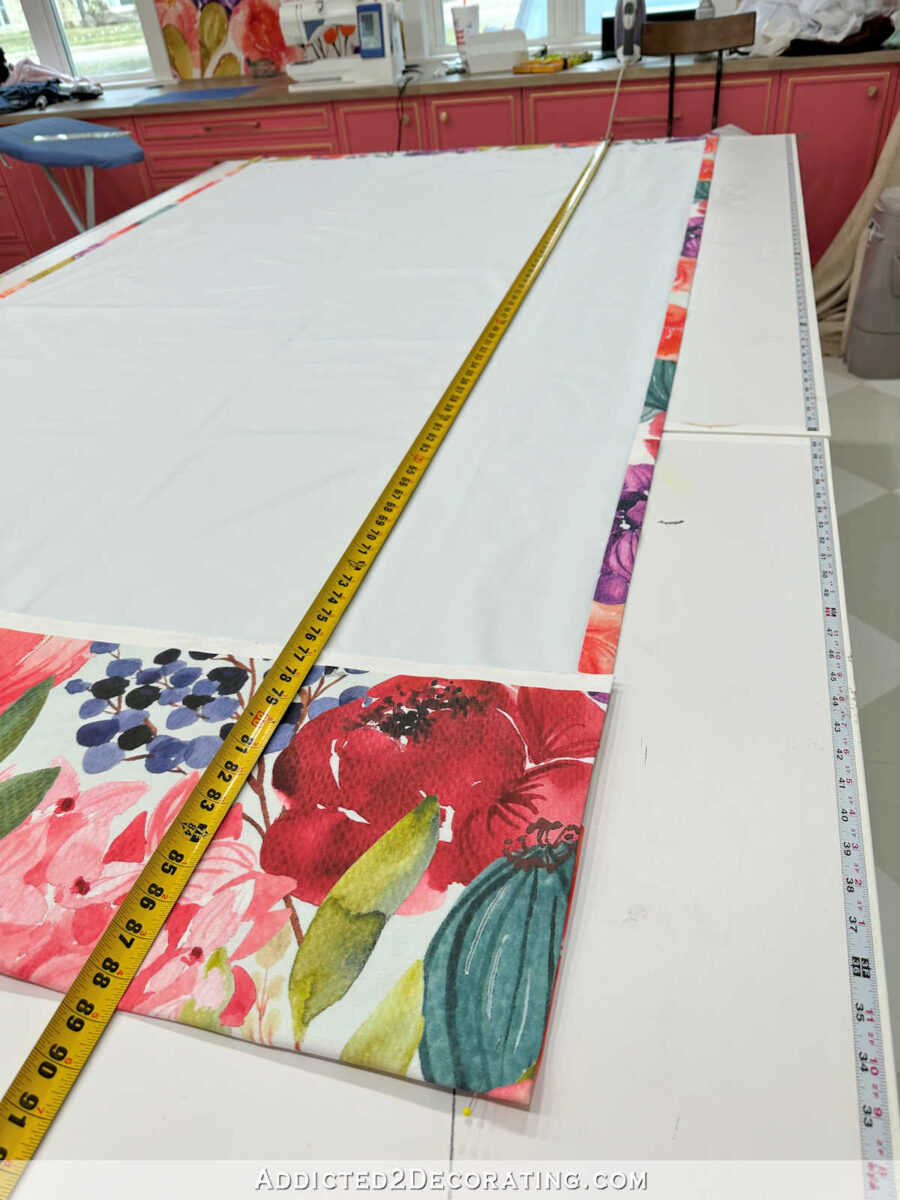
I solely wanted to make solely slight changes within the fold as I moved my approach throughout the highest of the panel.
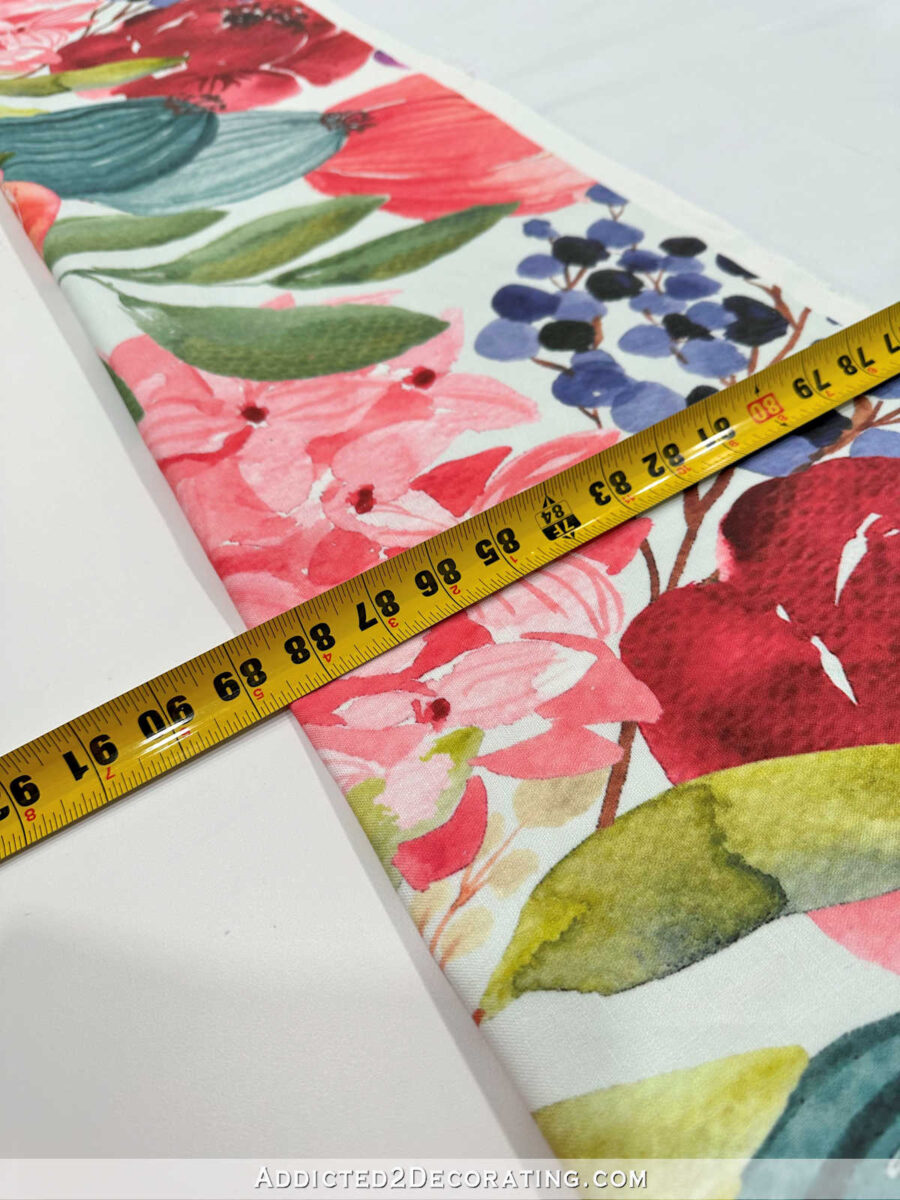
As soon as I had your entire high folded to the proper measurement and pinned into place, I steam ironed that fold within the high, eliminated the pins, and ironed it once more to ensure I had a really sharp crease.
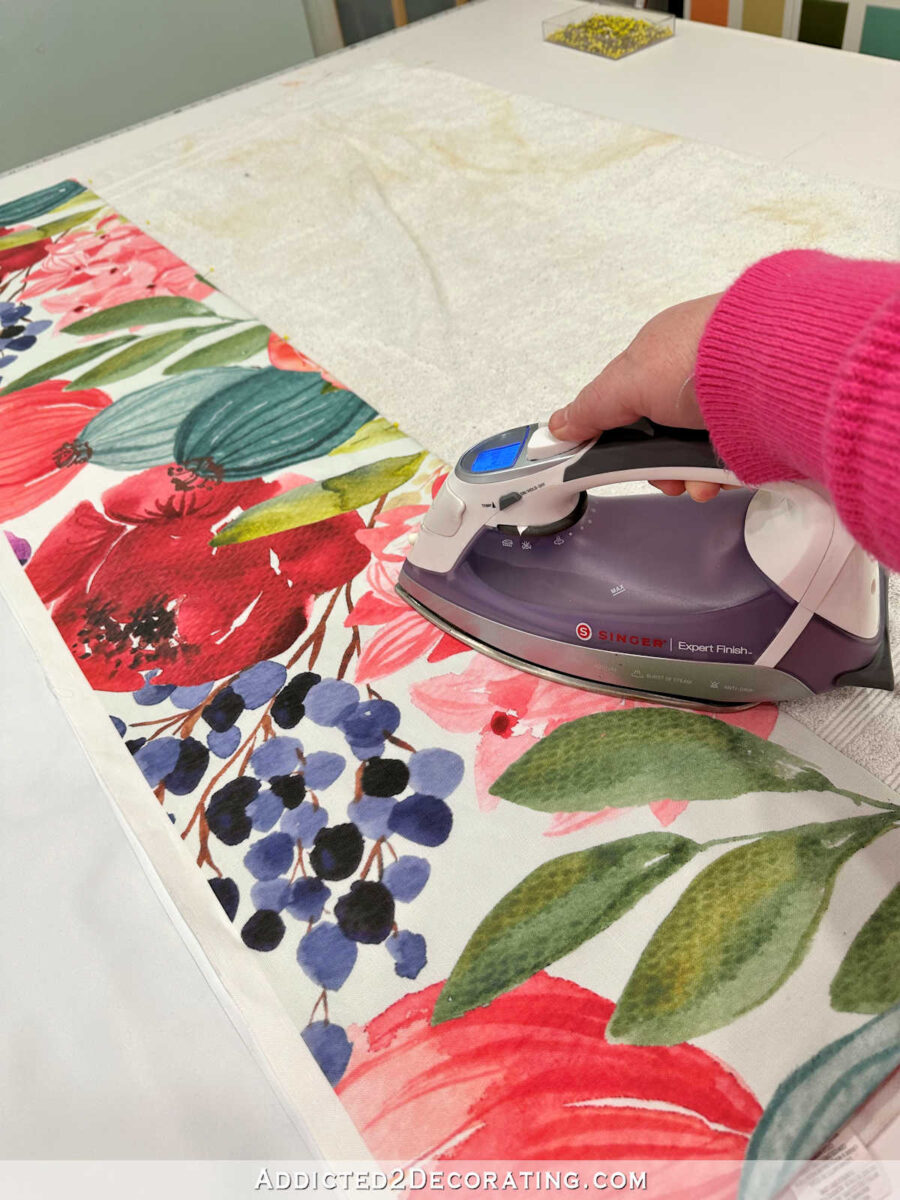
So at this level, right here’s what the highest of the panel seemed like from the again — no pins and a really sharp ironed-in fold alongside the very high fringe of the panel.
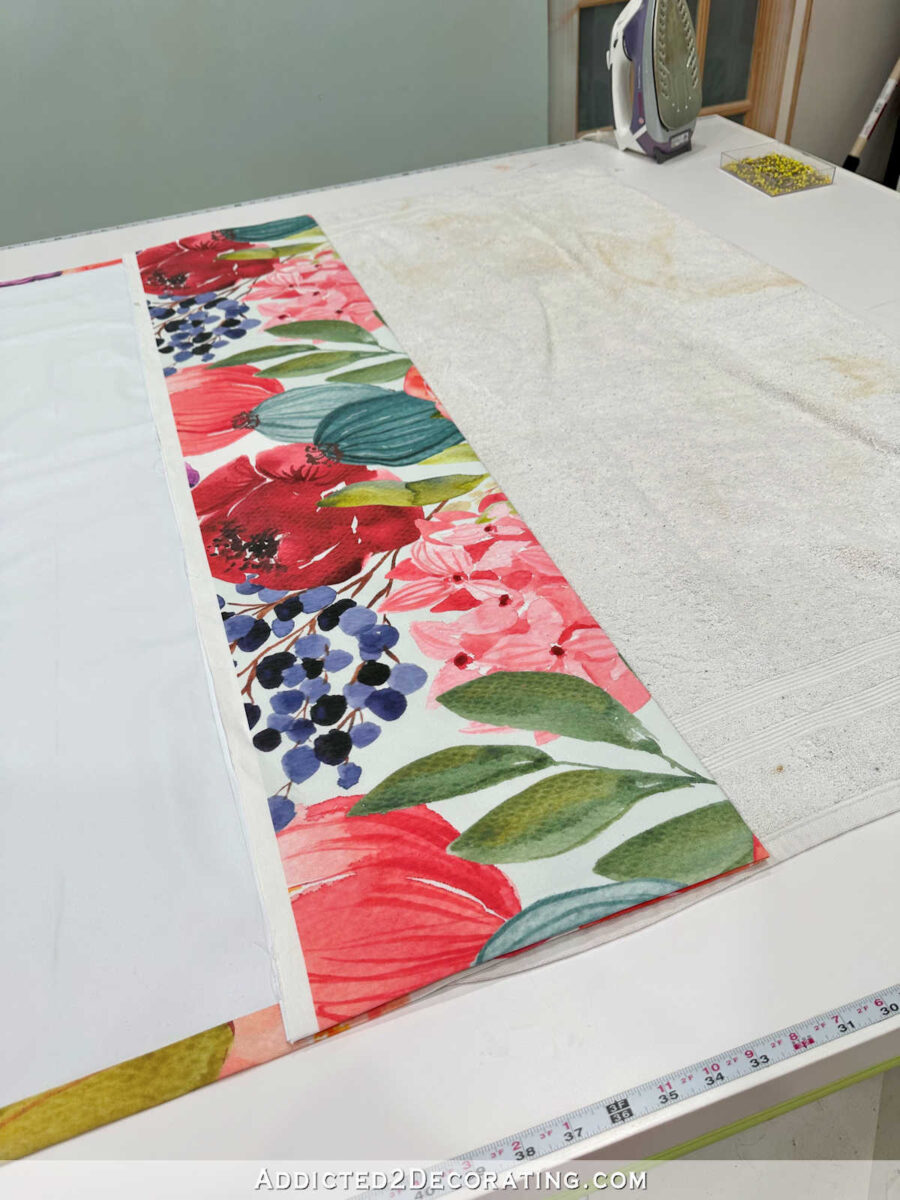
Subsequent, I unfolded the highest and made positive I might see the crease all the best way throughout the panel. (I edited this photograph to reinforce the road in order that you could possibly see it. In particular person, the ironed-in crease was very simple to see.)
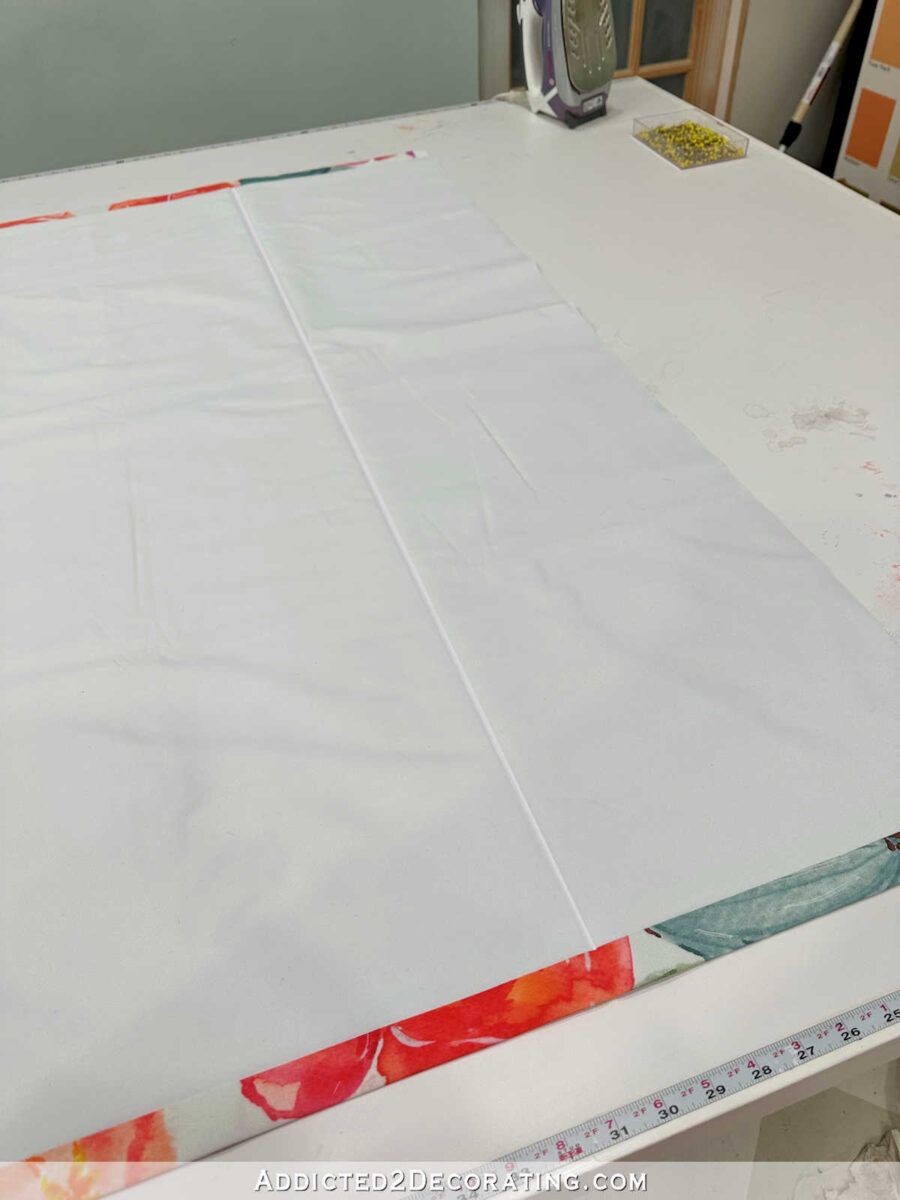
Then I eliminated the stitching holding the face material to the liner from the very high right down to that ironed-in crease.
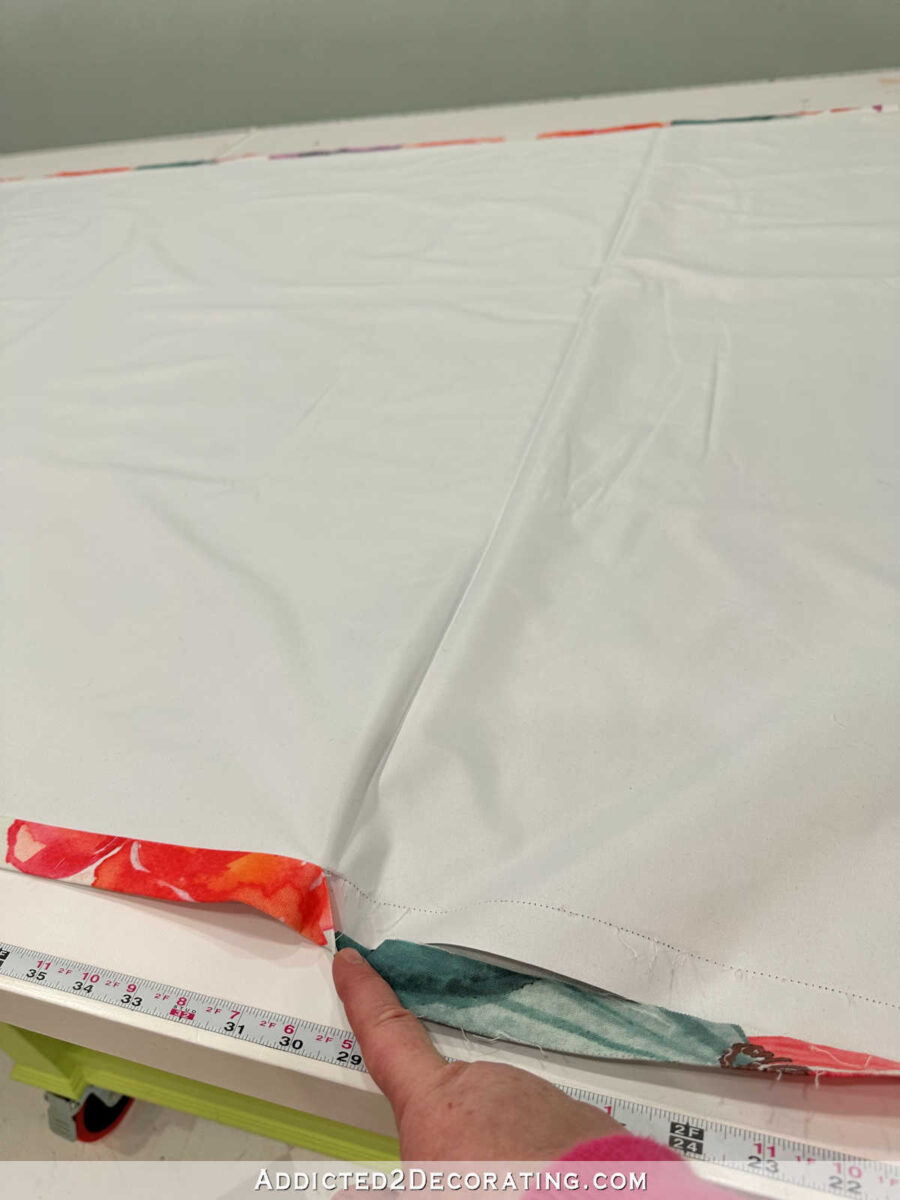
After which I used that ironed-in crease as a information to chop off the surplus lining. I don’t suppose that is 100% essential, however I at all times take away the surplus as a result of it can create two extra layers of material to wrangle into pleats later, and that simply creates pointless bulk that makes pleating tougher than it must be.
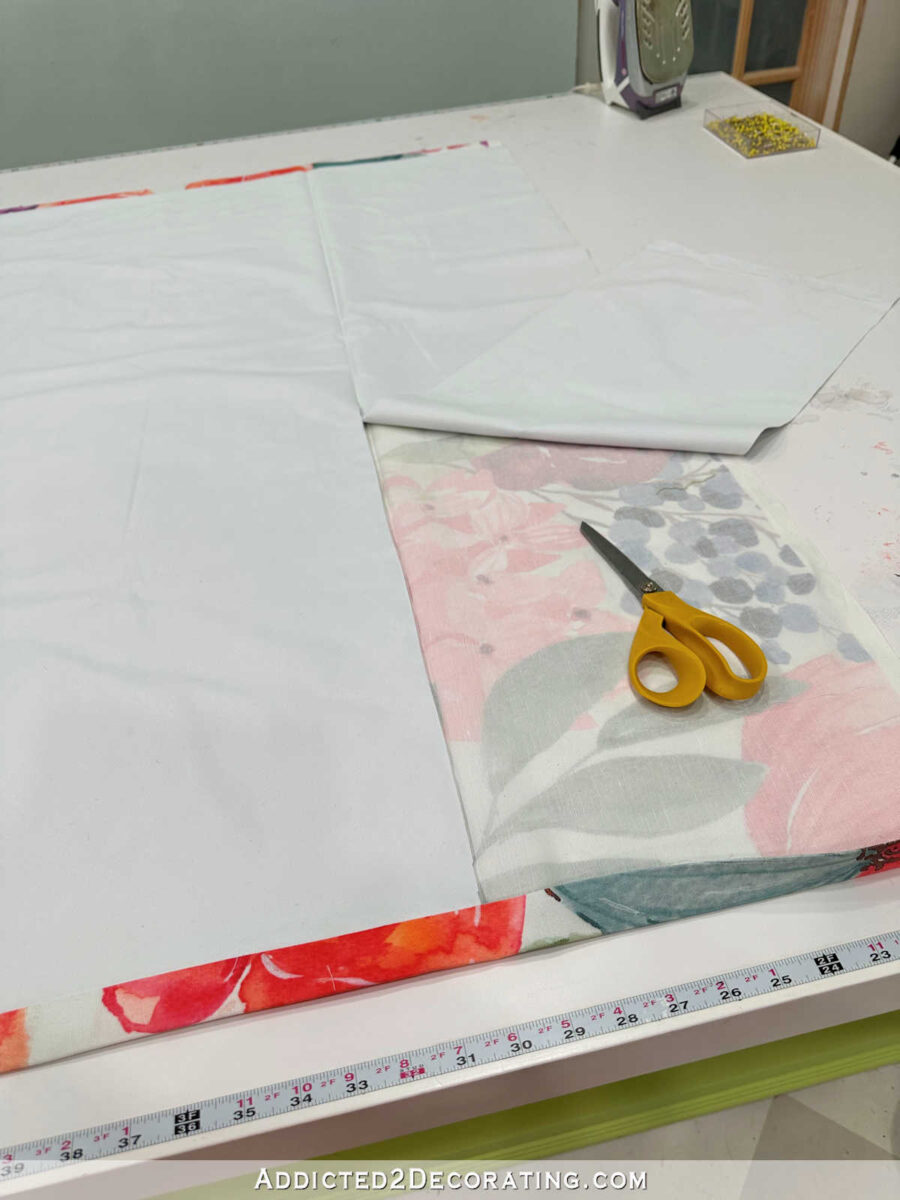
Subsequent, I reduce my material header tape to size. This can be a thick-ish materials that feels quite a bit like a heavy interfacing. You may get it in several widths, however I choose the three-inch width. You should purchase it by the yard at locations like Joann Materials.
