[ad_1]
Higher identified within the business as Ray Akira, Kuala Lumpur-born Raymond Choo’s journey with music began on the age of 15—late, maybe, by some musicians’ requirements.
Nevertheless, that didn’t cease the person from pursuing music. Not one to restrict himself by genres, Ray is expert at classical guitar in addition to the fashionable electrical rock guitar.
He used to carry out on worldwide cruise ships, music pubs and bistros, TV reveals, and guitar recording classes.
However in 2009, Ray determined to take a break from these performances and based The Guitar Hospital, a guitar restore enterprise.
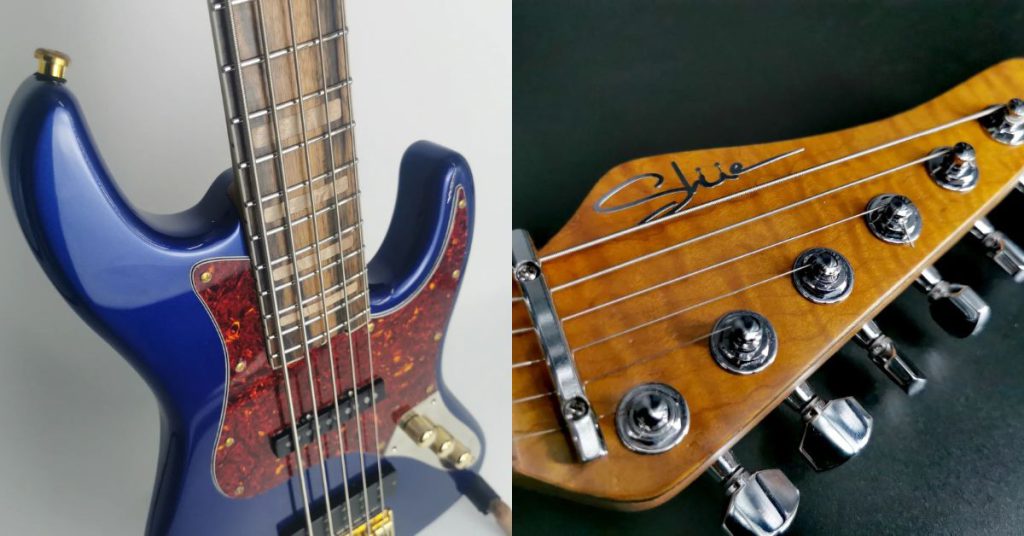
“I instructed myself that I need to focus extra on my enterprise, as guitar restore requires excessive focus and bodily energy,” he mentioned. “Nevertheless, the internal me of music nonetheless can’t cease me from taking part in guitar, so I’m nonetheless taking part in concert events for numerous artists from native to worldwide.”
Along with his ardour to carry out operating so deep, what acquired him to pursue a enterprise within the first place?
The physician is in
“As a full-time guitarist, our guitar is sort of a soldier’s weapon,” he defined.
And like troopers’ weapons, guitars undergo heavy utilization, thus requiring upkeep and repairs to ensure that them to do their responsibility.
“I used to ship my guitars to be repaired and serviced in different retailers, however my OCD all the time makes me refine it or typically have to redo it (primarily based on the information I acquired abroad whereas engaged on cruise ship).”