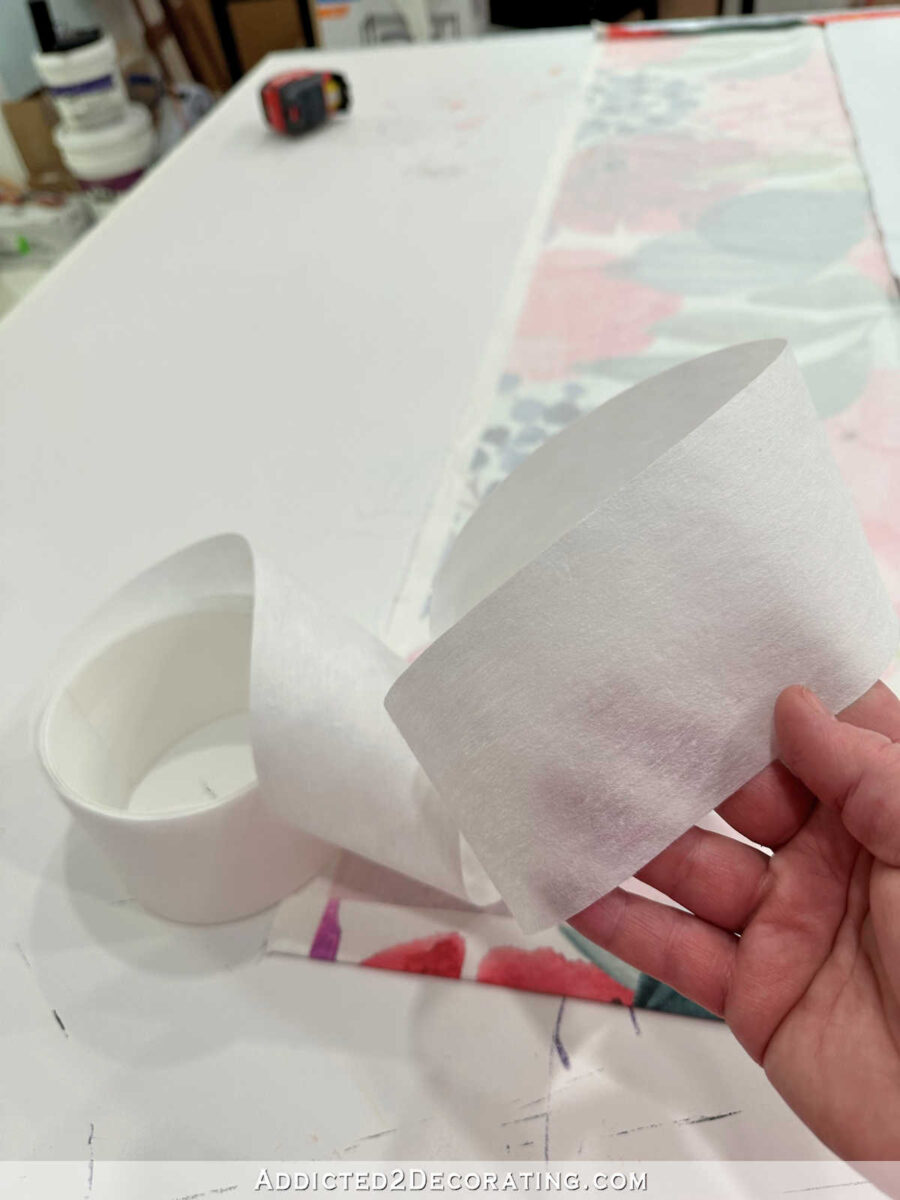
I reduce it to size in order that it spans the width simply contained in the 1-inch facet folds.
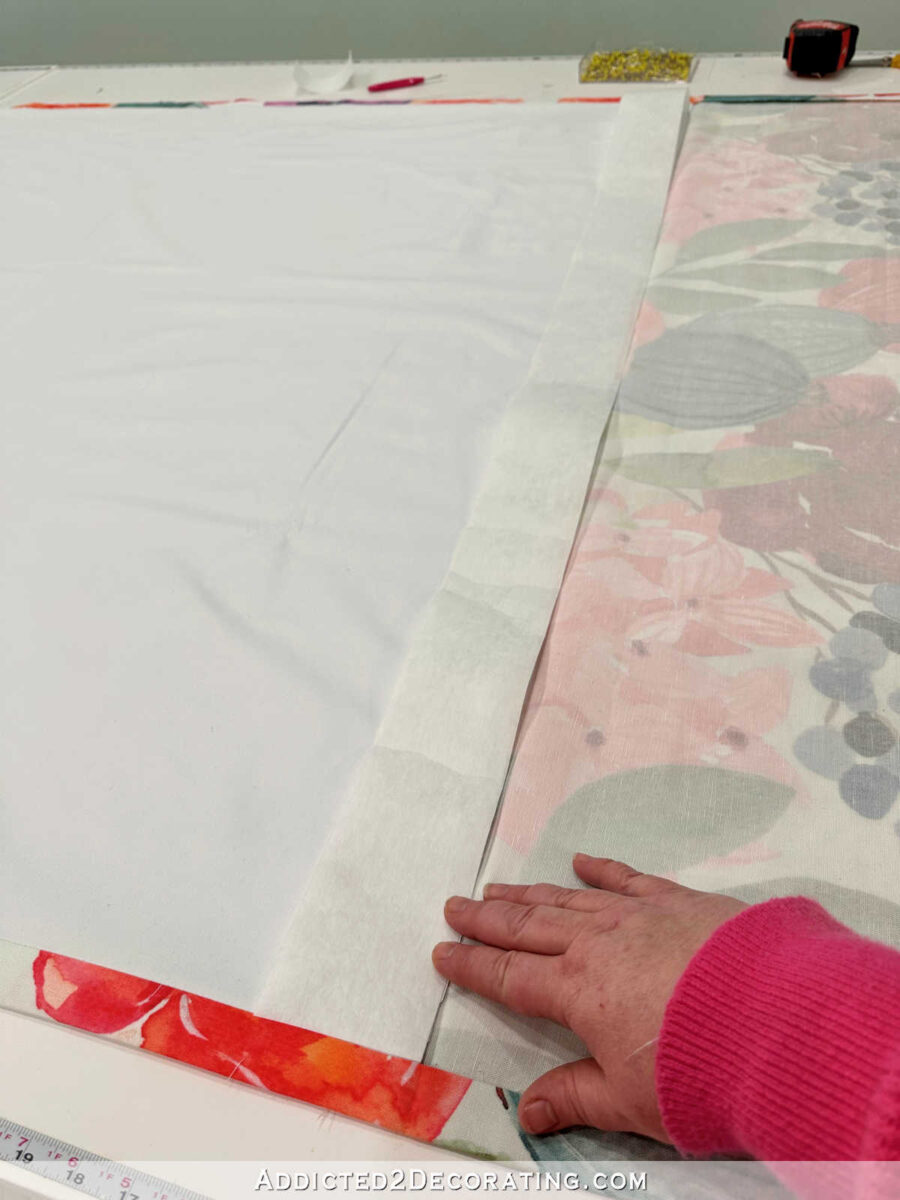
Since my header tape is three inches extensive, that meant that I wanted to chop away a few of the extra material on the high. The material wants to increase previous the highest of the reduce lining at a measurement equal to 2 instances the header tape width, minus only a smidge. (That’s the technical time period for it. ) Since I used to be utilizing three-inch header tape, I reduce the material to 6 inches minus a smidge (about 5 7/8 inches) previous the reduce fringe of the liner.
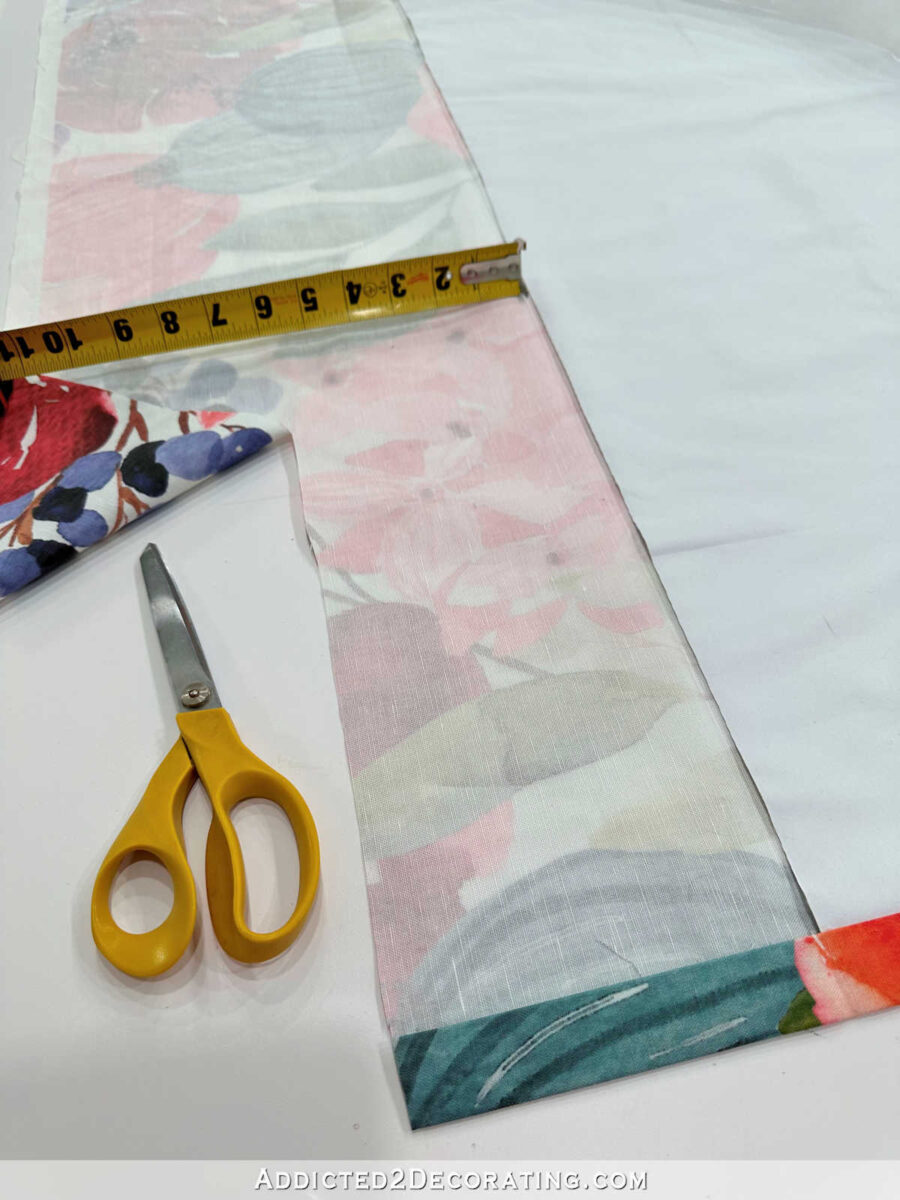
So as soon as I had the surplus reduce off and it seemed like this, I used to be prepared so as to add the header tape.
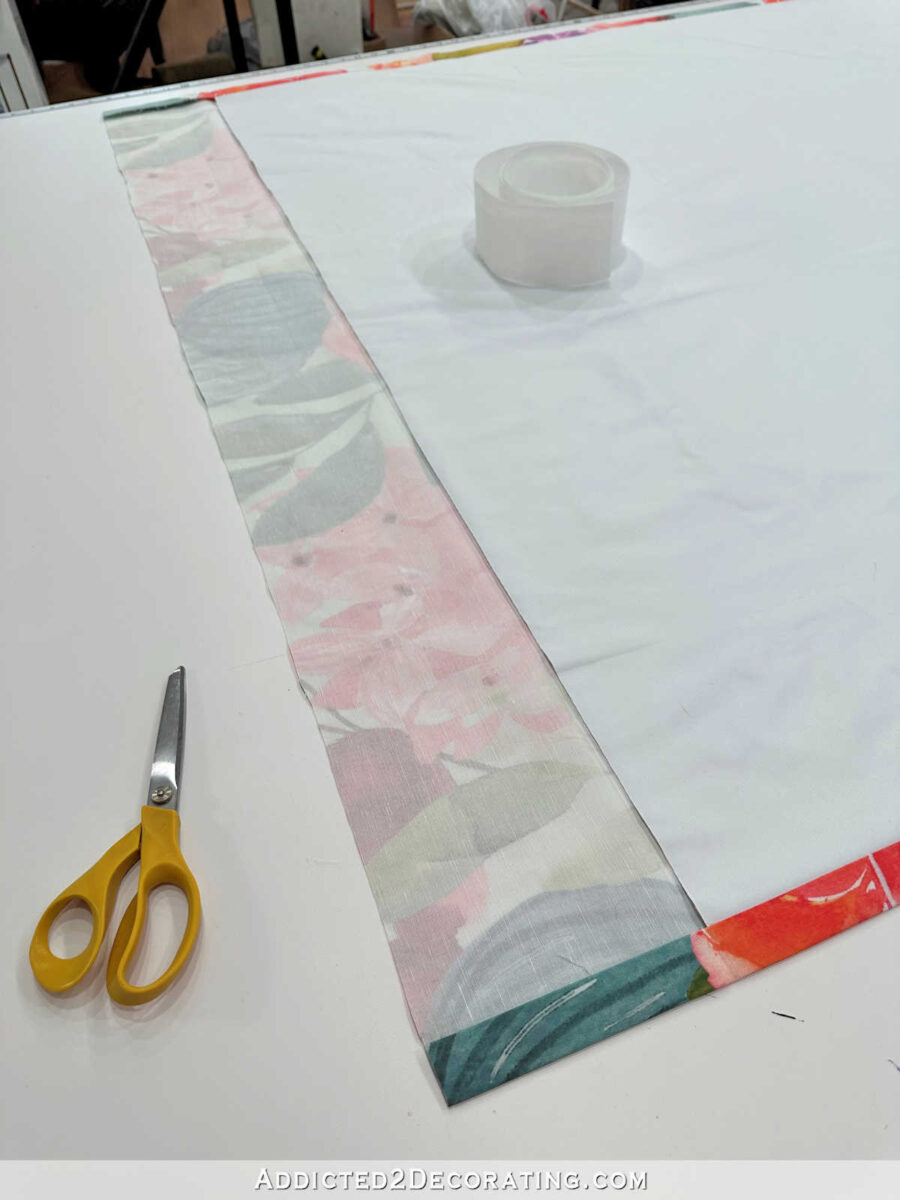
I began by putting the header tape in order that it lined up alongside the highest of the liner…
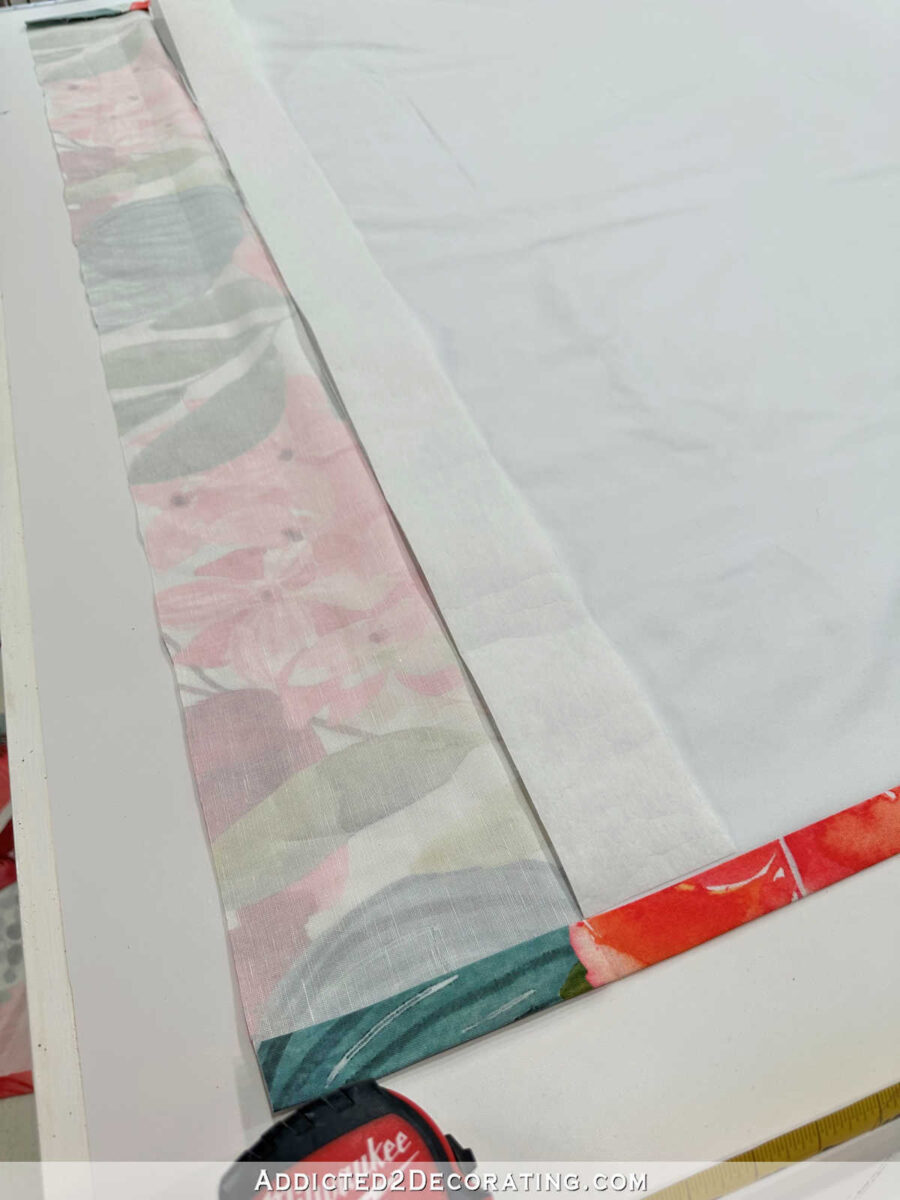
After which I folded the material down over the header tape alongside the ironed-in crease…
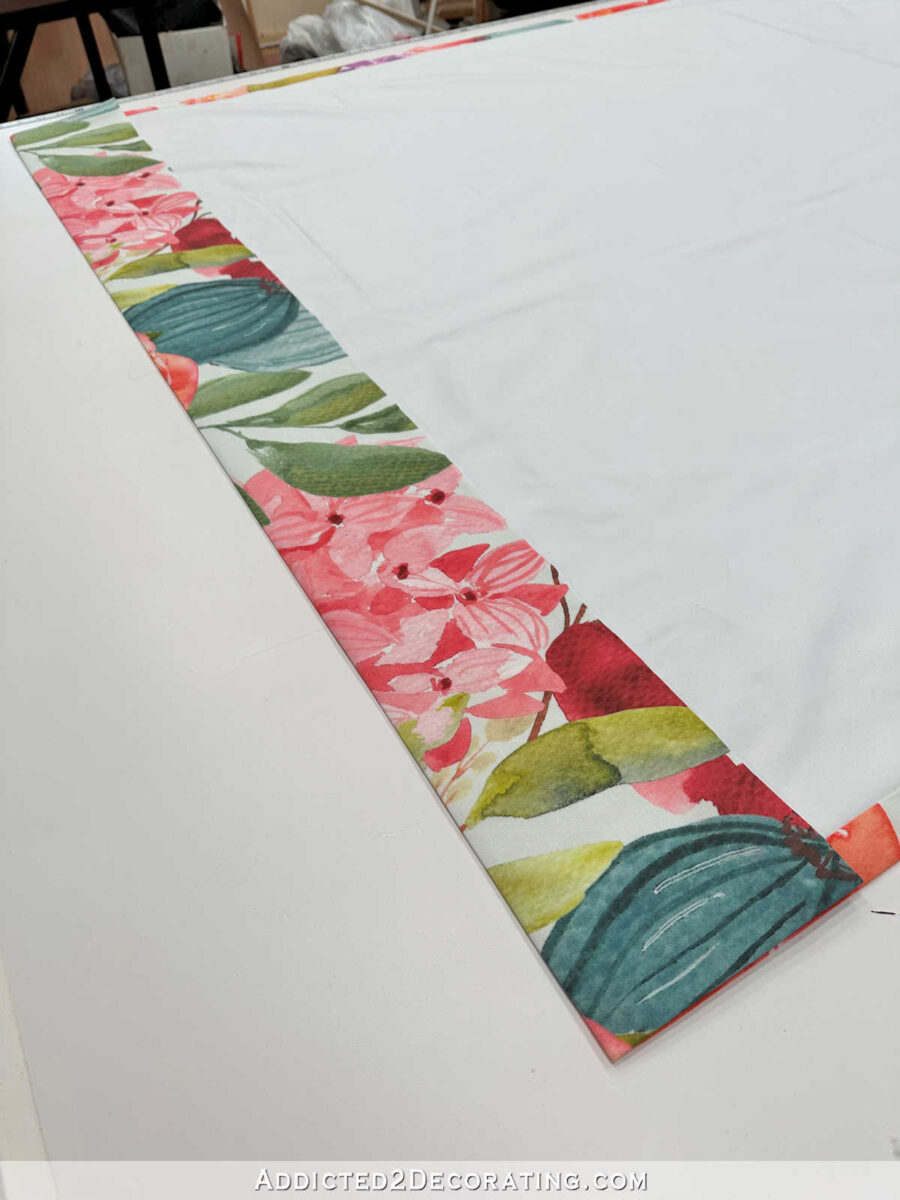
After which beginning within the center and dealing my approach out to the ends, I wrapped the surplus material again below the header tape in order that the material enveloped the header tape. After which I pinned all of the layers into place.
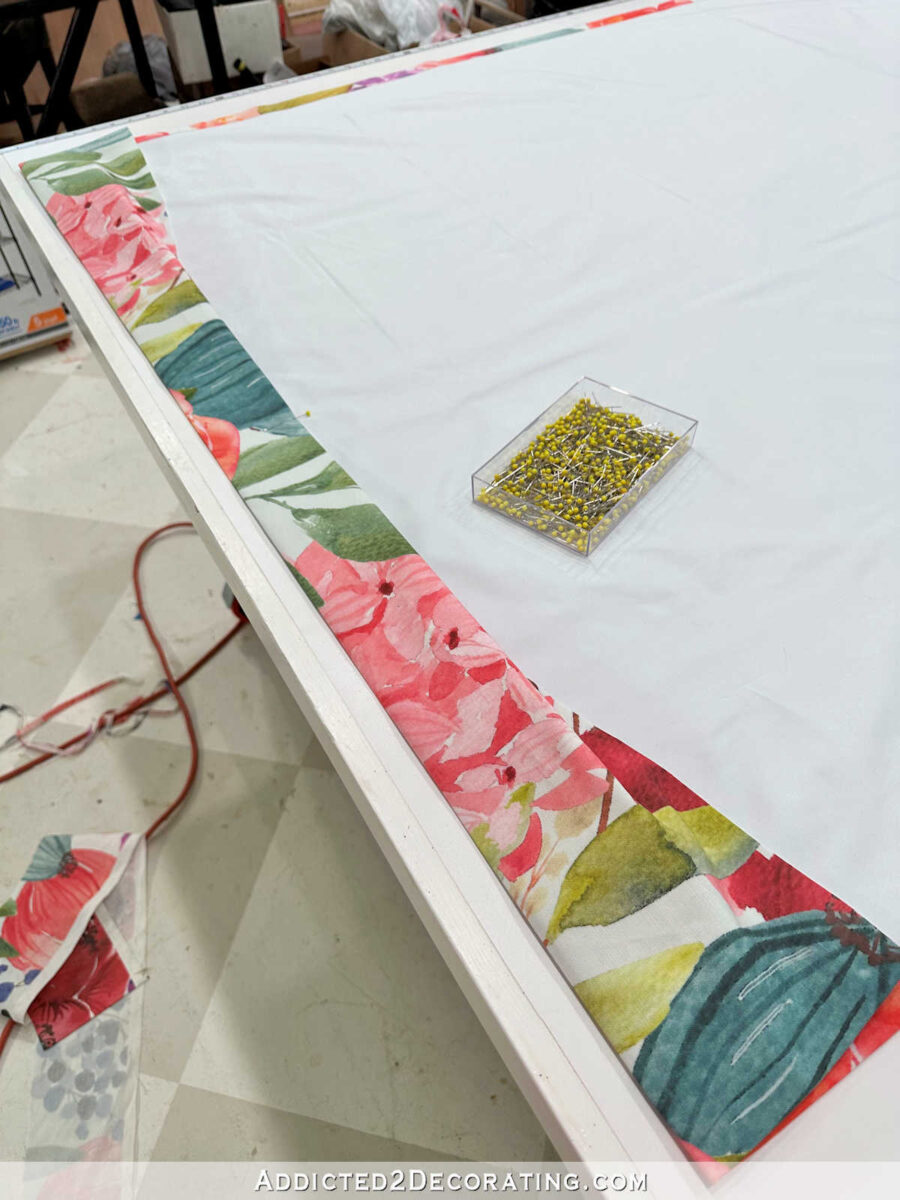
And right here’s what it seemed like as soon as it was pinned into place all the best way throughout.

Subsequent, I needed to determine the position of my pleats. The primary measurement I wanted was the return for the skin fringe of the panel. The return is the piece that folds again from the curtain rod and meets the wall. To get this measurement, merely measure from the tiny material pin loop on the curtain ring to the wall. It’s onerous to see from the attitude within the photograph under, however the measurement from the wall to my curtain rod/rings is 3 1/4 inches.
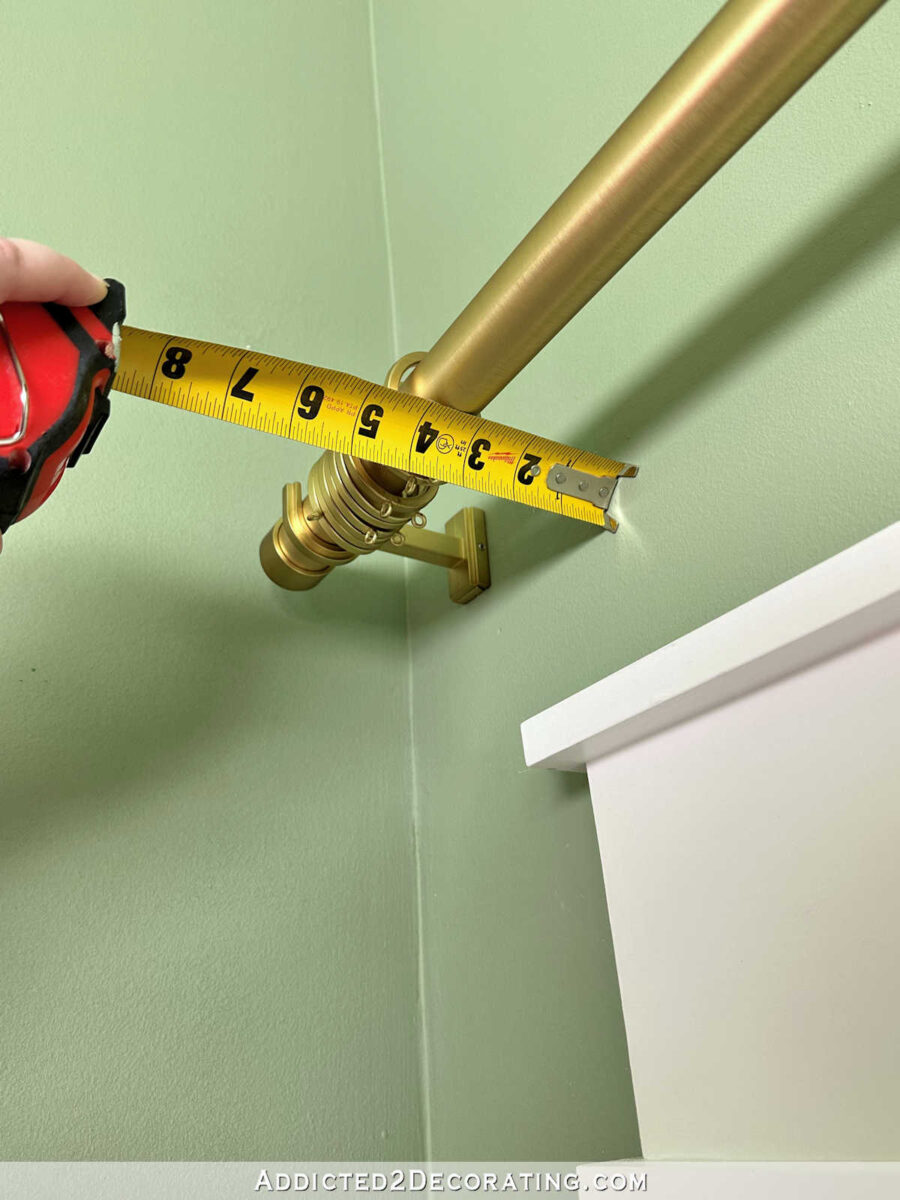
So I took that measurement and marked off 3 1/4 inches on the outer fringe of the header.
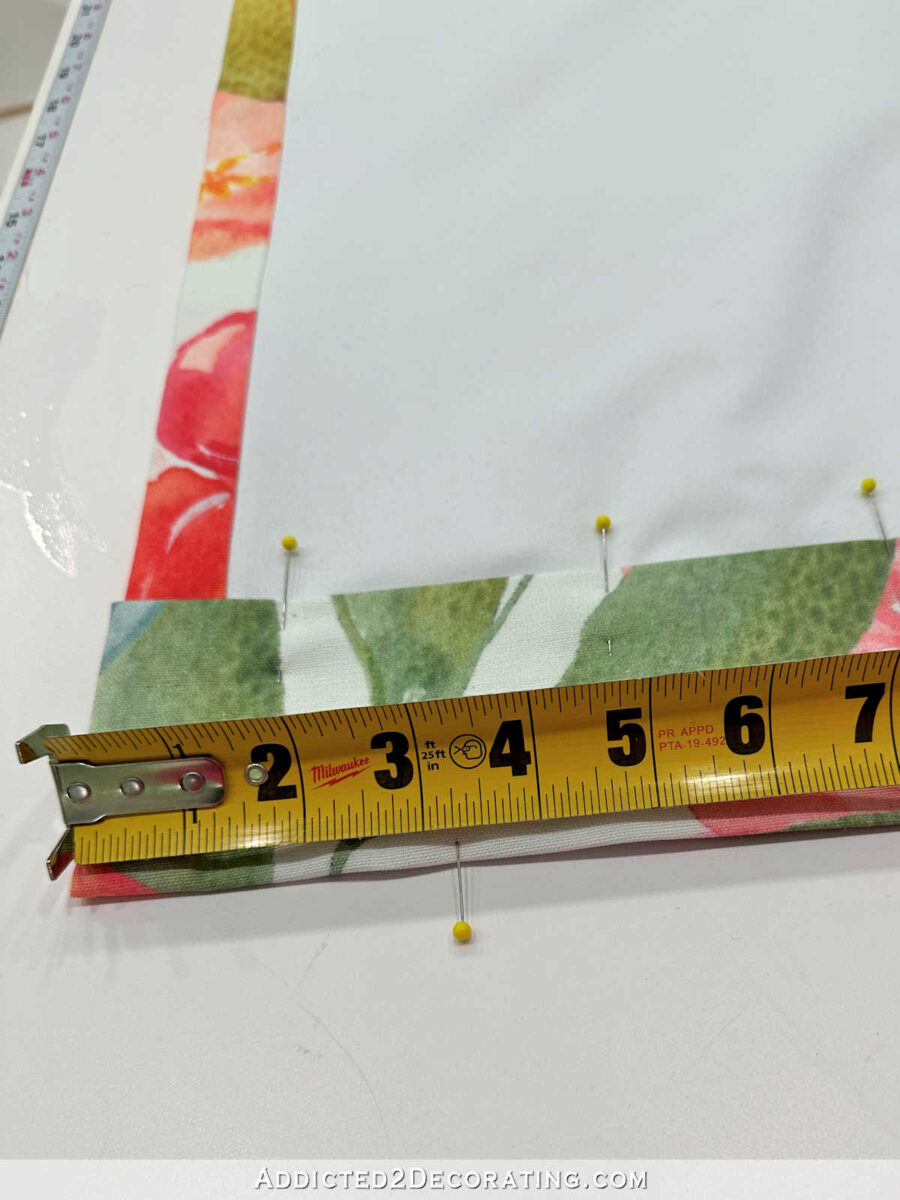
After which I measured and marked off an area on the vanguard (the within edge) of the header. I simply went with 2.5 inches as a result of I feel that appears good. However you’ll be able to regulate relying on what you suppose appears good.
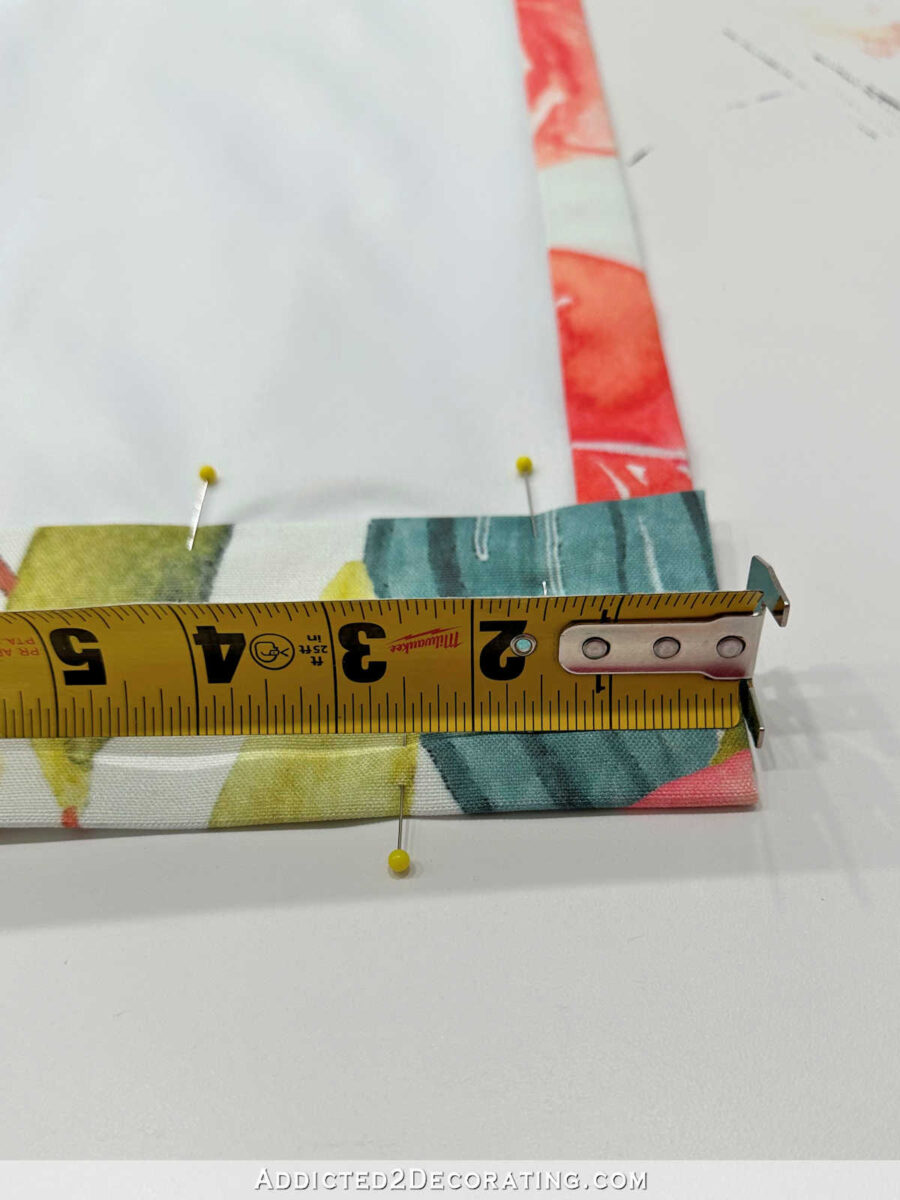
Or for those who’re including trim to the vanguard of your material panel (which wanted to be carried out a number of steps in the past), you would possibly want to regulate this measurement relying on the width of the trim. The very last thing you need is getting an ornamental trim caught up in your first pleat. Coping with that bulk in a pleat could be a nightmare, and it just about by no means appears proper. Ask me how I do know. However anyway, about 2 1/2 to three inches for that vanguard will do.
As soon as I had the return and the vanguard marked off, I measured the width remaining between these pins. So I positioned my tape measure proper on a kind of pins…
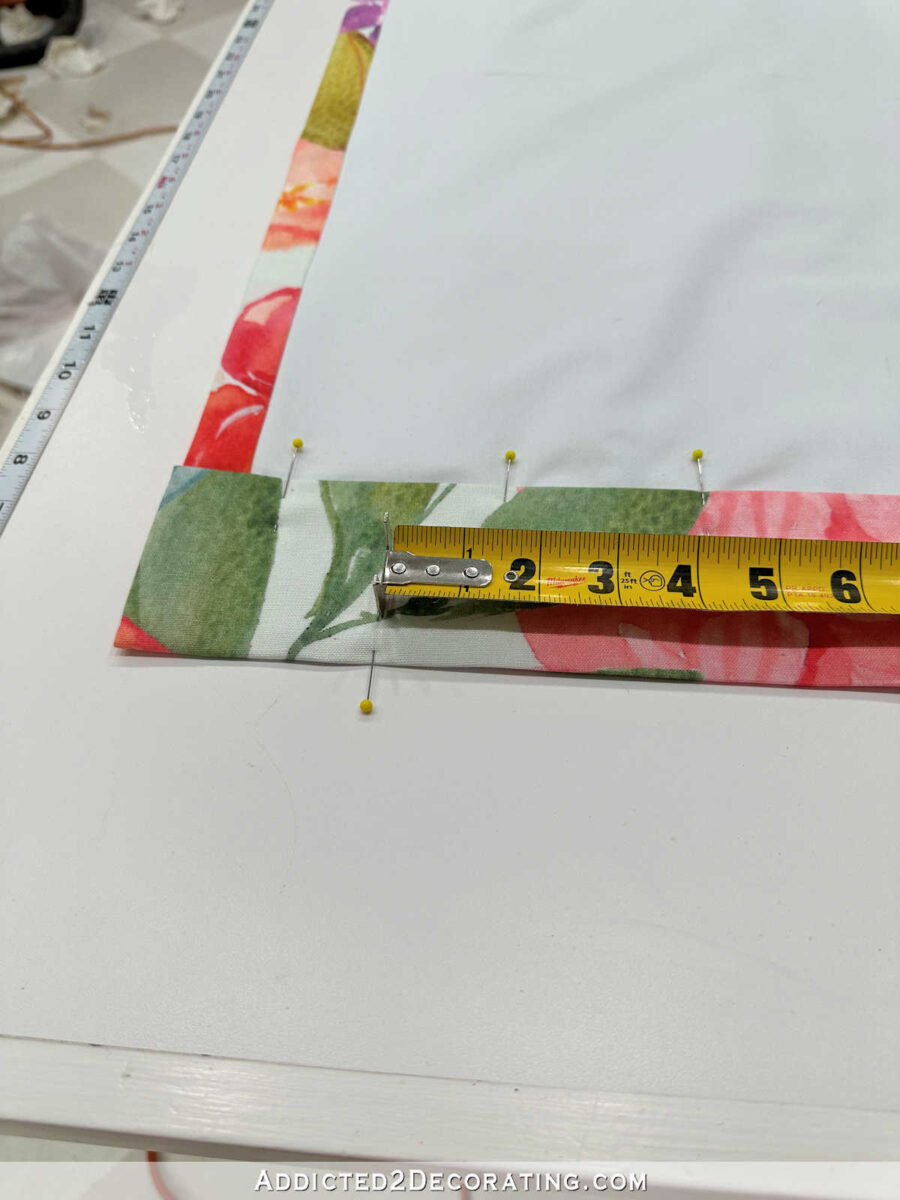
And measured to the opposite one. That gave me a measurement of 43.5 inches. (Once more, the attitude on the photograph under makes that look a bit off.)
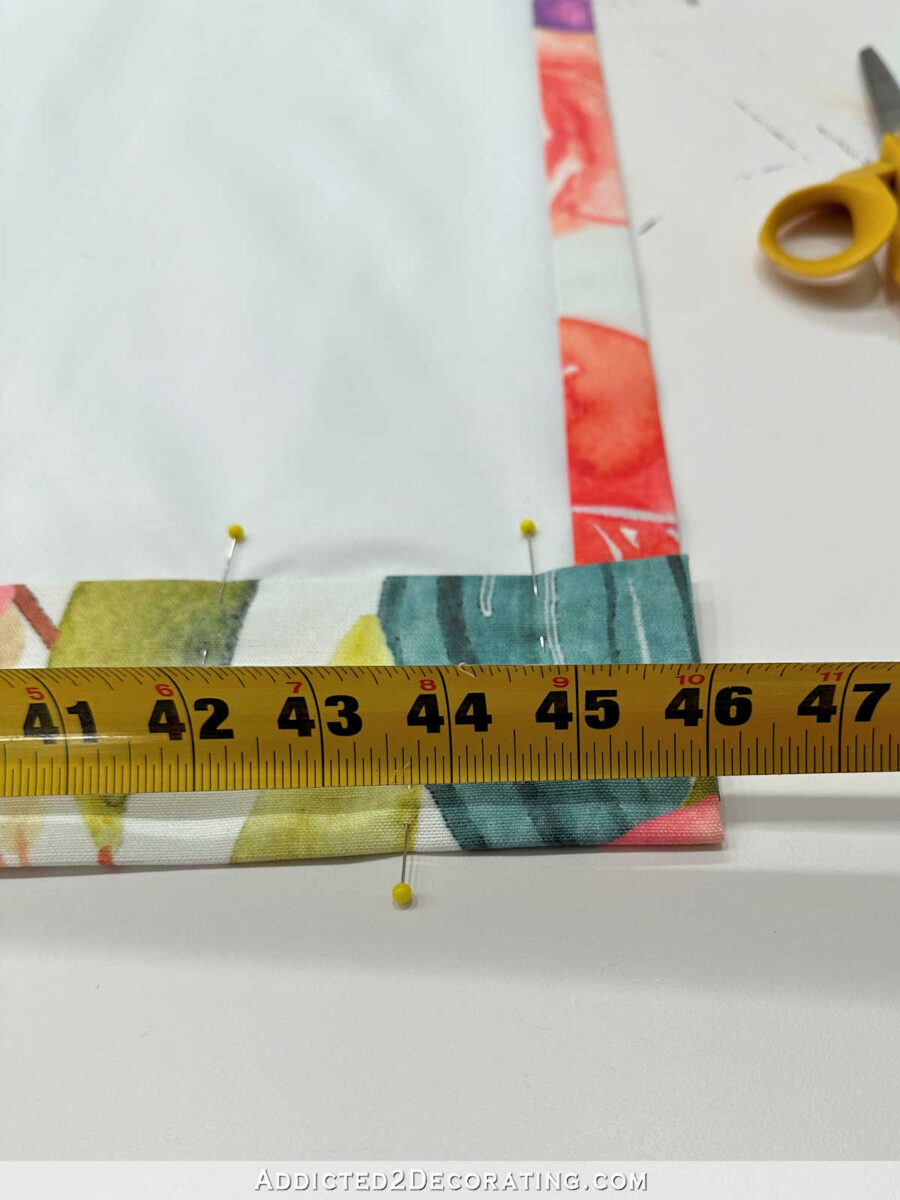
On a single width material panel, I prefer to have seven pleats. And I prefer to have a minimal of three inches of material width to work with per double pleat, or a minimal of three.5 inches per triple pleat. I made a decision to make use of double pleats on these material panels, so I multiplied 7 (pleats) instances 3 (inches per pleat), which meant that I wanted a complete of 21 inches for my pleats. That left me with 22 1/2 inches of material that wanted to be divided by 6 areas between the pleats. (If I’ve seven pleats, I might have six areas. If I’ve 9 pleats, I might have eight areas. So the variety of areas is at all times one lower than the variety of pleats.) So 22 1/2 divided by 6 signifies that every house wanted to be 3.75 inches extensive.
So I used my pins to mark off these areas.
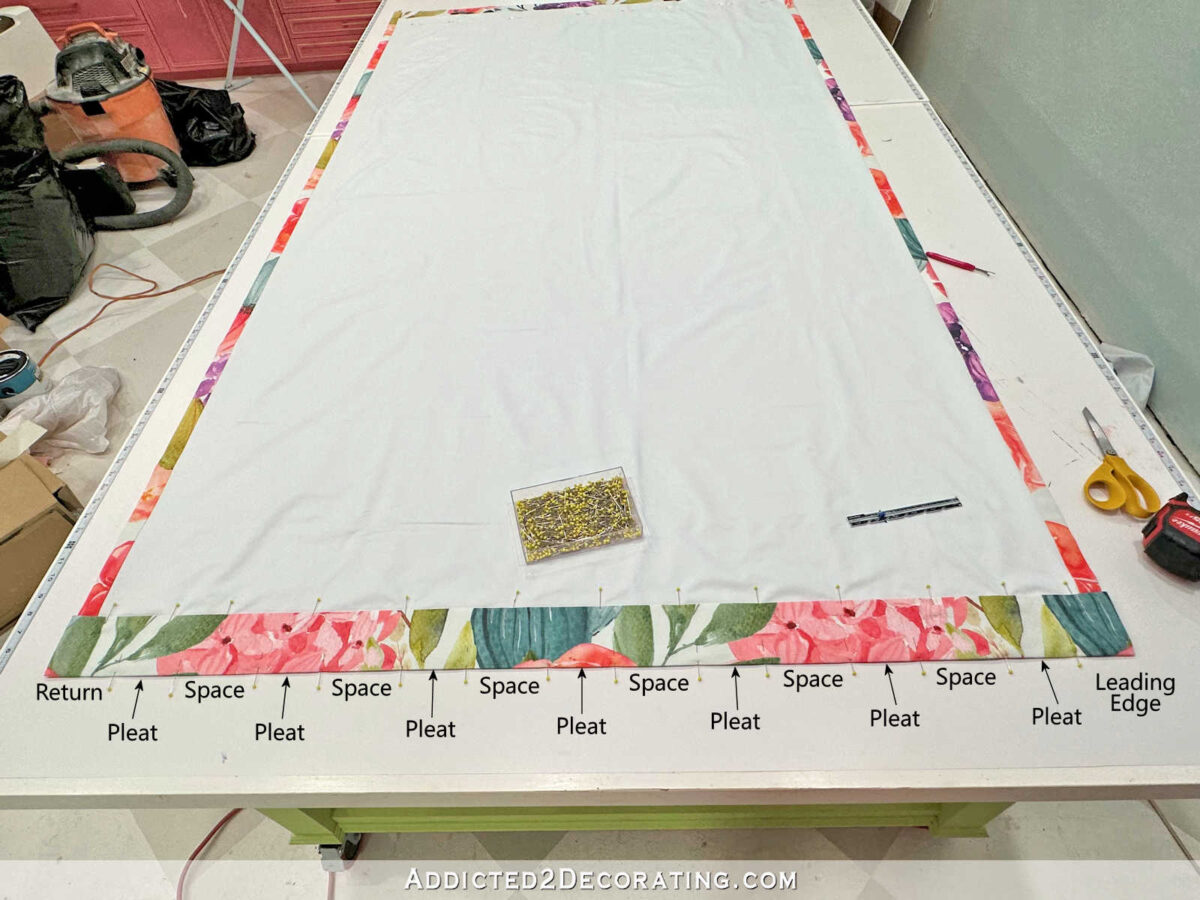
Subsequent I wanted to pin the pleats in order that I might sew them into place. To do that, I folded the material in order that the to pins marking off the pleat met.