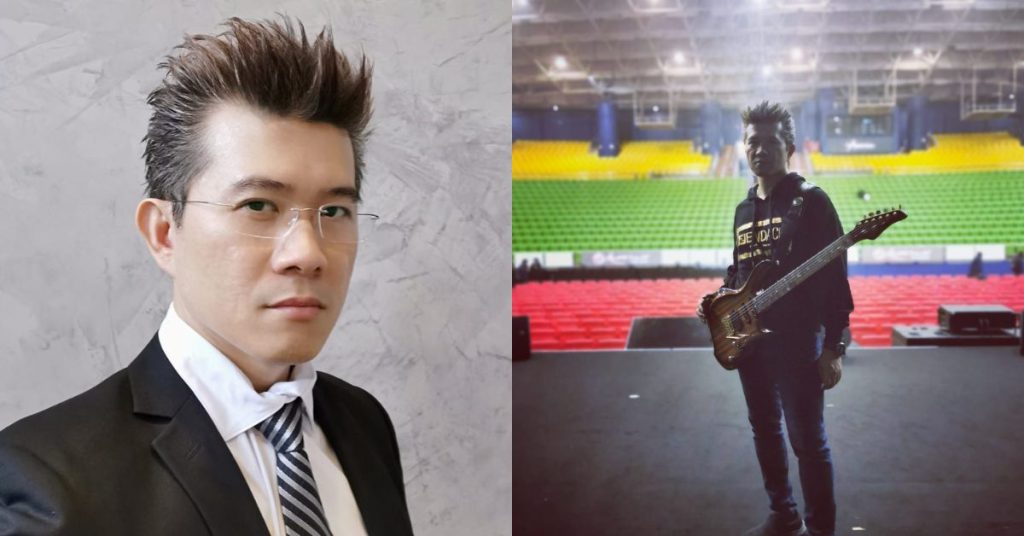
Slowly, Ray grew to become identified for his repairs, and his mates started to ask him for assist servicing or repairing their guitars. As this continued, the guitarist determined to start out his personal guitar restore store.
“Throughout the time, we accepted every kind of challenges that nobody within the business was prepared to do,” he mentioned.
This included restoring terribly broken guitars to appear as if nothing ever occurred, fixing damaged necks to flawless situation, or resolving lifeless guitar pickups.
To do all that and extra, Ray invested in lots of heavy-duty machines and costly instruments, equivalent to laser-cutting and CNC milling machines for precision repairs and customisations.
“Our repairs high quality has gained about 9,000 constructive critiques and nearly 200k followers on Fb,” the founder proudly mentioned.
In 2013, The Guitar Hospital began to provide high-end OEM guitars and basses for an Italian firm. In keeping with Ray, the crew constructed all the pieces from A to Z, from the wooden carving and milling to the programming and setups.
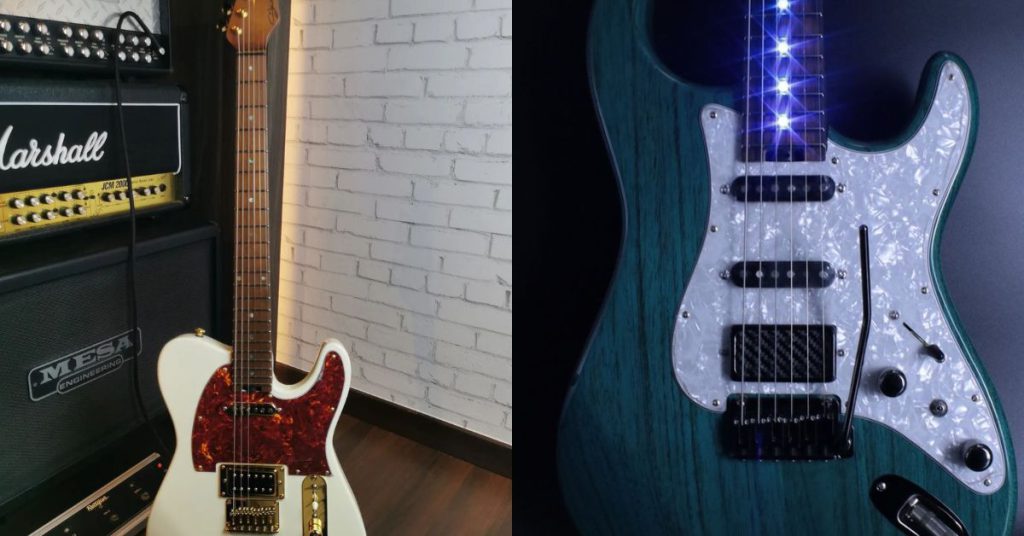
Nevertheless, since they have been doing these on an OEM foundation, the crew was not allowed to shout themselves out or take any credit score.
After seven years of doing this, Ray lastly determined to cease, and began up their very personal model, Shue Guitars.
A tropical sound
A very Malaysian product, Shue Guitars makes use of native wooden to make its guitars.