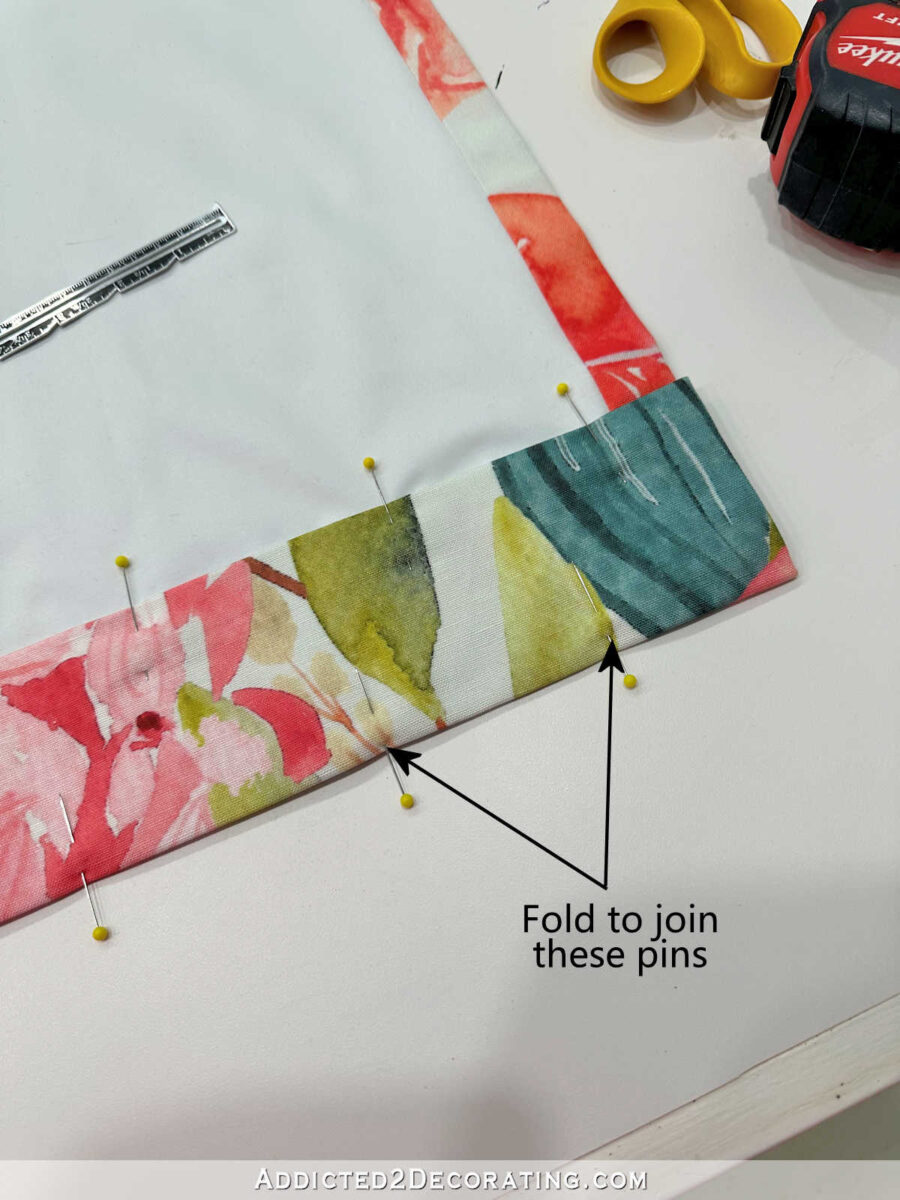
I folded the material in order that the again sides had been collectively as proven…
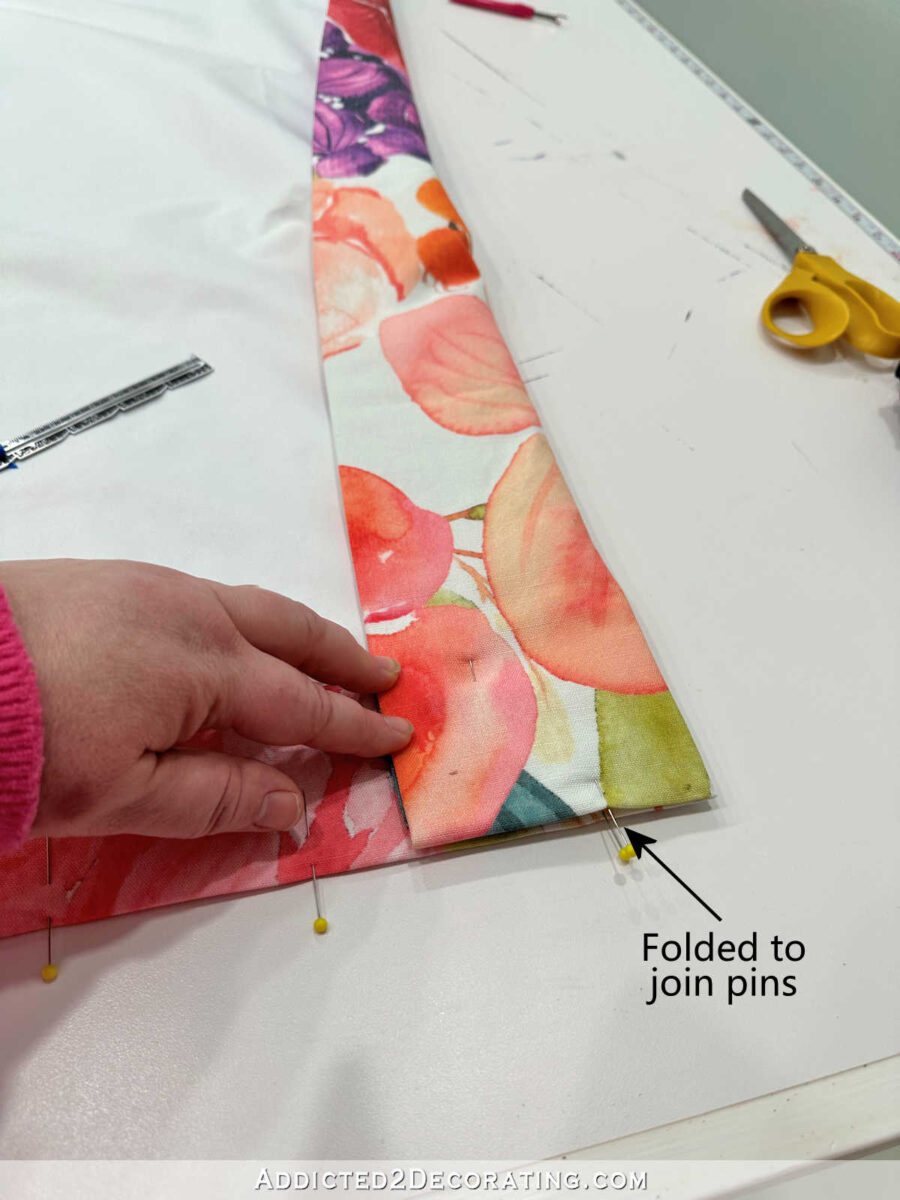
After which I eliminated one of many pins, and pinned all layers along with one pin.

Right here’s what that seemed like pinned in…
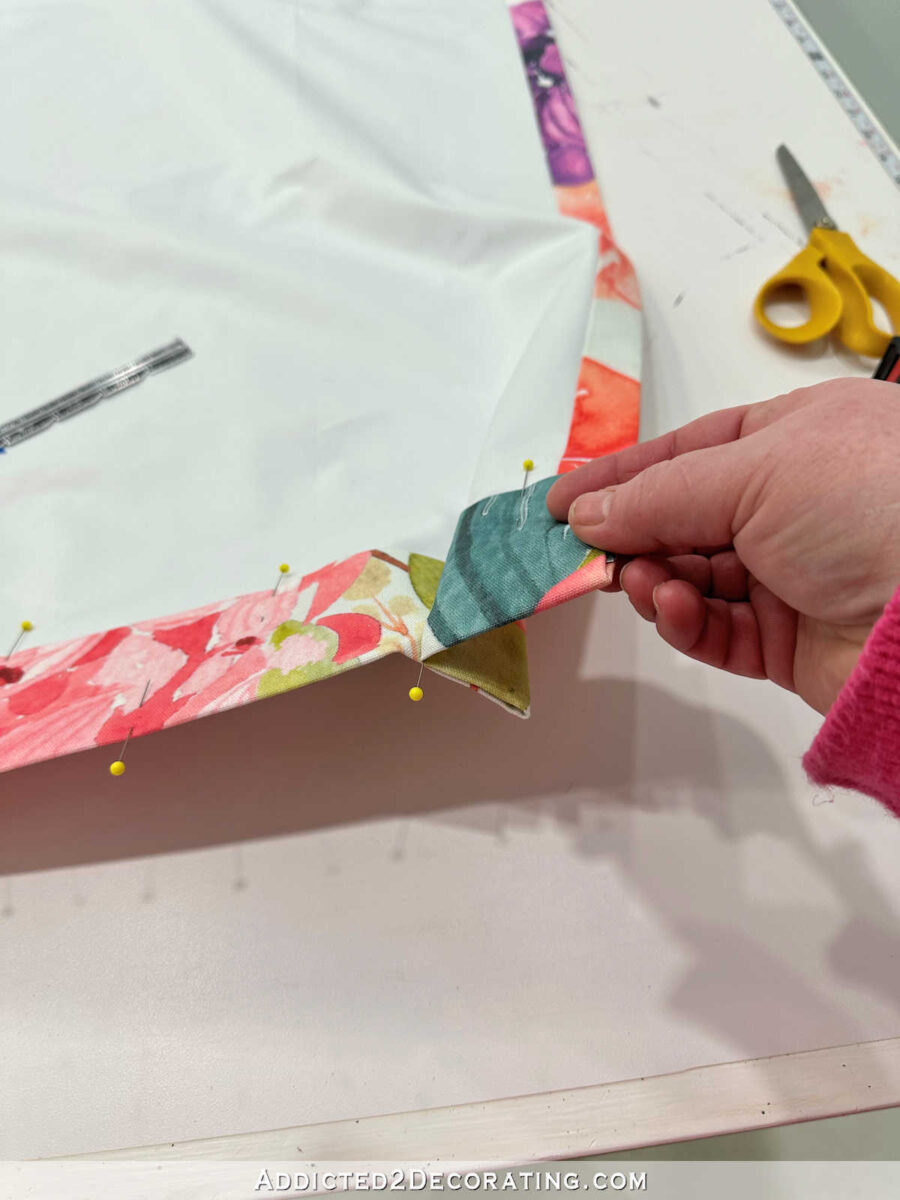
Then I skipped the house subsequent to that pleat…
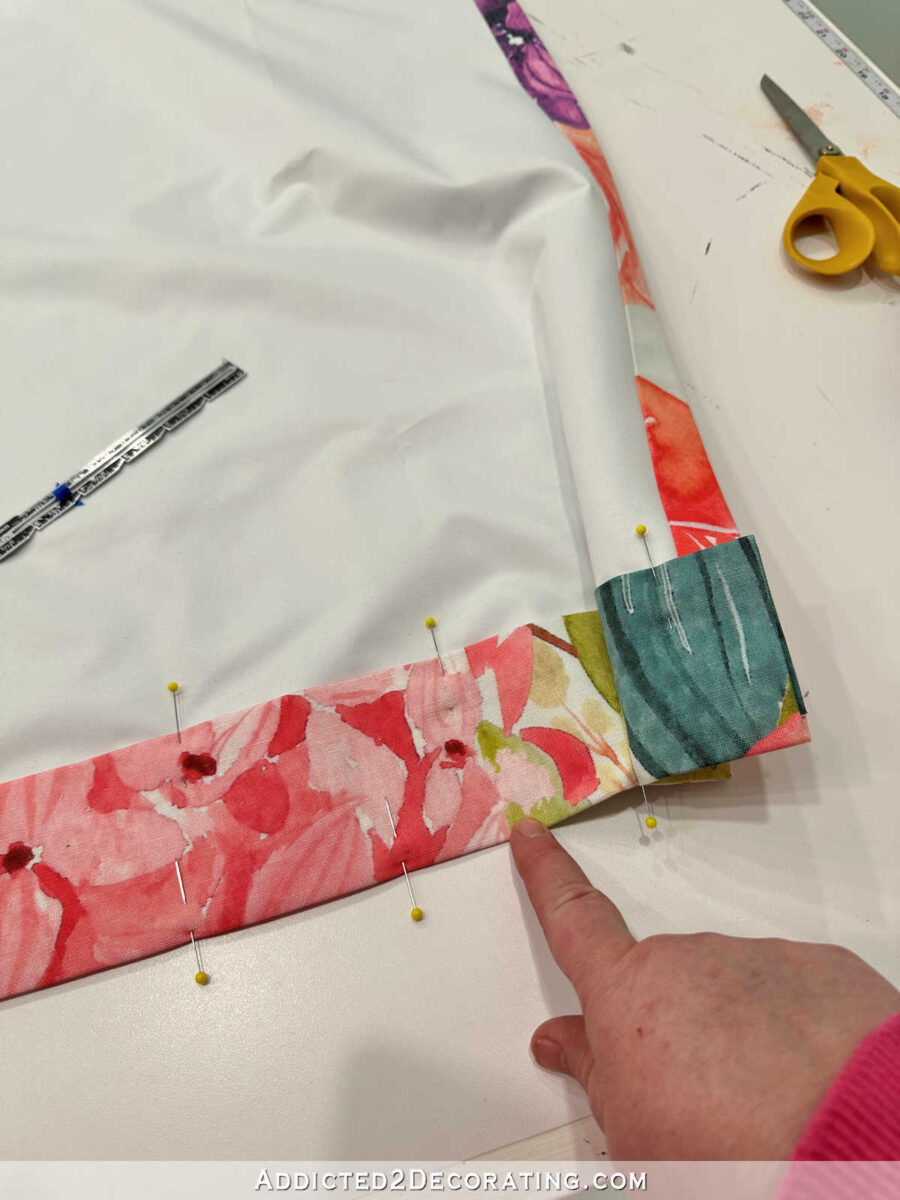
And moved on to the subsequent space marked off as a pleat, and repeated that folding and pinning course of.
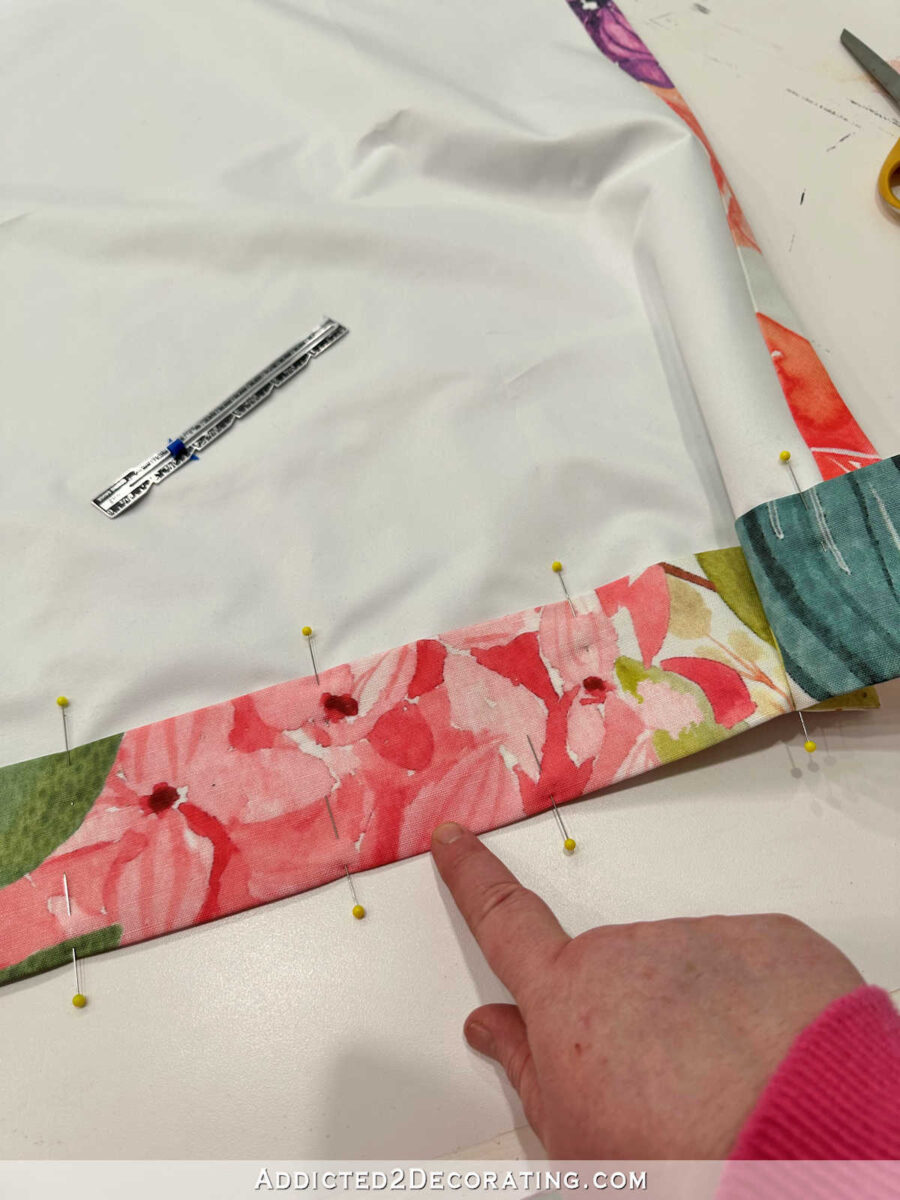
So with two pleats pinned in place, that is what it seemed like…

I repeated that each one the best way throughout till I had all seven pleats pinned.

At this level, these different pins alongside the underside of the material header tape/folded material may be eliminated. They’ve served their function nicely, however at this level they’ll simply be in the best way.
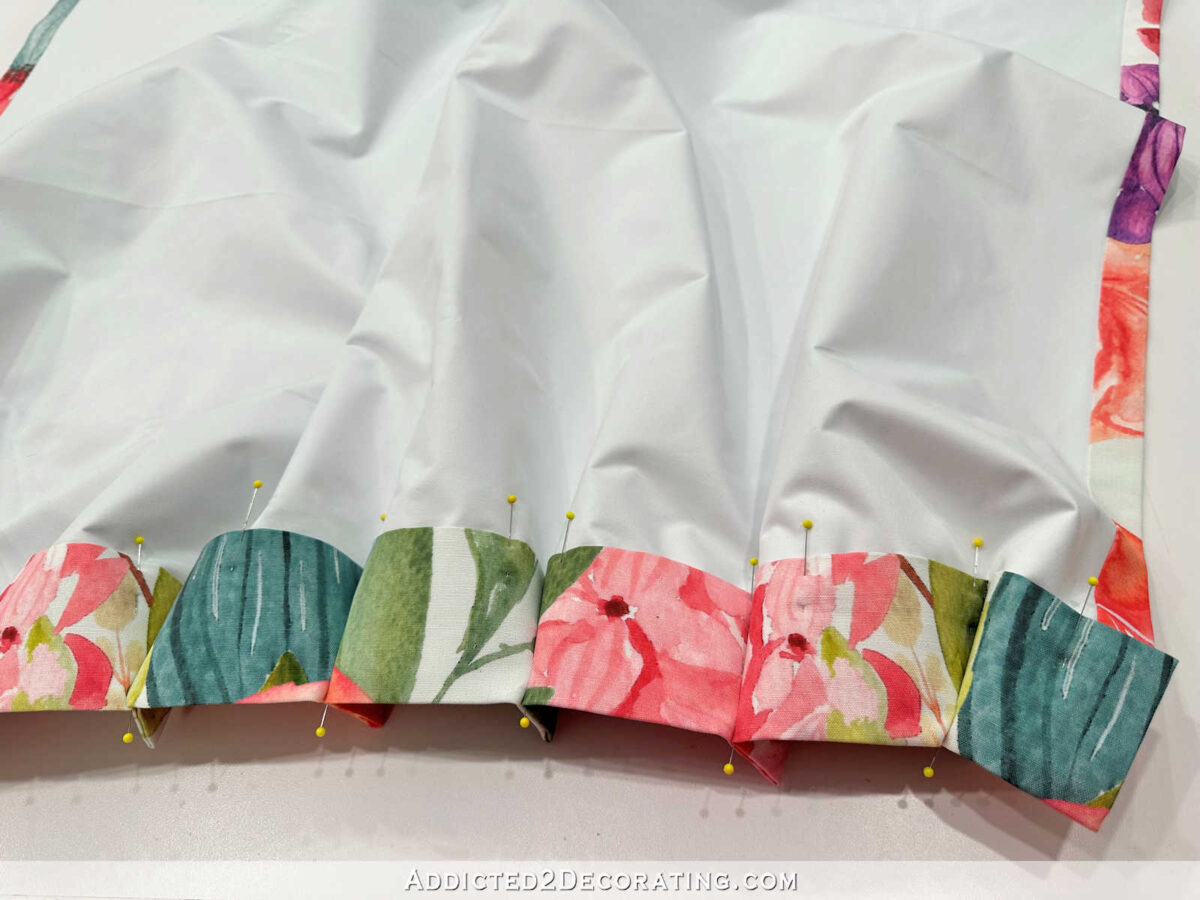
So with the pleats pinned into place, that is what they appear like from the entrance. I used my fingers to crease and press the entrance folds into the header tape earlier than I took the panel to the stitching machine.

Stitching the pleats into place is completed with a primary straight sew.

To find out the place to stitch, simply divide the pleat material width (once more, mine was three inches) by two, and stitch straight down the header tape from high to backside at that distance. So I sewed my sew at 1 1/2 inches from the sting.
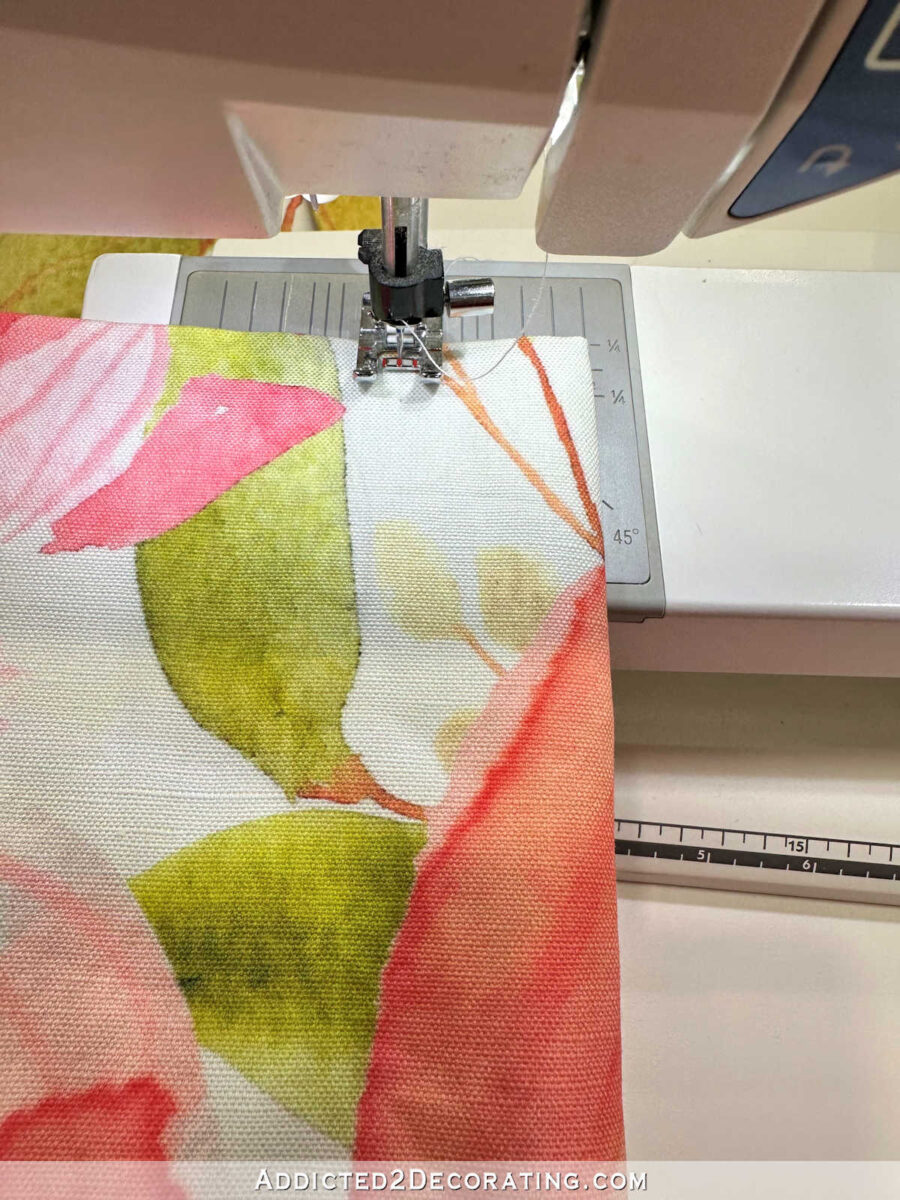
And right here’s what it appears like with the pleat sewn into place.
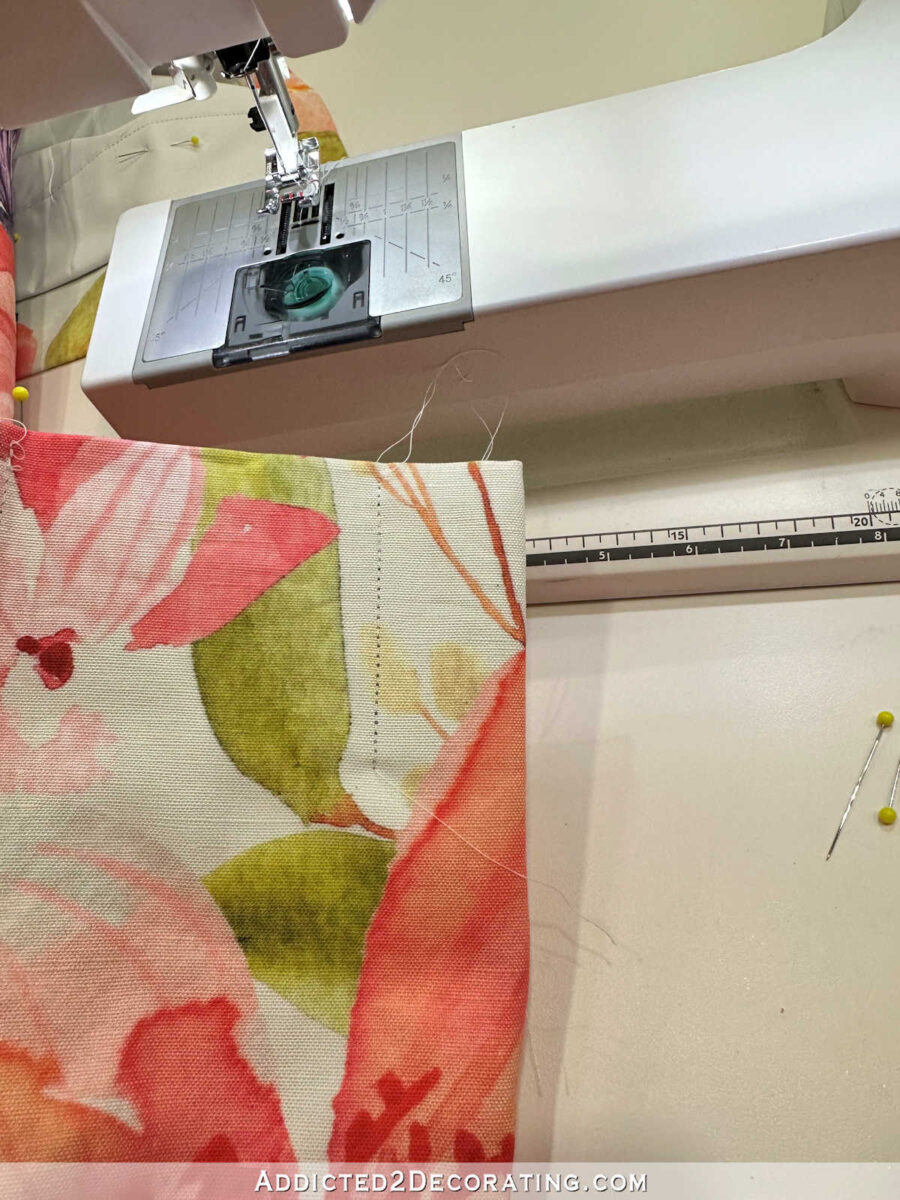
I repeated that on the opposite pleats, and that is what the header seemed like with the entire pleats sewn in.
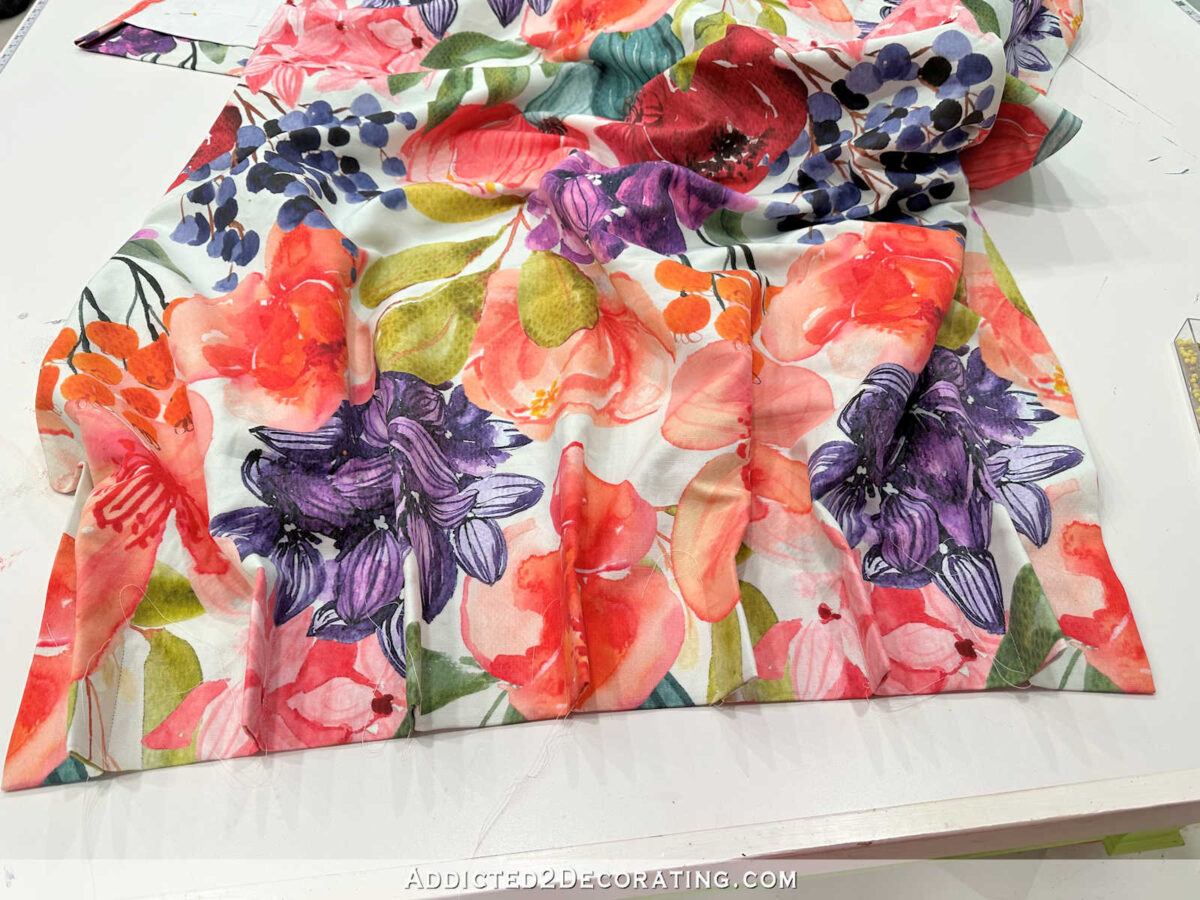
Right here’s a facet view for a greater look.
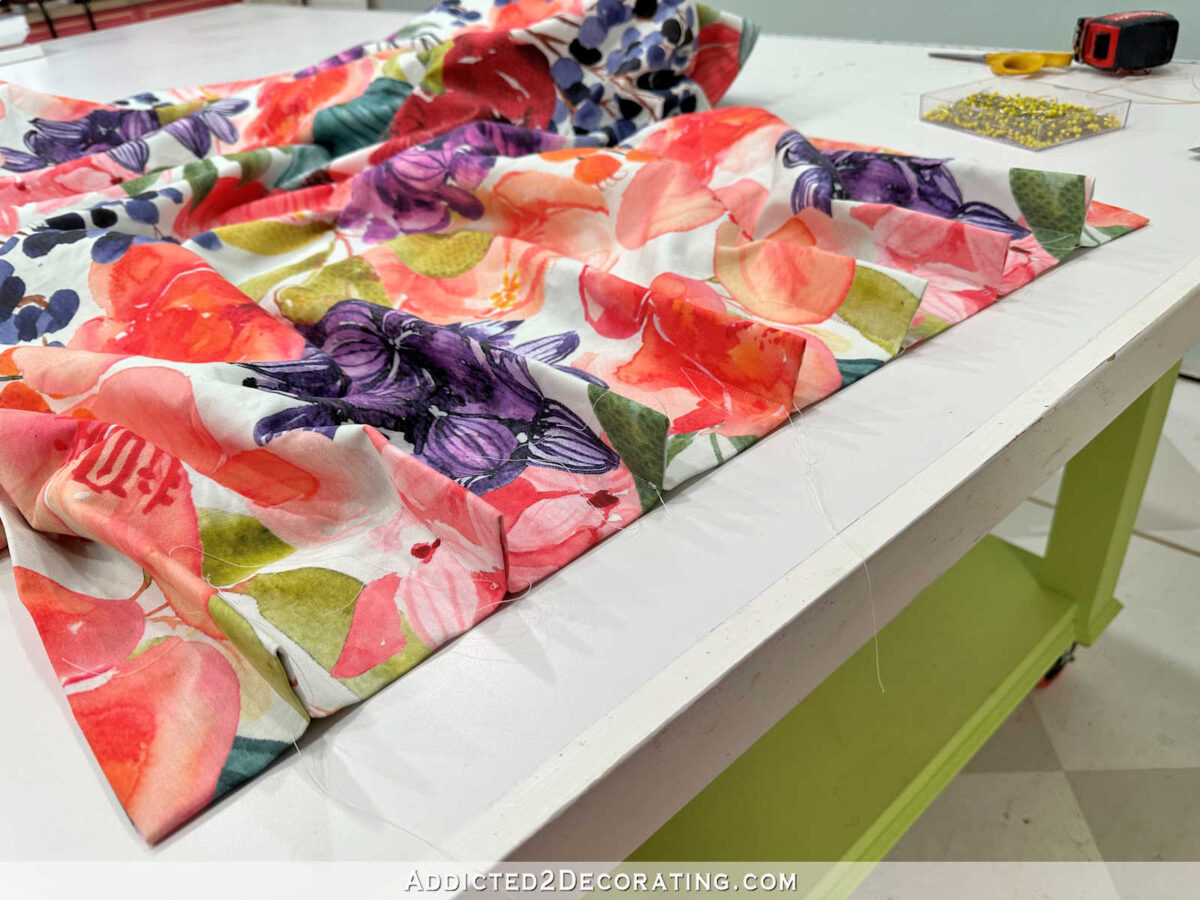
These are the essential pleats, however now I needed to type the “double” a part of the double pleats. To do that, I began my utilizing my finger inside that fold and urgent the seam of the header tape open.
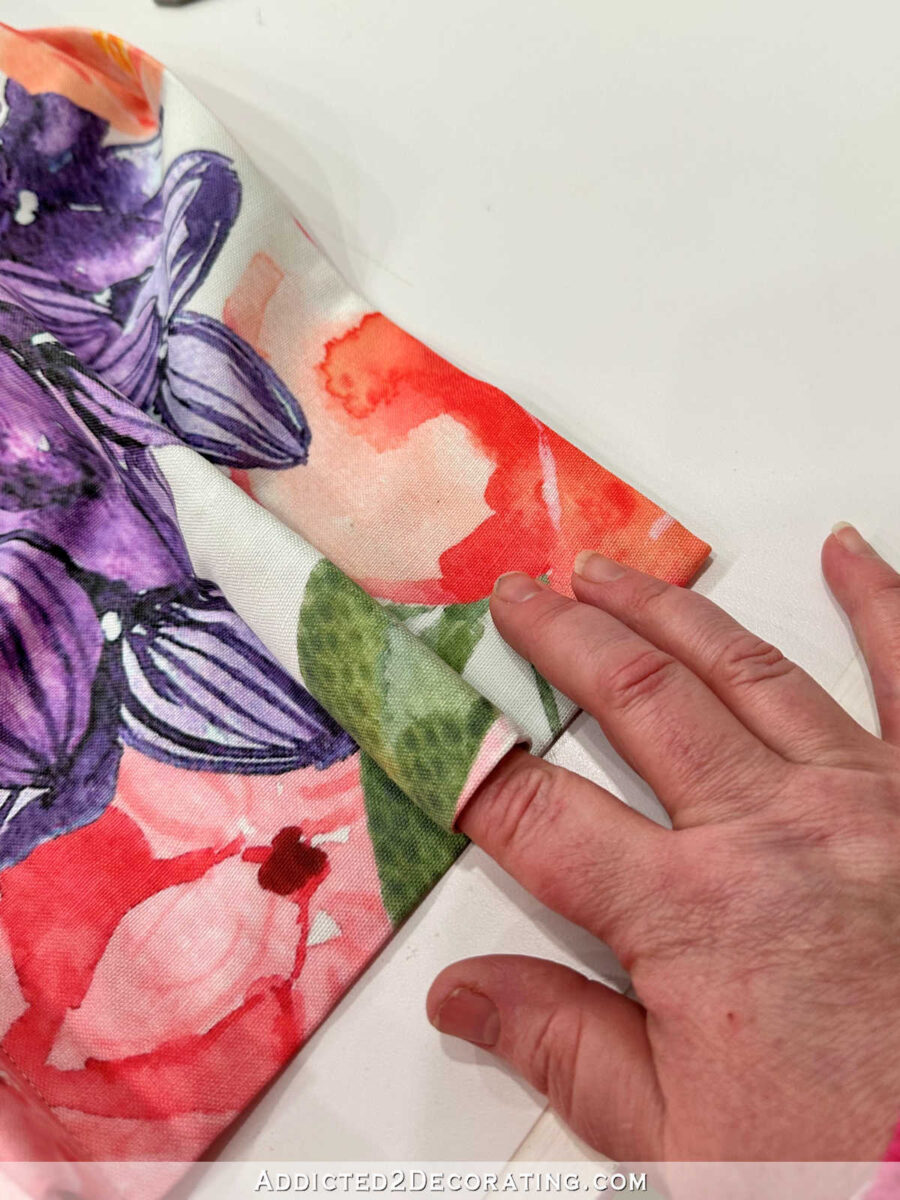
After which I pressed the fold of the pleat down to fulfill the seam…
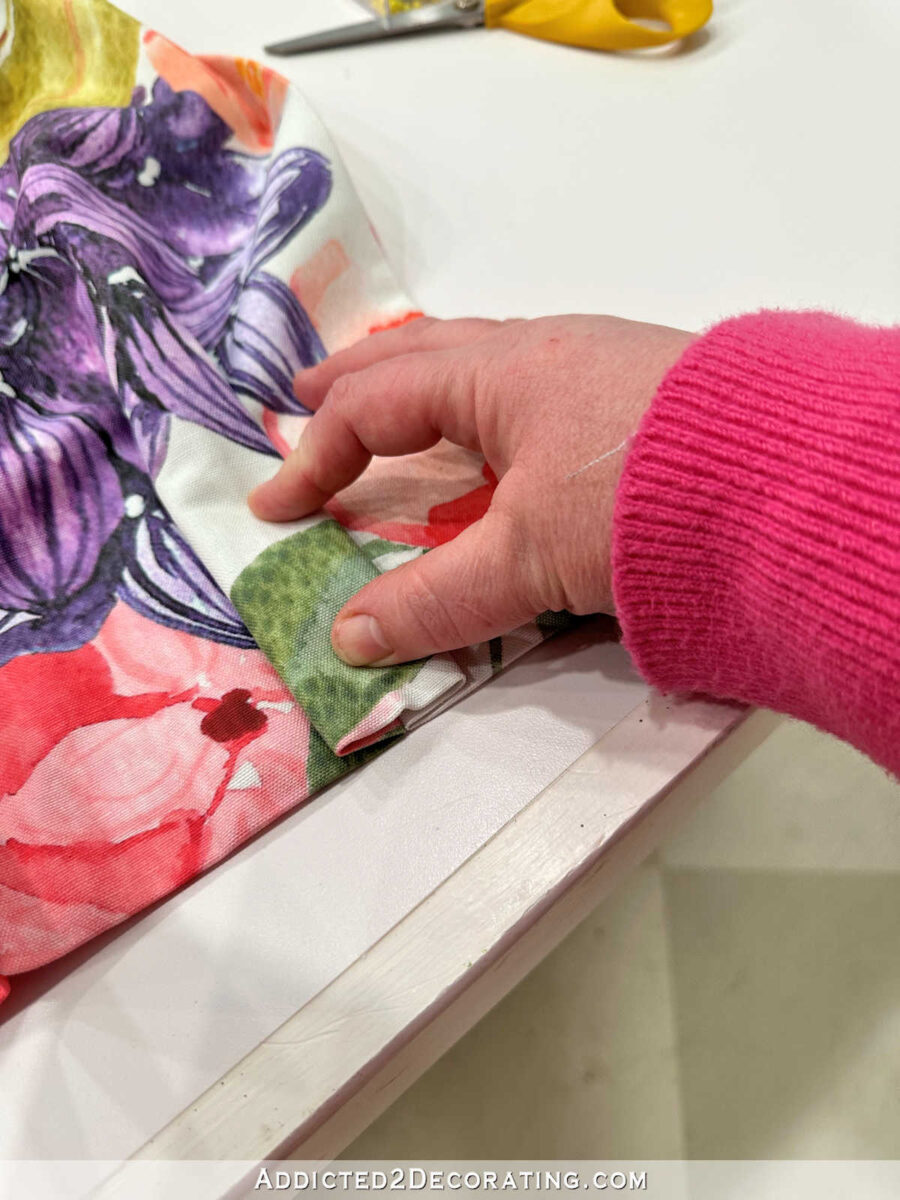
After which I introduced the 2 sides as much as meet. And that kinds the double pleat.
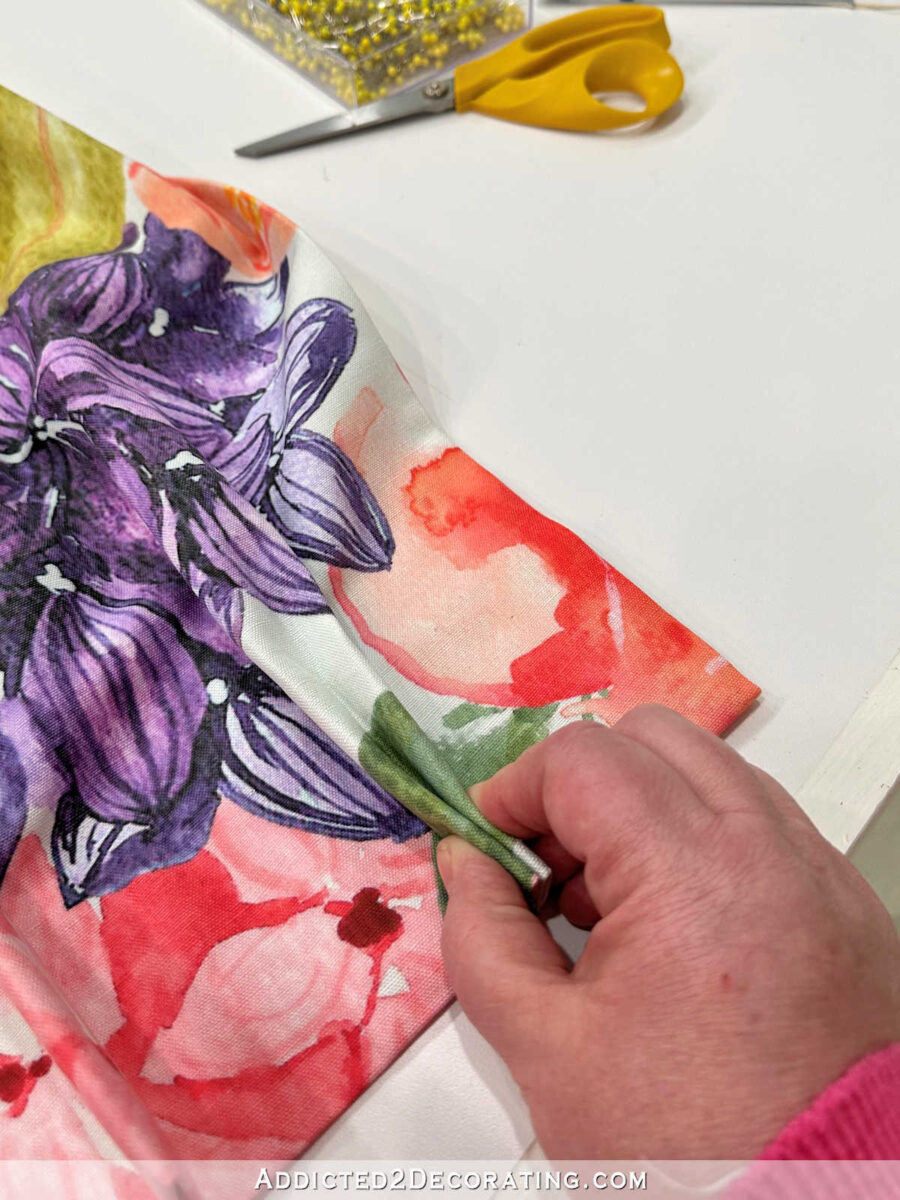
Pleats may be sewn elsewhere to get completely different appears. For instance, if I sew them into place in direction of the underside of the header tape, it leads to a extra conventional French pleat.
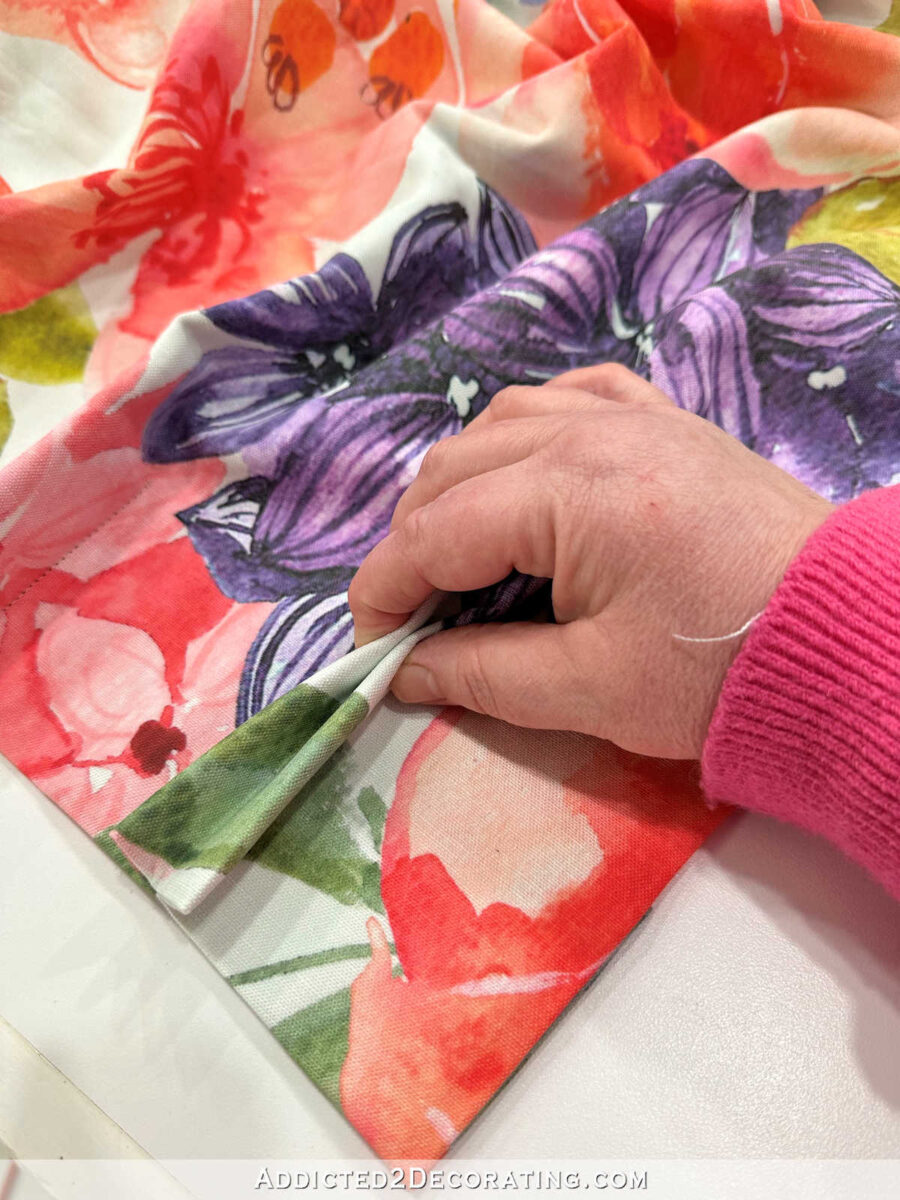
If I sew extra in direction of the highest, it provides a little bit of a extra fashionable look. That is known as a Parisian pleat.
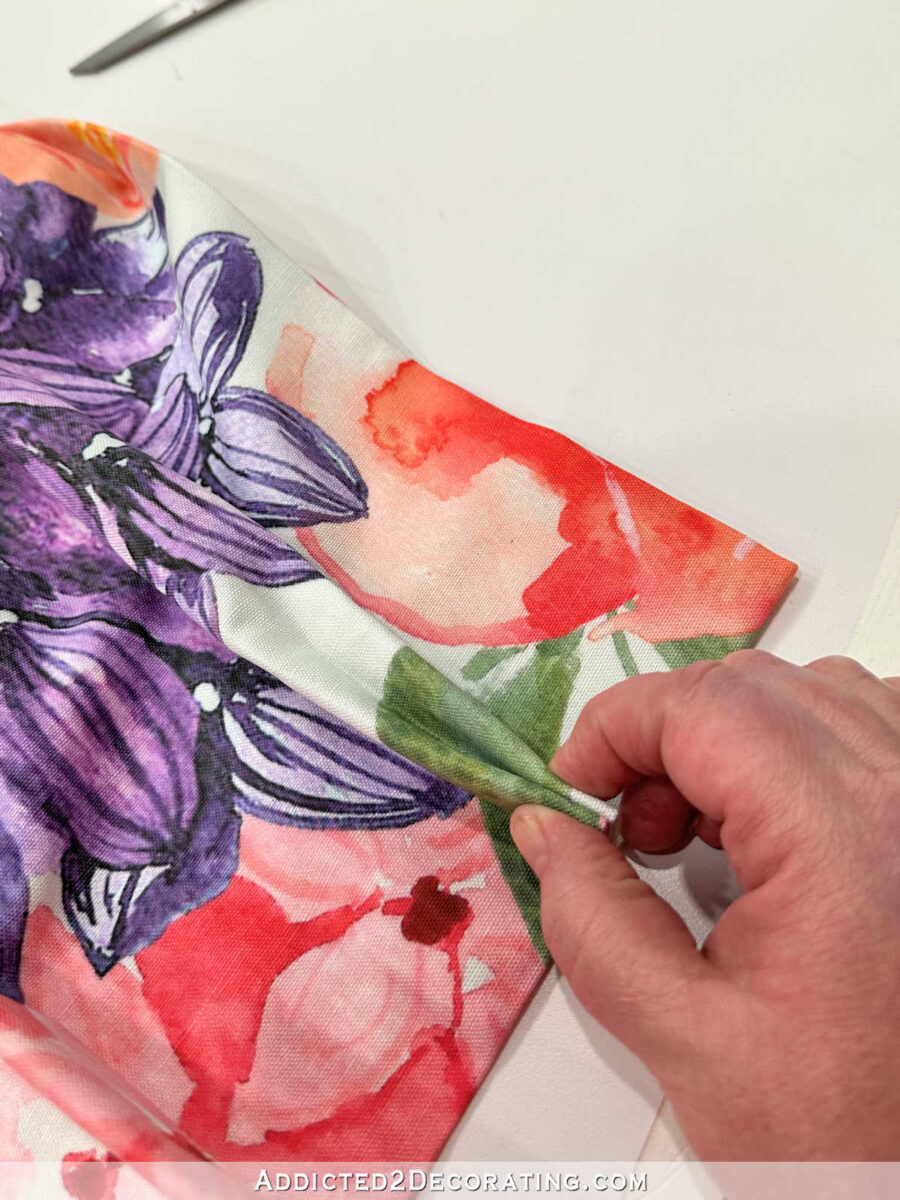
I made a decision to go together with extra of a Parisian pleat by stitching the folds collectively about 3/4 inch from the highest, and 1/4 inch from the entrance folds.