“We supply our wooden by means of our shut relationship with native wooden suppliers and connection in wooden and agricultural departments, plus mates in aboriginal communities,” he defined.
Having examined and in contrast many sorts of tropical wooden, the Shue Guitars crew has learnt that not each species is appropriate for guitar-making.
For instance, some woods have good resonance however are too heavy, whereas some woods are visually engaging however sound too mellow. Some woods are excellent, however have inconsistent provide.
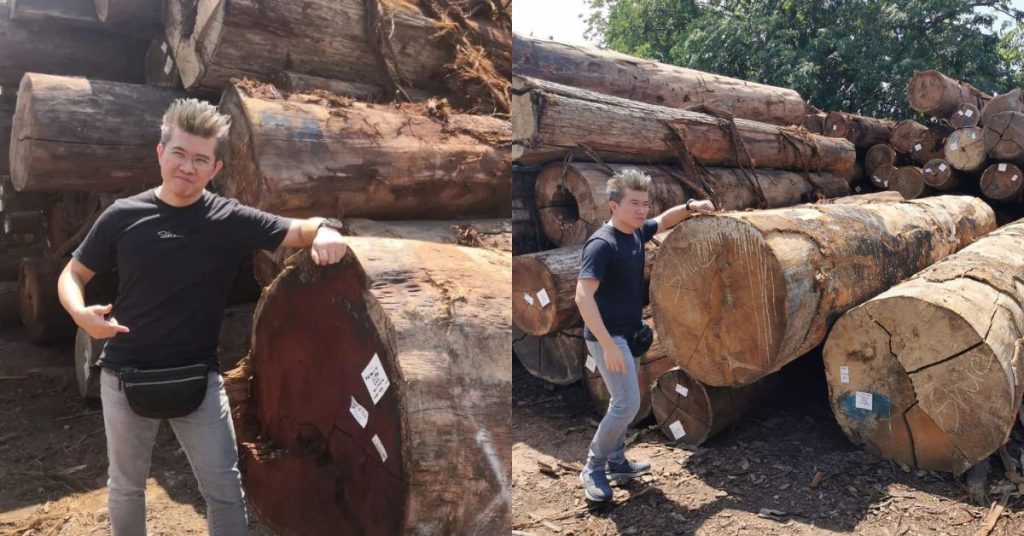
Ray expressed, “To fulfill the standards, it’s a lengthy journey, man.”
Whereas some might imagine wooden from the tropics is moister and thus not applicable for devices, tropical wooden has really been generally utilized in guitar making. That is very true for species equivalent to mahogany, rosewood, and ebony.
“The problem is the wooden processing methodology, and whether or not the wooden is processed correctly together with sawing, chemical remedies, vacuum stress therapy, kiln drying, and the storage setting,” Ray mentioned. “We’re very explicit about these particulars.”
Consideration to element
Shue Guitar’s guitars are all made to order. Sometimes, a consumer will first select the wooden they need from the model’s wooden library. Then, the crew will put together the design art work.
From there, it’s a matter of manufacturing the guitar—which entails slicing up all of the wooden, gluing the components collectively, sanding the physique, contouring the neck, fretting, and rather more.