Every stitching machine will probably be a bit completely different, however that is what the sew appears like on my stitching machine.

When you don’t have a sew that appears like that, you need to use a large zigzag sew with a stationary foot (i.e., set it in order that the foot doesn’t stroll the material ahead).
And right here’s what the sew appears like from the facet.

And right here’s what our double Parisian pleat appears like from the entrance.
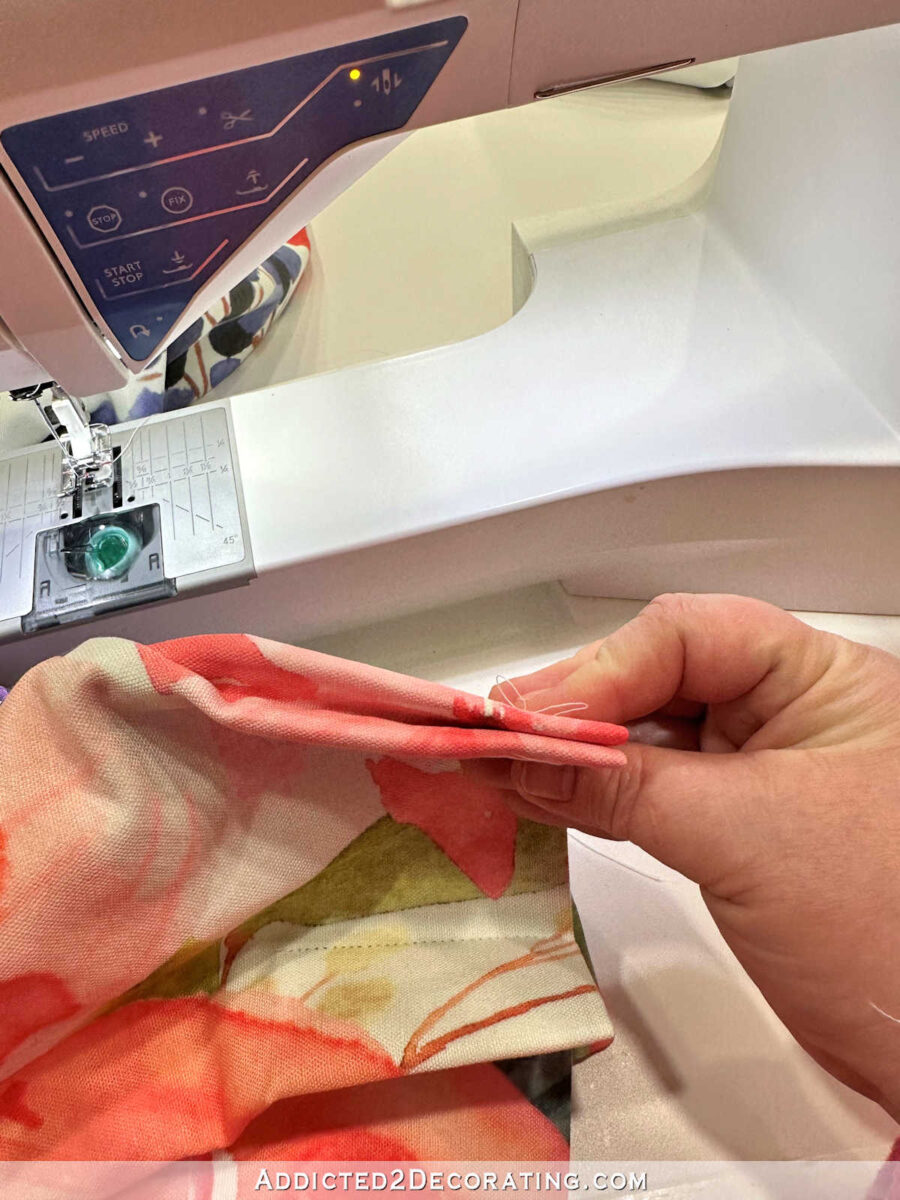
After repeating that course of on the opposite six pleats, my header seemed like this…
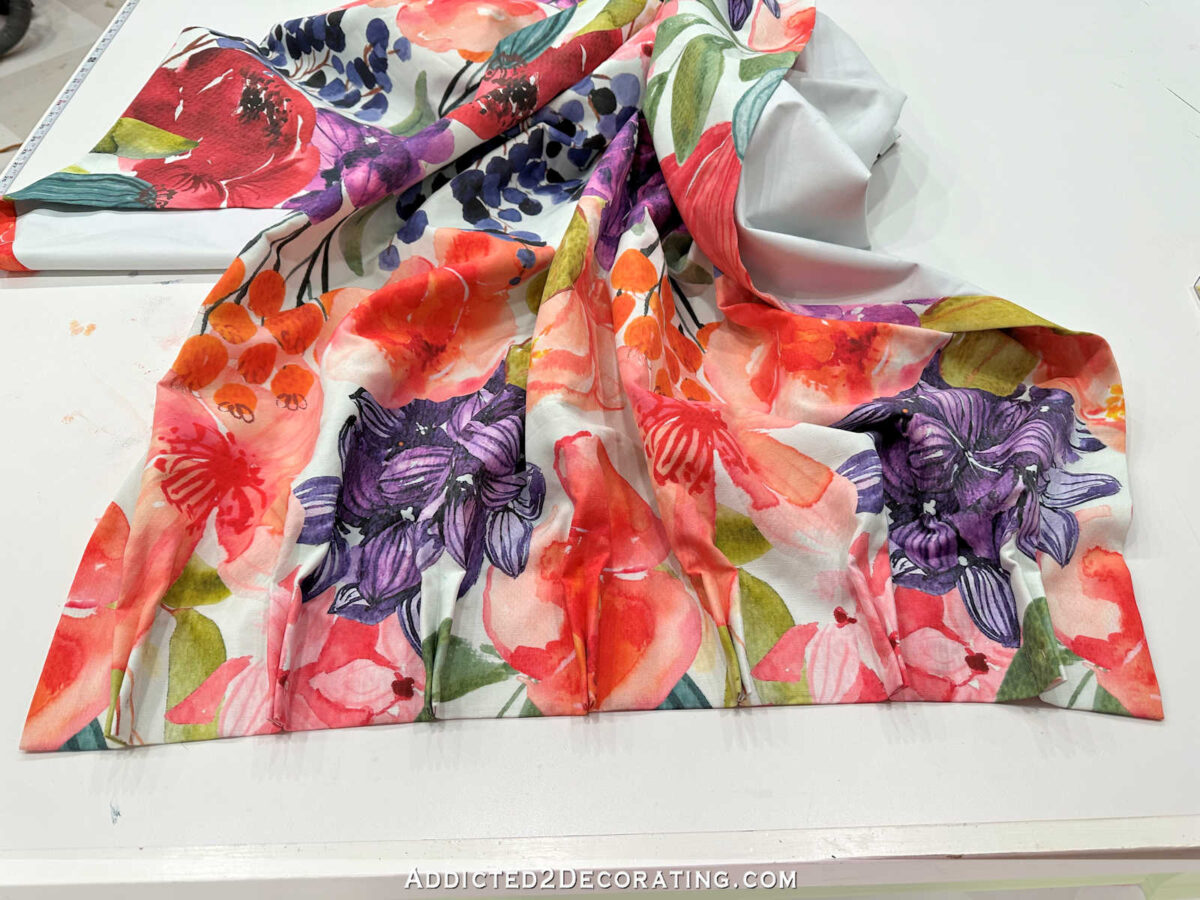
Solely a few ending touches remained. First, I wanted to sew the very ends of the header closed. I personally do that by hand, and never on a machine.
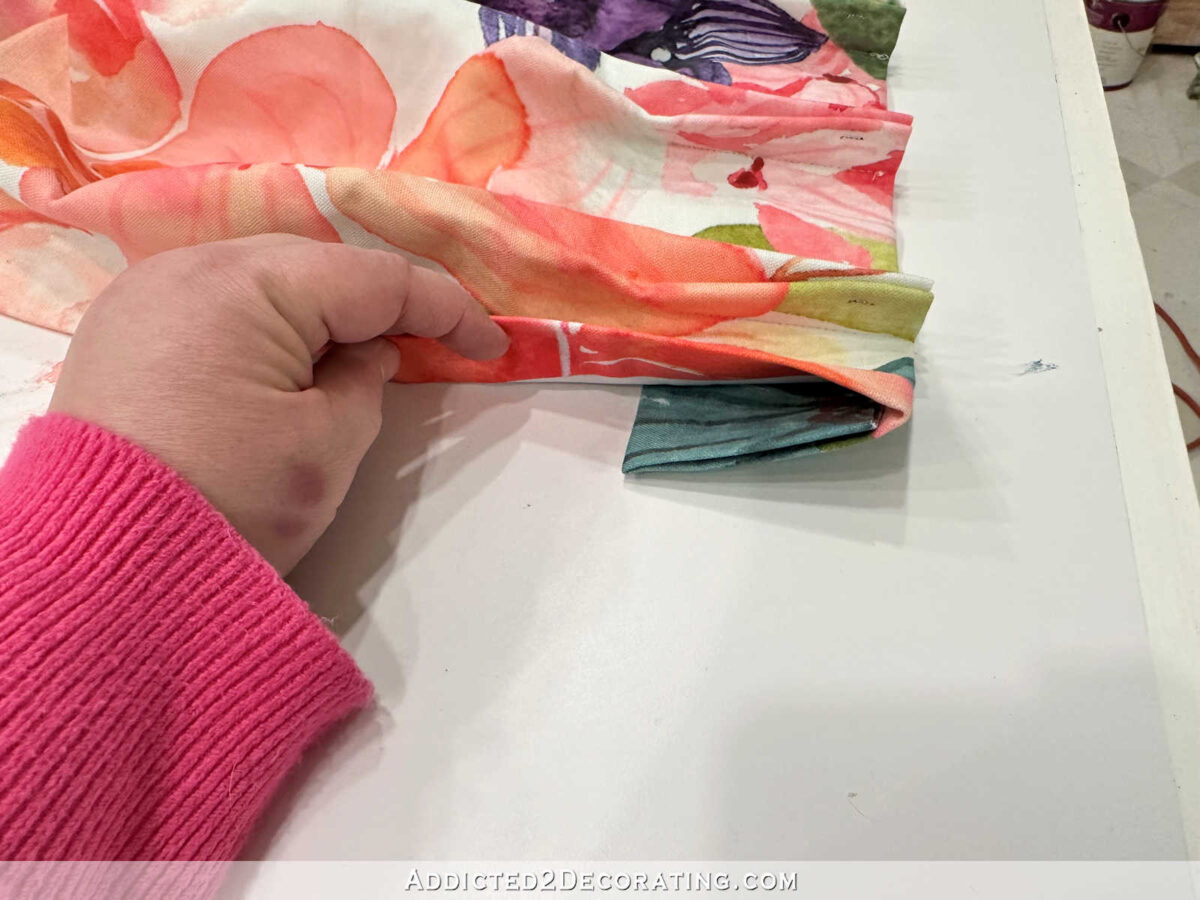
I’m not the easiest at hand stitching, however I nonetheless suppose it appears higher and cleaner than attempting to stitch these layers collectively as near the sting as doable utilizing a machine.
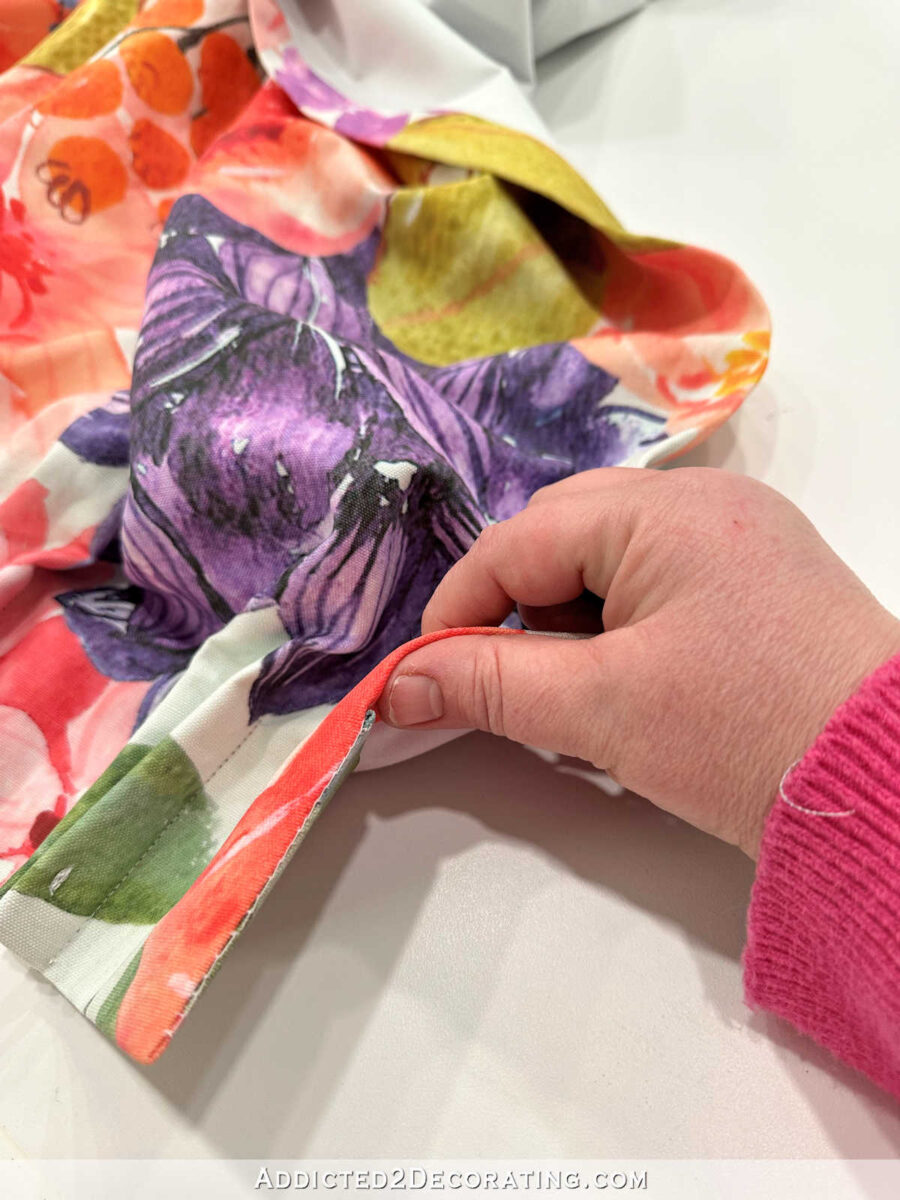
After which I hand sew the very backside corners in order that they keep put. At this level, they had been nonetheless free and never sewn collectively in any respect.

I do that through the use of the least quantity of hand stitching doable simply because I don’t need it to indicate.
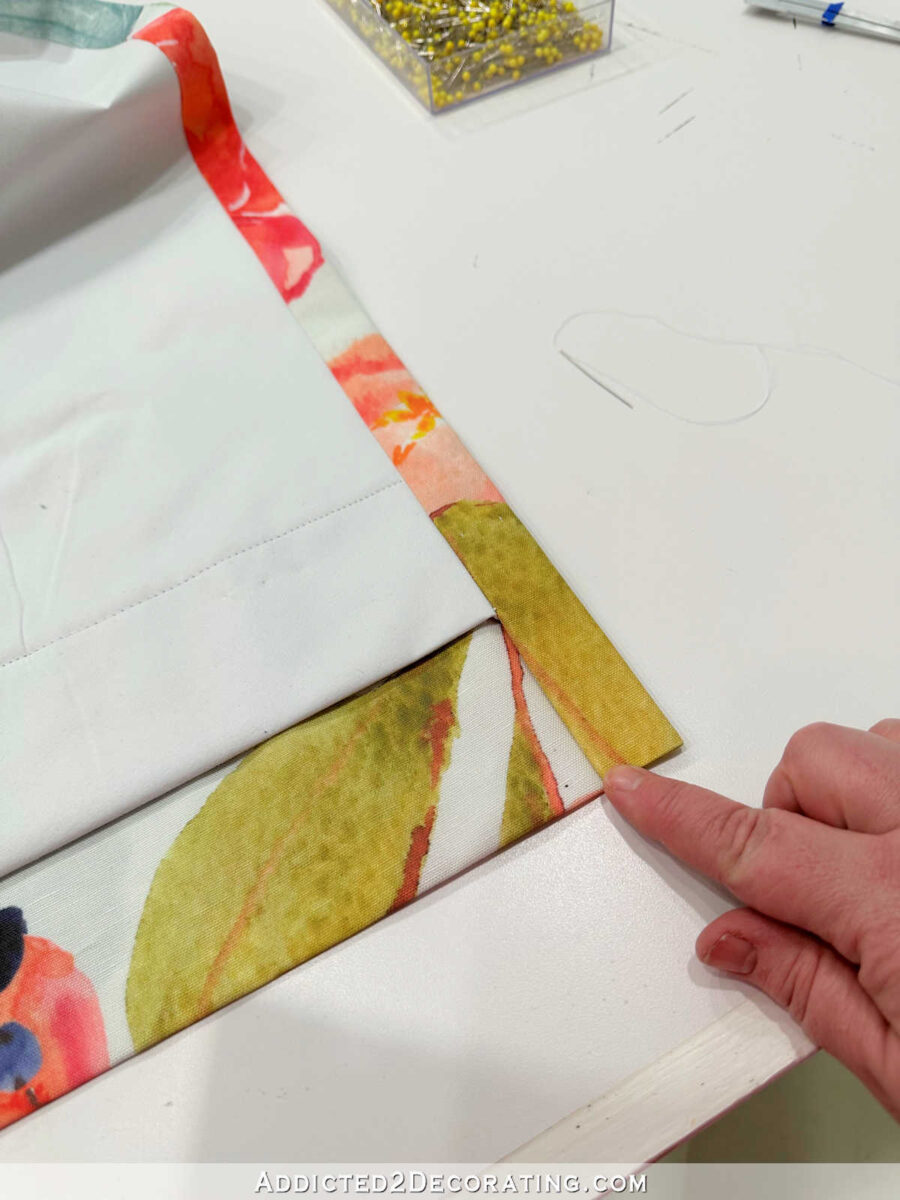
So since I used to be utilizing 100% cotton that stays put, I simply put a easy tack sew proper on that internal fold and thru to the entrance material.
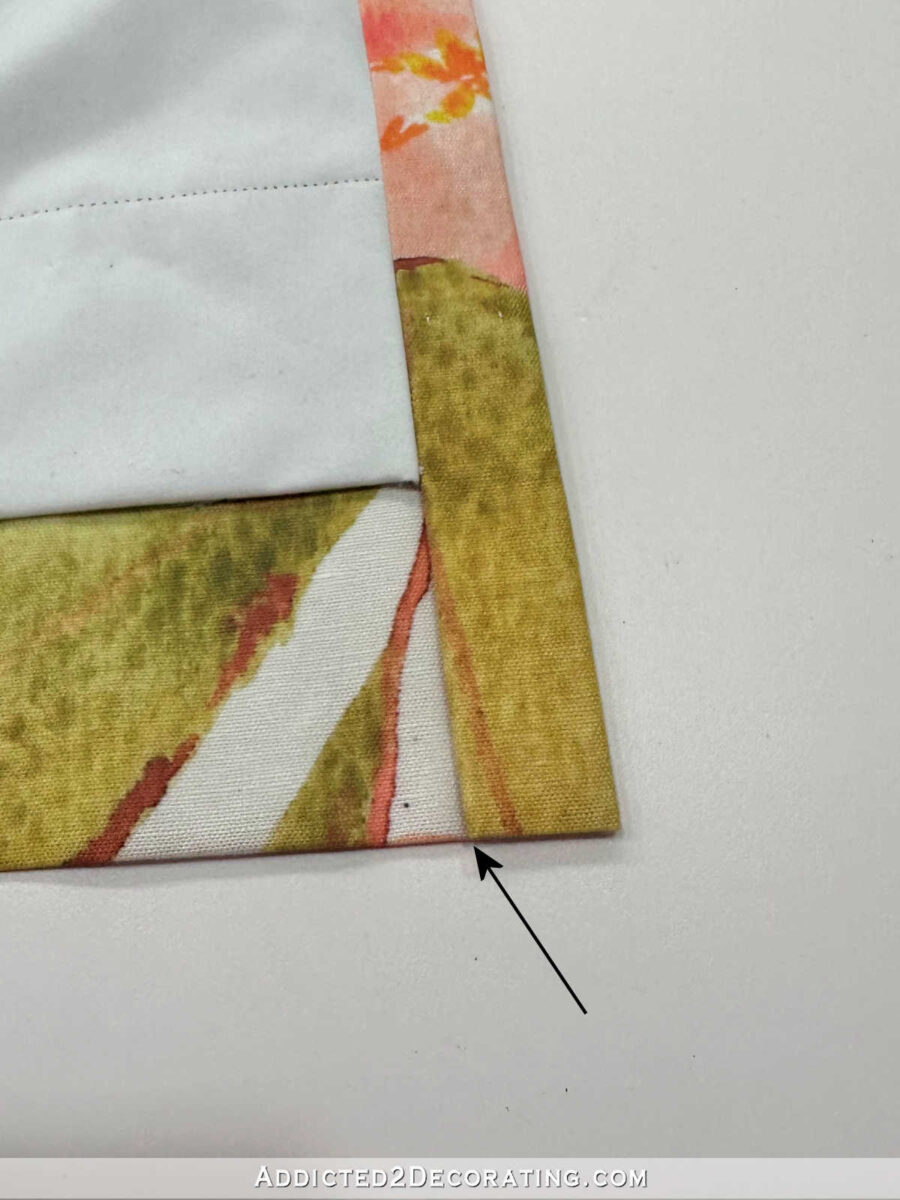
That’s not how I discovered to do it in my material workroom coaching, although. So let me present you what I used to be taught is the correct approach, simply in case you favor it.
First, unfold the nook of the material like this…
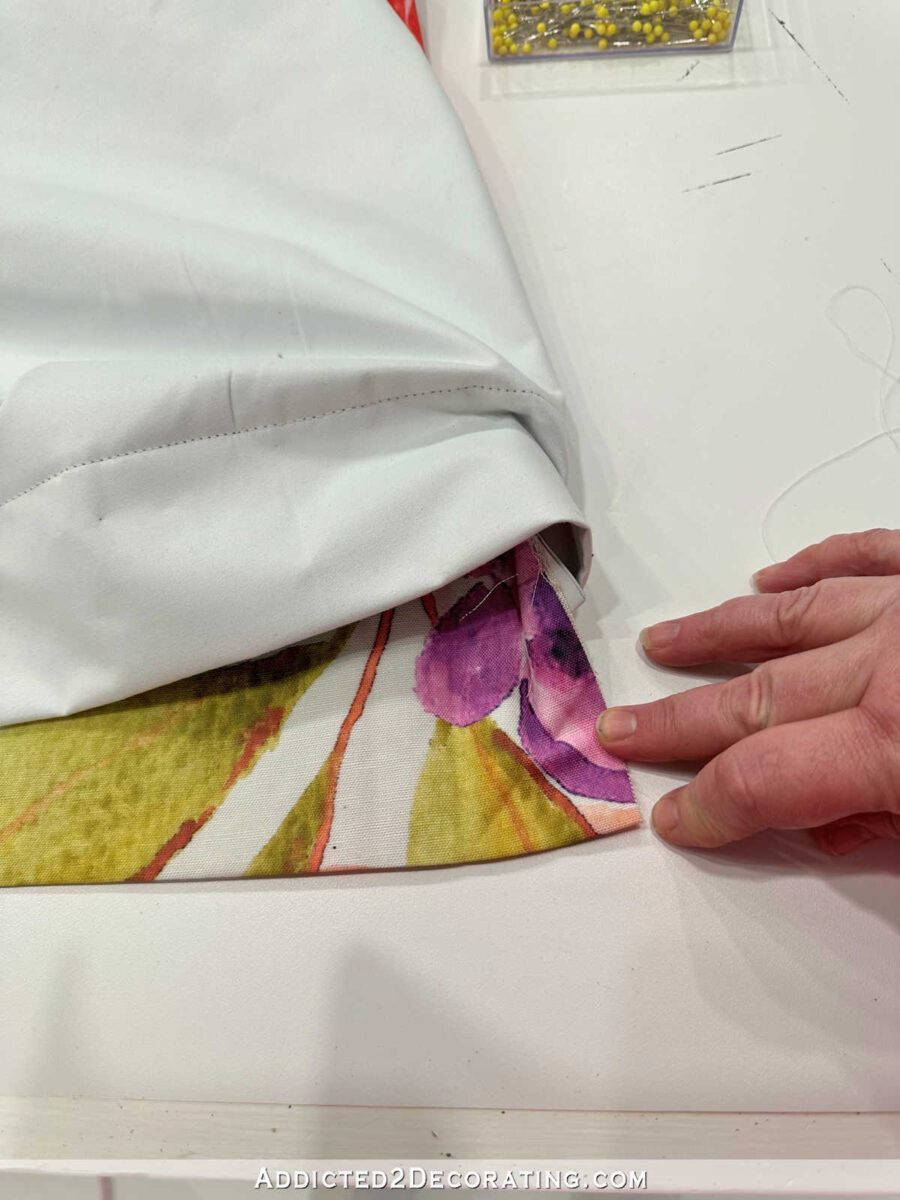
Fold the nook up at a 45-degree angle in order that the sting meets that inside ironed-in crease…
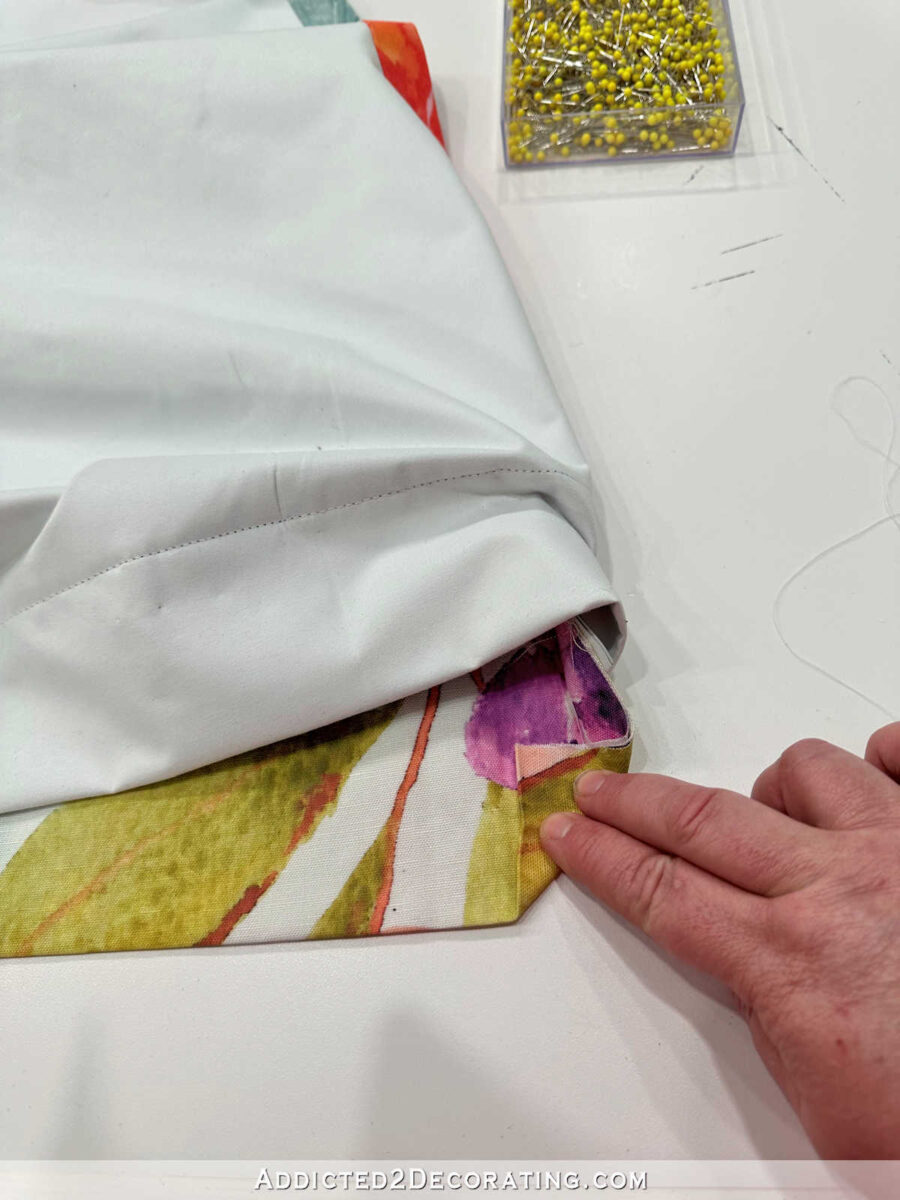
After which refold the sting. That offers you a nook that appears like this…
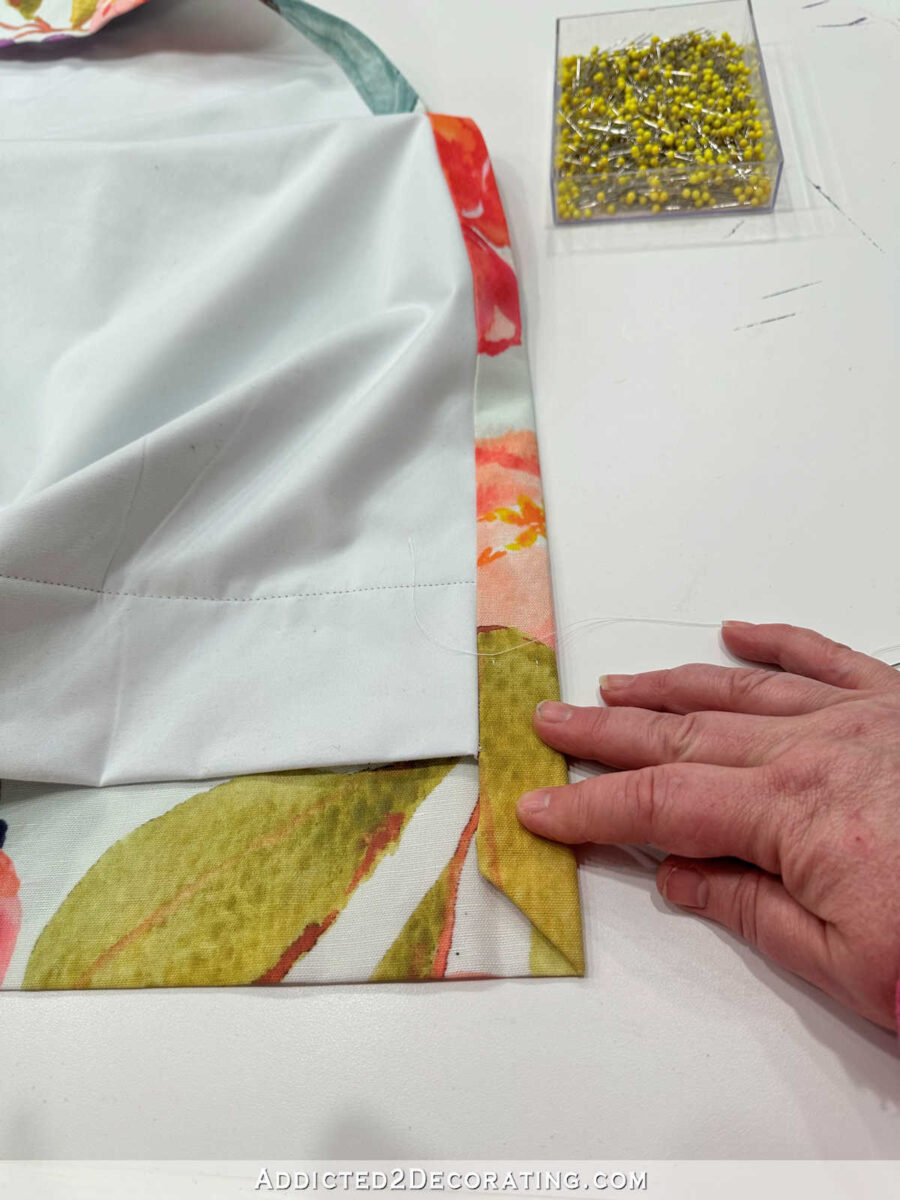
I personally don’t like that. I feel it’s pointless work, creates the necessity for extra hand stitching, creates extra bulk. Plus, I simply don’t like the best way it appears. However that’s a private choice. Chances are you’ll choose that approach, which in fact, is completely advantageous. However I personally simply preserve mine folded straight, add a tiny little tack sew to maintain the flap of material closed, and go away it at that.
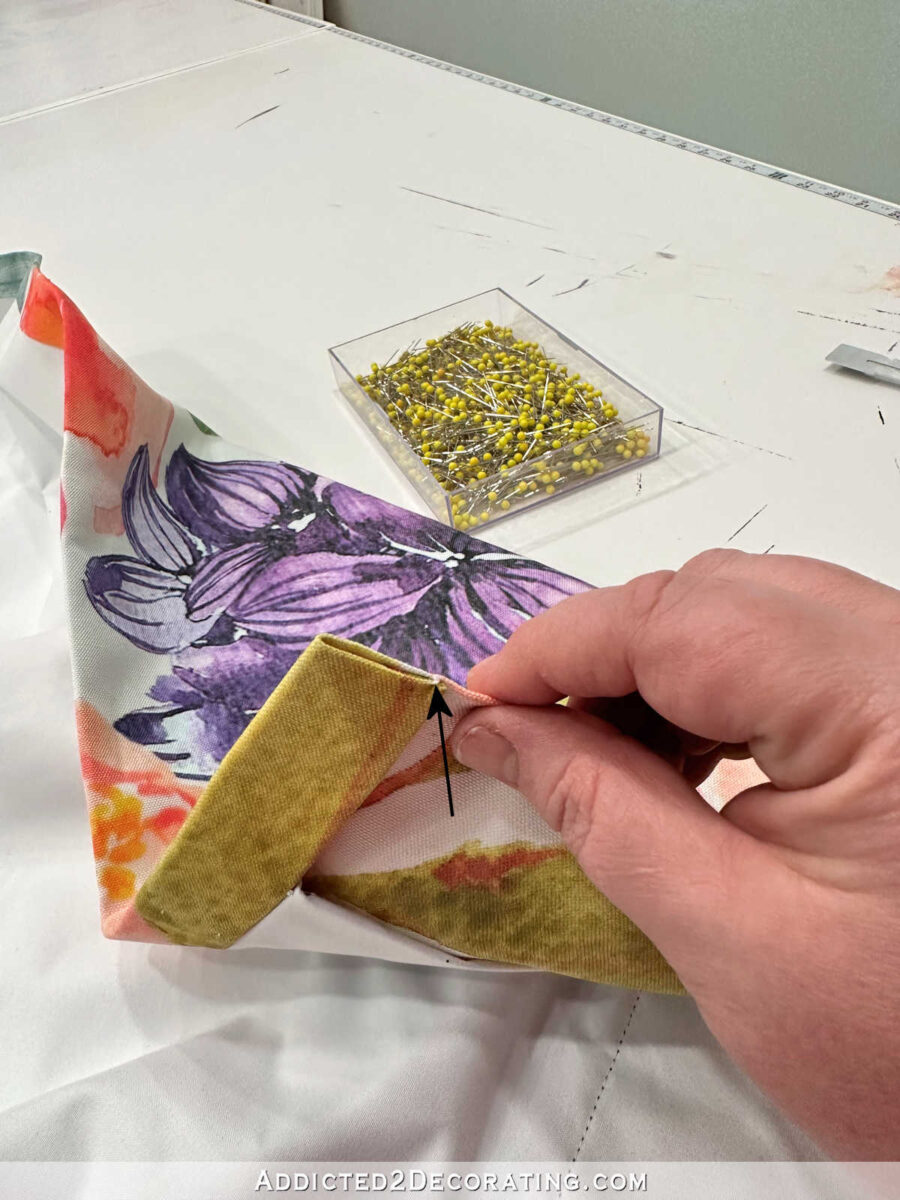
The panel is formally completed! To hold the panel, I had so as to add the material pins to the backs of the pleats. Material pins appears like this…
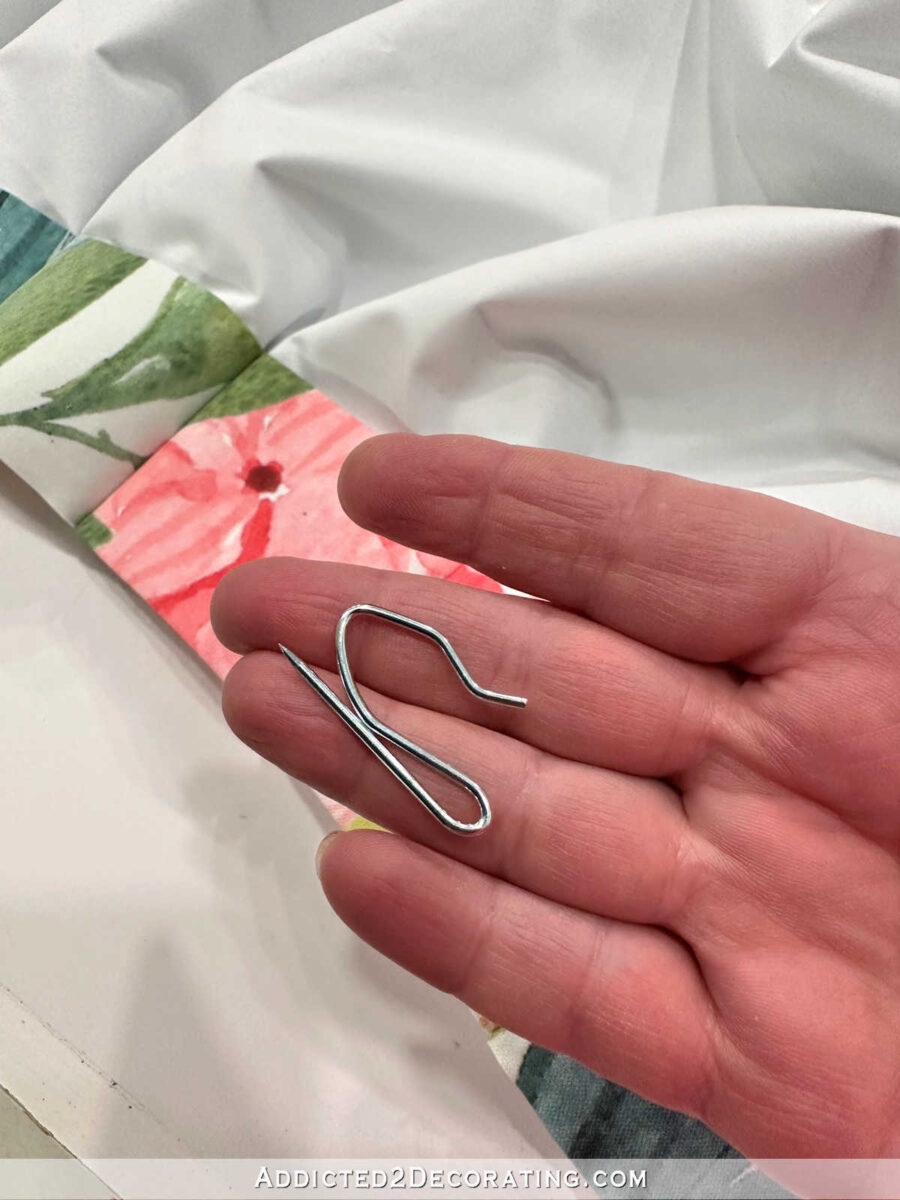
They’re inserted proper behind every pleat with the hook dealing with down and the sharp level going up. They only slide proper below the stitches holding these pleats collectively. You’ll get some resistance when placing them in as a result of these stitches ought to be tight. However for those who’re getting a number of resistance when attempting to place them in, you’re most likely needlessly forcing the pins into layers of material. Simply take away the pin and take a look at once more.
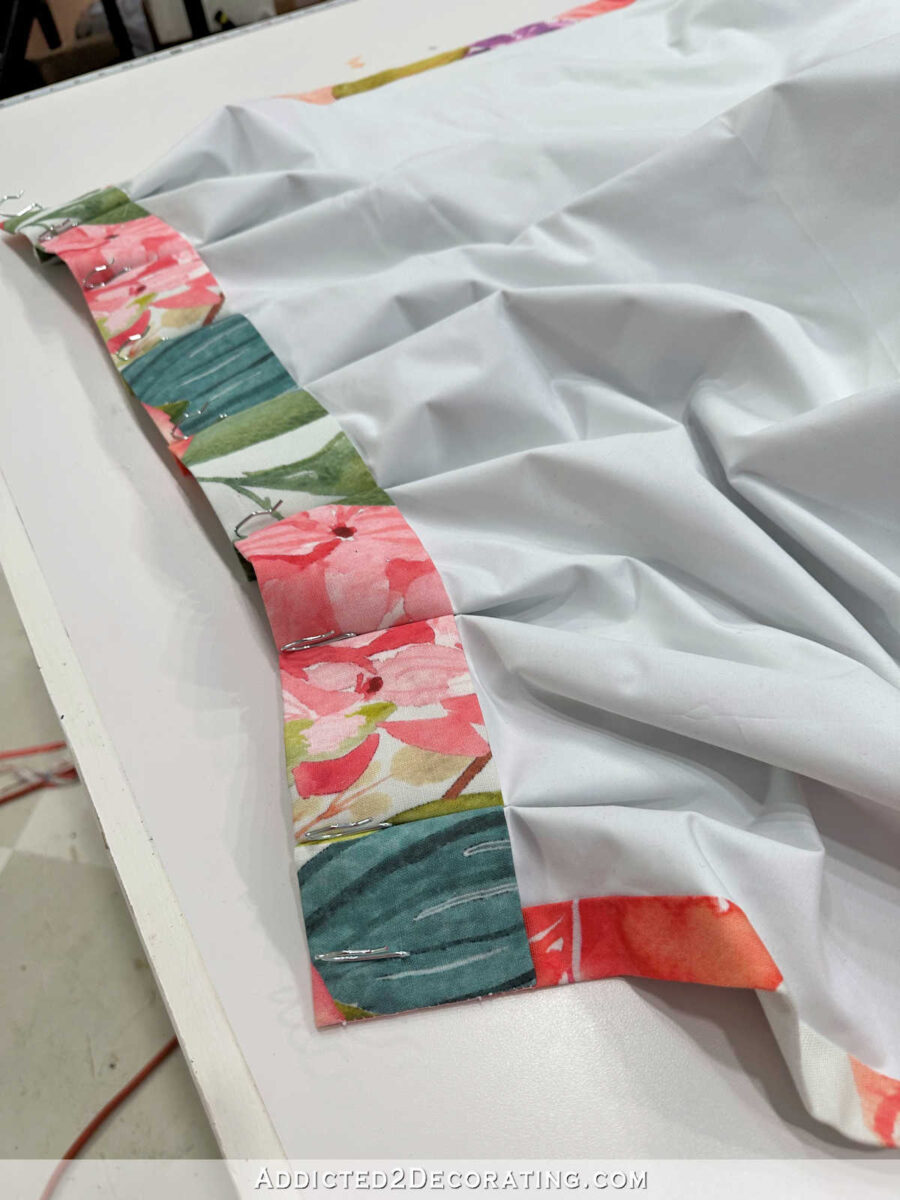
And I additionally added a pin on the sting of the skin return, and about an inch from the vanguard…
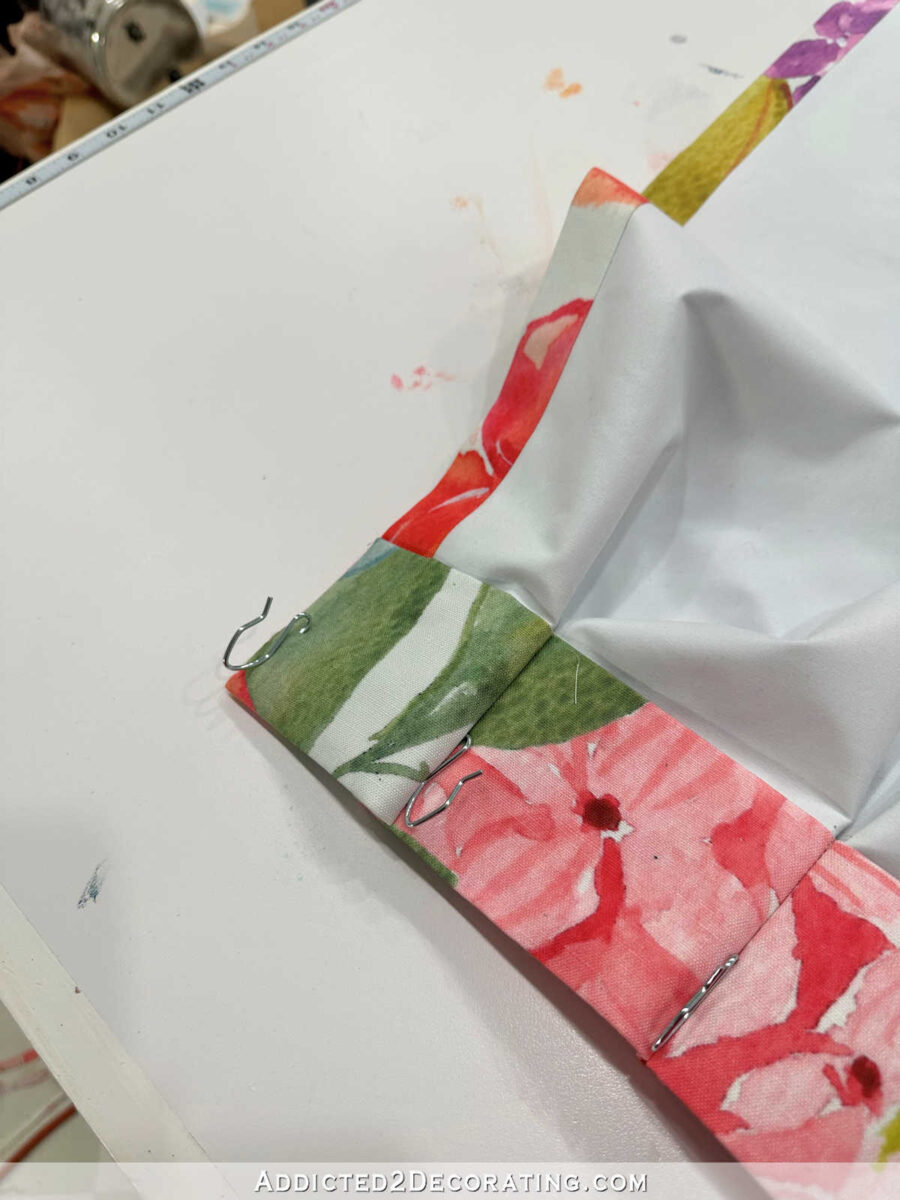
Then I used to be prepared to hold the panel!
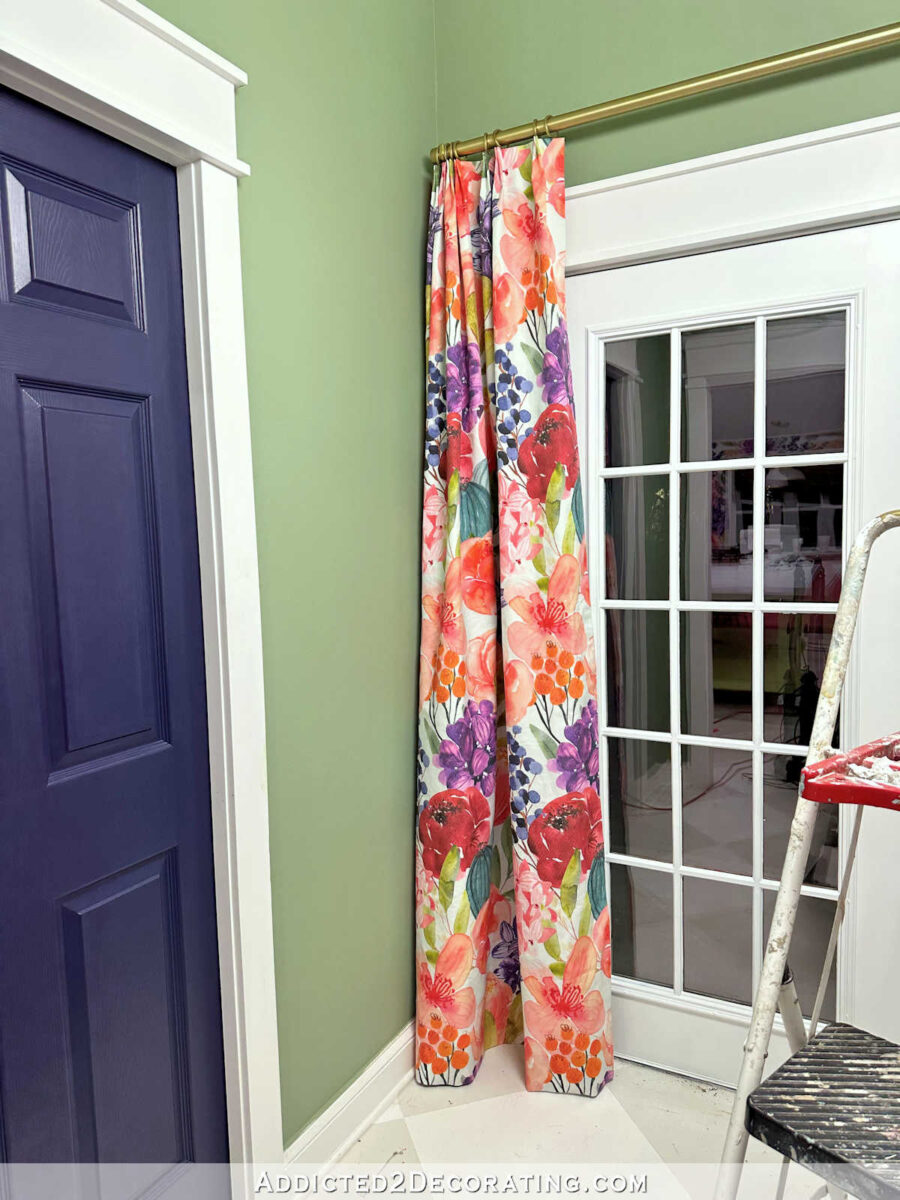
On that return on the outer fringe of the panel, I wanted to place a small eye hook into the wall proper about the place I added the black dot under with the intention to connect that final pin to the wall, however I used to be all out of eye hooks. As soon as I get that carried out, I’ll add the image right here.