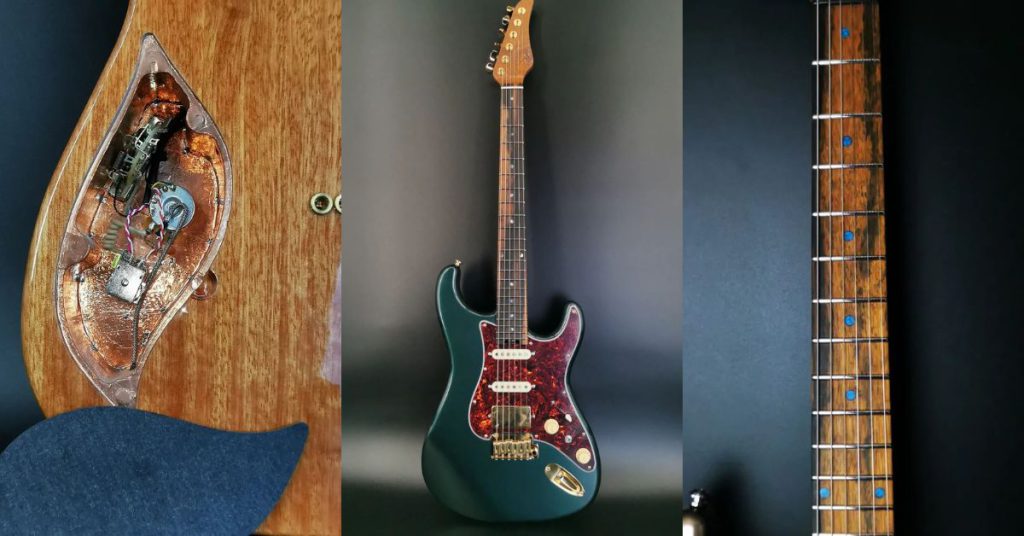
After that, it takes round 20 days for the ending touches. There’s additionally polish, buffing, physique shielding, pickup winding, and meeting to contemplate.
With all these processes in thoughts, the crew requires as much as six months to finish an order, relying on mannequin and materials availability.
At the moment, the Shue Guitar crew includes 10 folks, every specialising in a selected step of the method.
“At first, I personally taught and educated them, and I’ve all the time inspired them to try for perfection and excellence in all the pieces they do,” Ray shared. “Our crew is sort of a heat household; everybody works fortunately and strikes in the direction of the identical purpose.”
For professionals and hobbyists alike
Contemplating Shue Guitar’s prolonged course of, what makes shoppers select it over well-established guitar manufacturers?
“We’re extra explicit concerning the high quality of each guitar we construct,” Ray reasoned. “It have to be assembly the expectations of a severe musician or performer, by way of tone high quality, playability, comfortability, and preventability.”
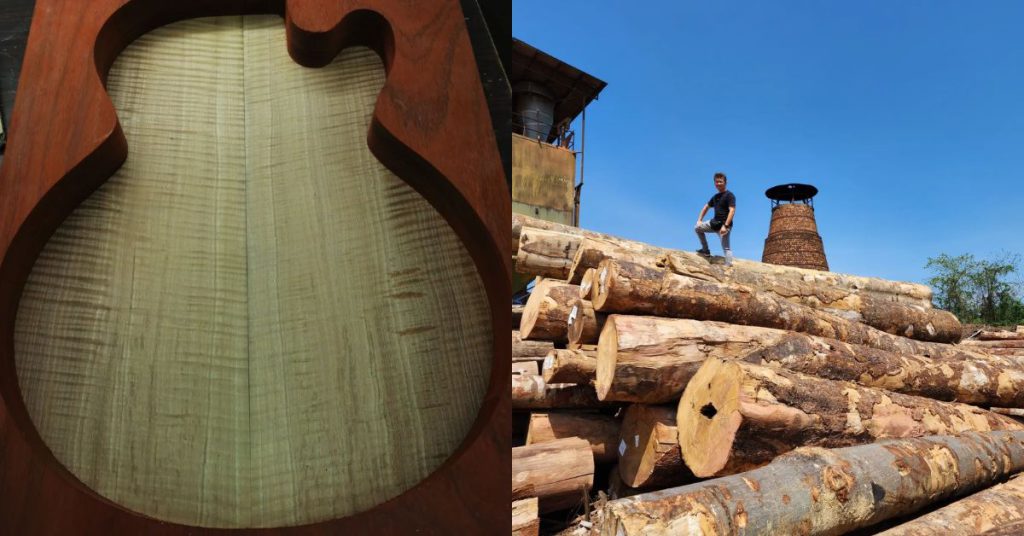
He believes that for many of the well-known manufacturers to fulfill these standards, it should set the client again US$5-10k.
And, Ray identified, you possibly can’t entry or select your supplies with these firms, except you purchase an air ticket to their areas.
“We’re principally a customized store with inexpensive costs with most customisation choices,” Ray mentioned. “And we’re prepared to hear and accommodate totally different gamers’ necessities.”