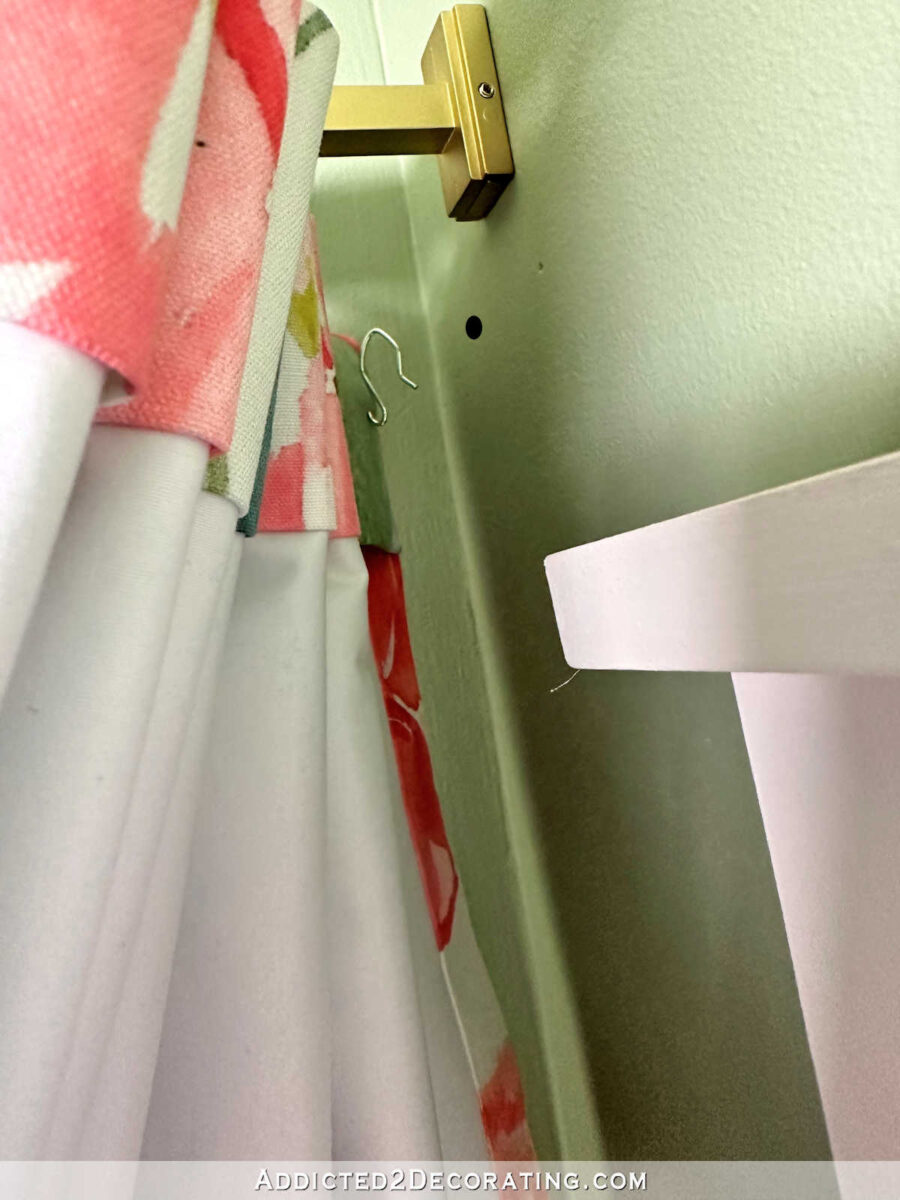
Then I wanted to crease the areas between the pleats in order that they might keep wright here I needed them. So long as there’s no crease within the areas, that header tape will struggle you whenever you attempt to correctly house your curtain rings.
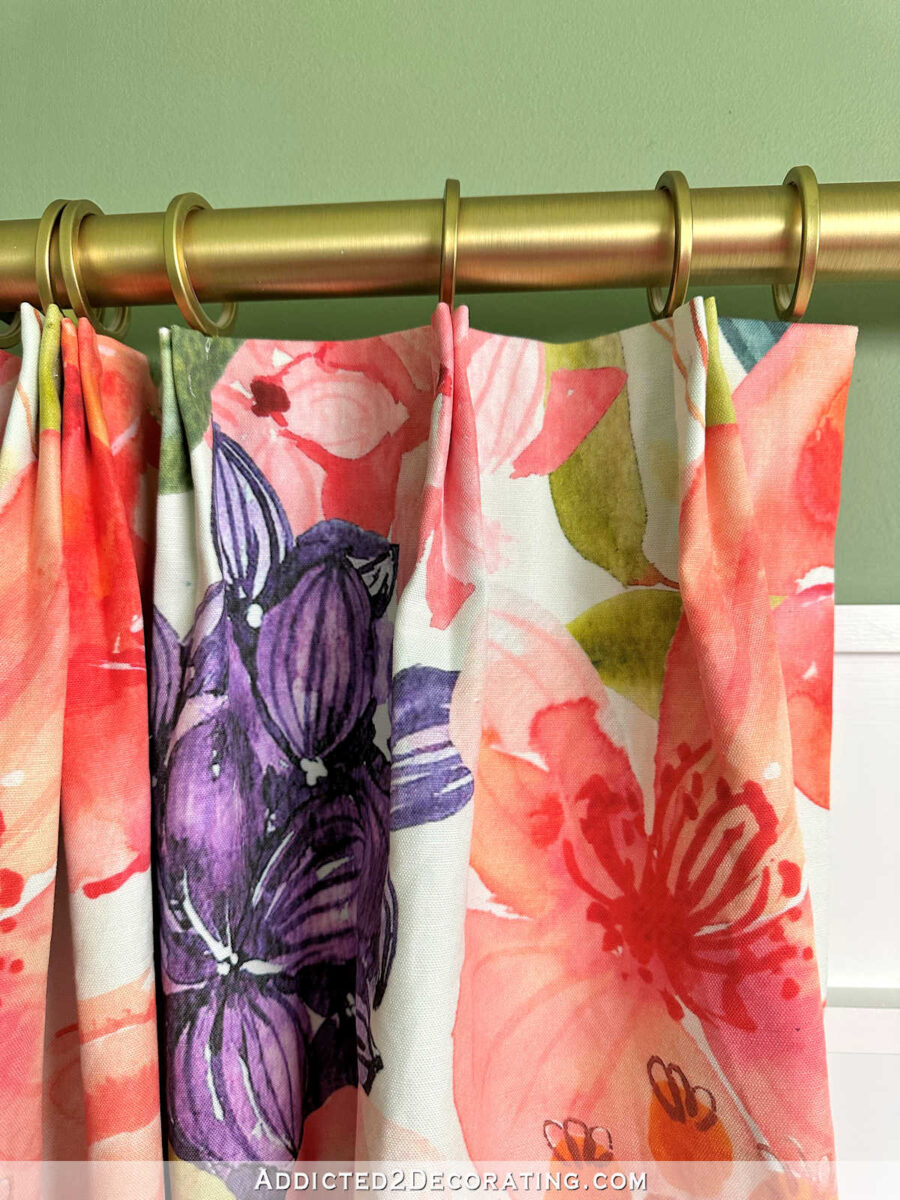
To do that, I merely introduced two pleats collectively…
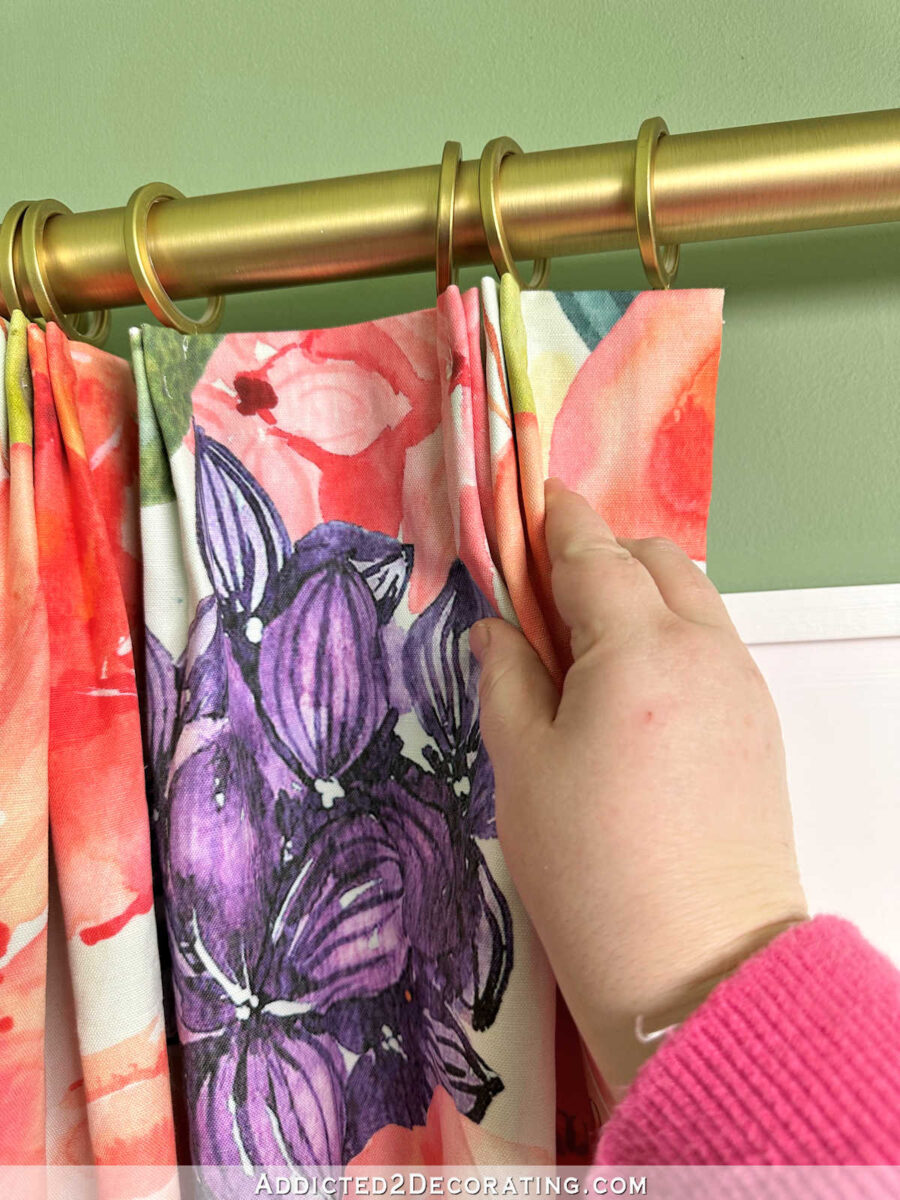
After which used my fingers to press in a crease within the header tape on the again.
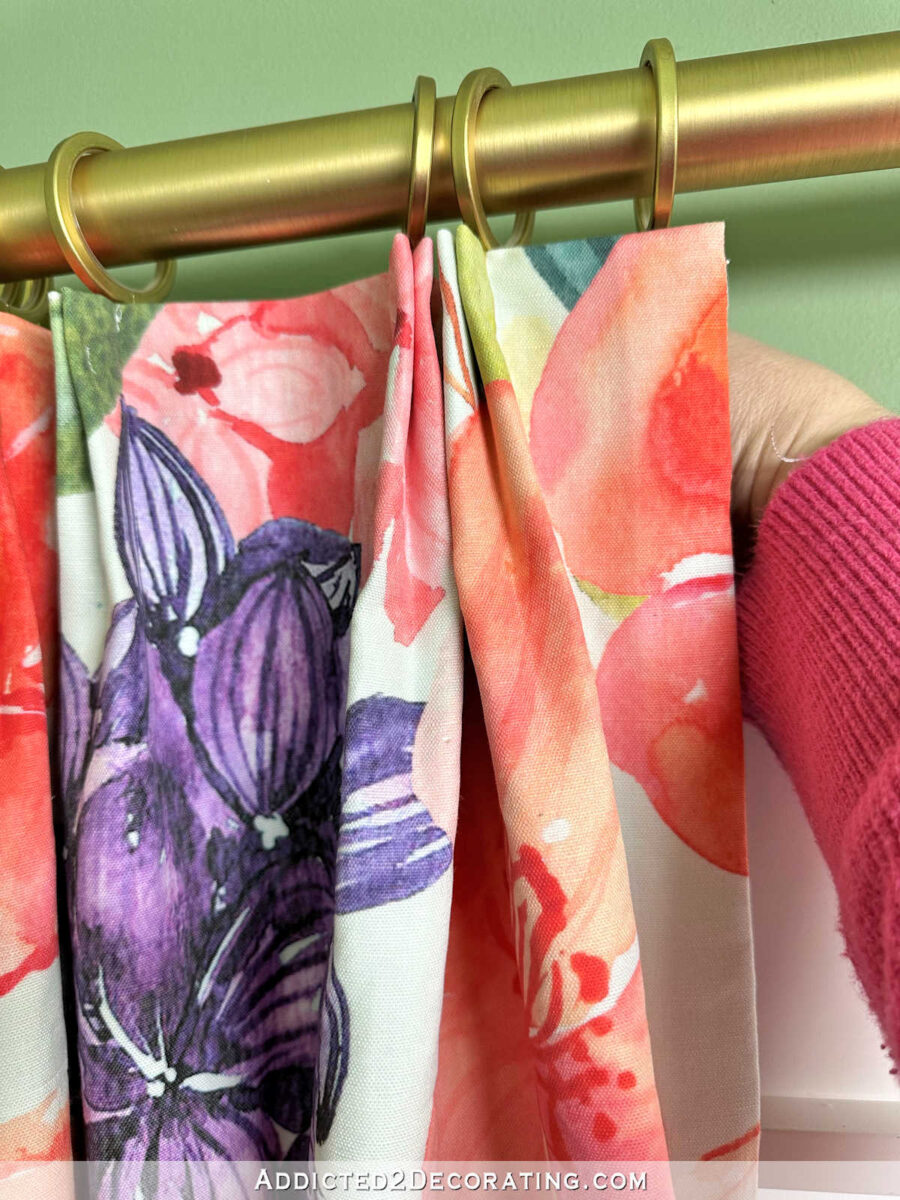
This can enable the rings to remain the place I need them to remain slightly than preventing me as I’m attempting to make changes.
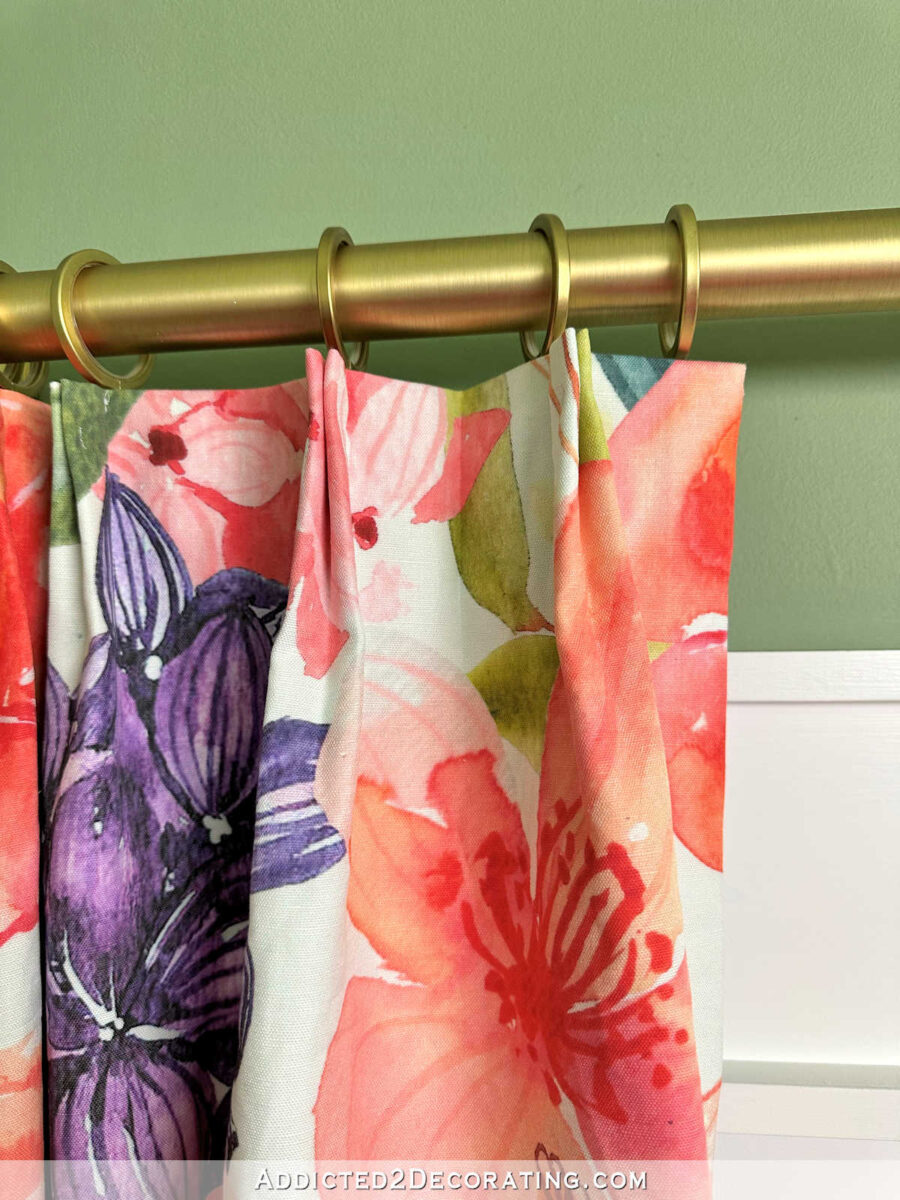
And at this level, the panel was completed and looking out stunning, if I do say so myself!
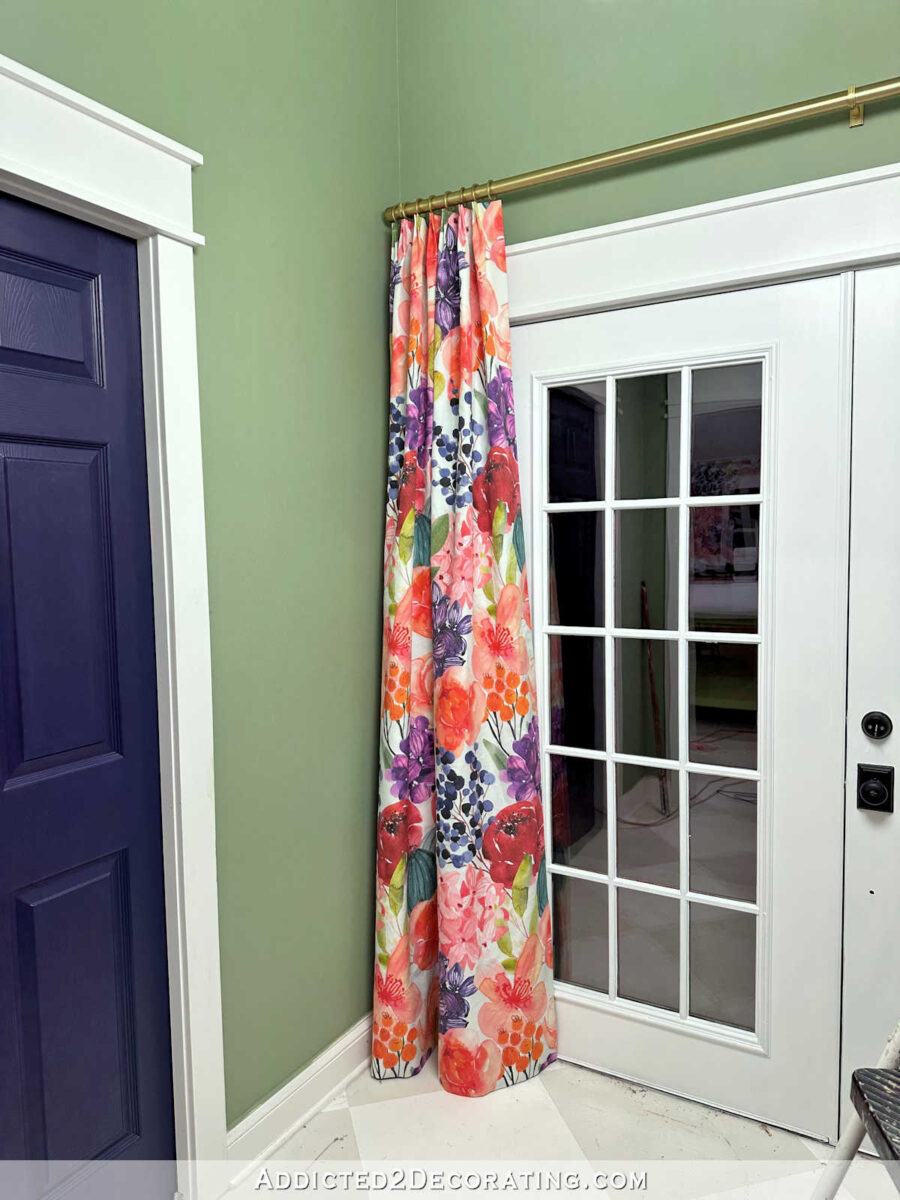
You possibly can determine at this level whether or not you desire a extra informal look, like what’s proven within the image above, the place the folds within the material look sort of carefree and are left to do what they naturally need to do.
Or in order for you a extra formal, polished, tailor-made look, you’ll have to “practice” your pleats and folds. Do that by beginning on the high and patiently folding the material consistent with the pleats. When you get a few foot or two down the panel, use some scrap material to tie the folds into place.

Proceed working your approach down till it’s tied in about three or 4 locations and appears like this…

You possibly can go away it like that for a day or two, or you’ll be able to velocity up the method through the use of a garments steamer or steam iron to steam in these folds.

And as soon as these folds are skilled, it’ll look extra like this…

I typically don’t like my creases too creased (as they appear above), so as soon as they’ve had a couple of days like that, I’ll typically get my steam iron and hit them with some steam whereas smoothing them out a bit in order that they appear extra like mild waves within the material as an alternative of harsher folds bordering on creases. However you’ll have to find out what your panel wants based mostly in your private style in addition to the material that you simply used.
I’m unsure which look I choose but, however I’m leaning in direction of the primary one for my studio. If I determine to go that route, I can simply use my steamer to get these folds out, after which floof the panel like a bridesmaid floofing a bride’s wedding ceremony costume and practice, and that’ll return it again to that extra pure, carefree look.
I hope this tutorial was useful! When you have ANY questions in regards to the course of, please let me know and I’ll do my absolute best to reply.
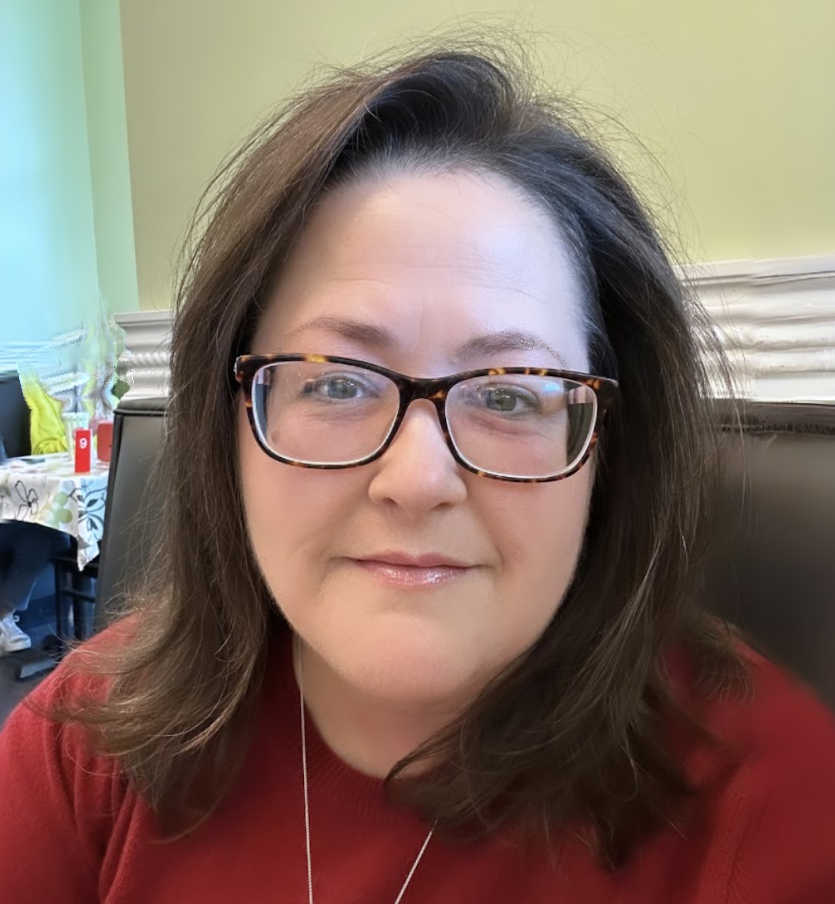
Addicted 2 Adorning is the place I share my DIY and adorning journey as I transform and beautify the 1948 fixer higher that my husband, Matt, and I purchased in 2013. Matt has M.S. and is unable to do bodily work, so I do the vast majority of the work on the home on my own. You possibly can be taught extra about me right here.
[ad_2]
Source link