Shue Guitars’ fashions vary from RM5,300 to RM9,800, relying on the supplies and specs. Ray shared that the crew plans to launch a lower-range mannequin by the top of the yr, although.
For now, a majority of Shue Guitar customers (round 80%) are severe musicians {and professional} guitarists.
This consists of names equivalent to Jamie Wilson (who has performed for the likes of David Foster, JJ Lin, and extra), Sham Kamikaze (at present on tour with Jacky Cheung), and Nappie Hassan (at present touring with Malaysian rock icon Ella).
Huge names apart, Ray additionally shared that his “household” additionally will get assist from many guitar lovers and collectors, music college students, buskers, and instructors.
Shue Guitars is for everybody, “so long as they love a pleasant tone and delightful guitar”.
A worldwide phenomenon
These considering Shue Guitars must attain out by means of their social media, as they’re nonetheless designing an internet site for the worldwide market.
As of now, Shue Guitar’s crew of 10’s primary precedence is delivering the backlog of various customized orders.
“These customized orders take various time for our total operation,” the founder admitted. “Within the enterprise means, not a great signal.”
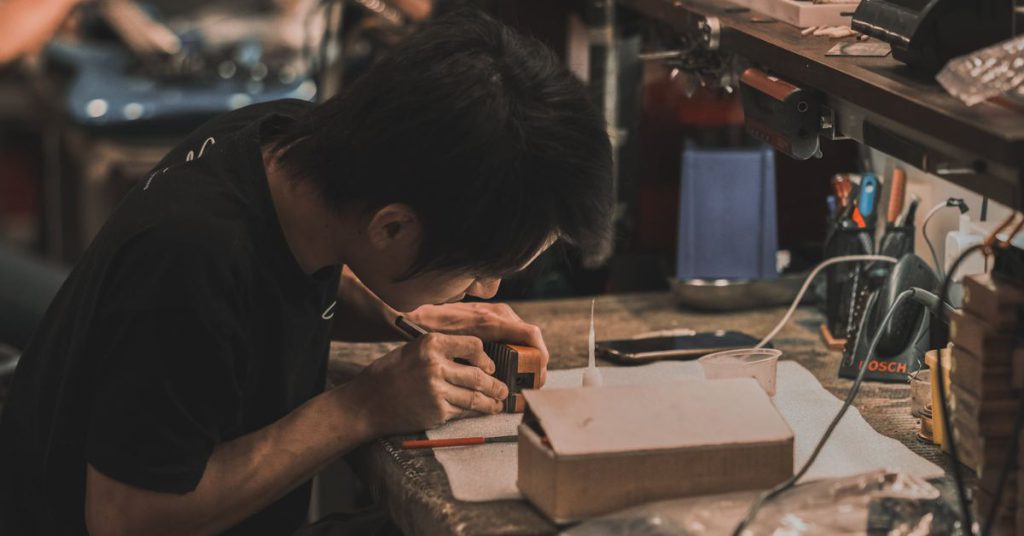
If the crew can solely produce 10 guitars a month, it could be a giant battle for them to make a big return or develop the enterprise, particularly contemplating their inexpensive costs.
Whereas chasing these backlogs, the crew will slowly roll out lower-range commonplace fashions. With that, they count on to develop their gross sales.
Backlogs apart, a problem Shue Guitars is combating is the prolonged lead time for the availability of sure components and supplies resulting from spillover results of the pandemic in addition to the warfare in Ukraine. This makes it tough for the crew to ship and obtain funds on time.
“That is additionally why we’re hesitant to interact in large-scale manufacturing of ordinary fashions and wholesale,” he mentioned.
That mentioned, the crew is working in the direction of implementing mass manufacturing as quickly as doable, making Shue Guitars extra accessible to the general public.
Within the greater scheme of issues, Ray hopes to determine Shue Guitar’s very personal large-scale automated manufacturing facility, bringing his Malaysian creations worldwide.
- Study extra about Shue Guitars right here.
- Learn different articles we’ve written about Malaysian startups right here.
Featured Picture Credit score: Shue Guitars
[ad_2]
Source link